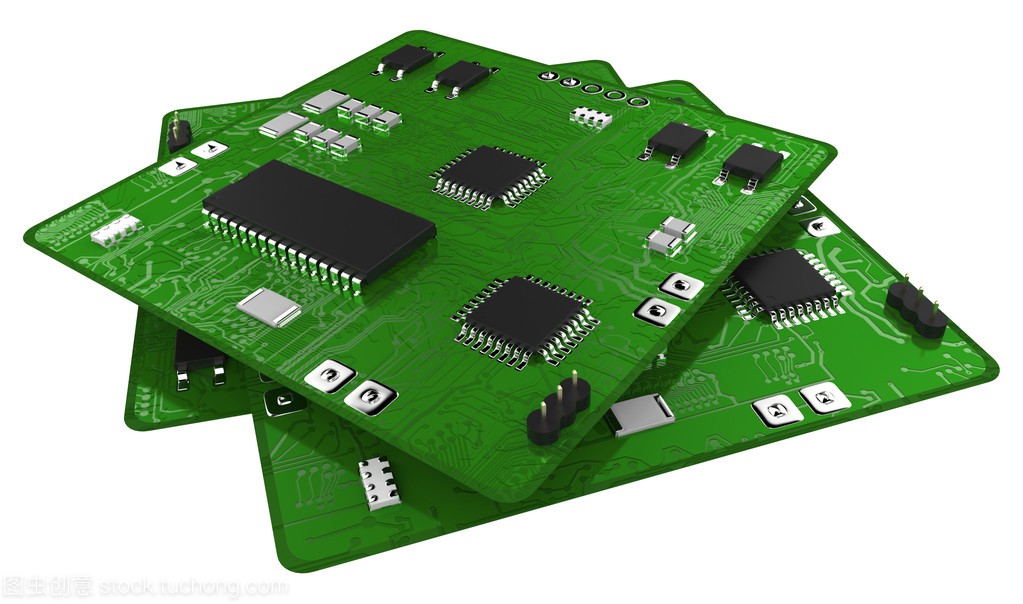
Circuit boards, also known as printed circuit boards or PCBS, can be found in every electronic device in the world today. In fact, the circuit board is considered the foundation of the electronic device because it is the place where the various components are held in place and connected to each other to make the electronic device work as intended.
In its simplest form, circuit boards are non-conductive materials with conductive tracks made of metal, usually copper, to physically support and electrically interconnect the components needed for electronic devices.
A design engineer working on a specific electronic device will create custom pattern conductive tracks (called traces) with similar characteristics of pads and holes into which the components will be mounted and interconnected. Since different devices require different components and interconnects to achieve the desired function, the pattern of copper tracks and conductive components on the substrate will vary from board design to board design.
More complex circuit boards will feature multiple layers of conductive copper tracks and interconnects sandwiched between non-conductive materials. As technology advances and the demand for electronic devices gets smaller with more functionality, engineers are pushing the boundaries of design and manufacturing capabilities to create boards with finer features, more conductive layers, and smaller and denser components. These advanced boards are often referred to as HDI or high-density interconnect PCBS.
What is a circuit board?
The most common non-conductive material circuit boards used to support etched copper tracks and conductive features are composites made of woven fiberglass cloth and epoxy resin. Surprisingly, the material is usually off-white rather than green. Later add green (or any other color) as one of the final steps in the board manufacturing process. This added layer of color, called solder marking, is used to protect the top and bottom layers of copper that would otherwise be exposed.
While a common substrate made of fiberglass and epoxy is sufficient for the needs of many electronic devices, it may not be suitable for others because not all devices are manufactured for the same purpose, application or environment. Many electronic devices require PCB substrates to meet certain characteristics, so more advanced or special types of substrates are needed. These requirements can include some degree of heat resistance, impact resistance, and brittleness, to name a few, but the list of attributes and qualifications can be extensive. Click on the links to learn more about the different types of materials that can be used in board manufacturing.
With the development of PCB manufacturing technology, it has become cheaper, faster, and more convenient to professionally manufacture printed circuit boards. Most PCB manufacturers require Gerber files to manufacture boards, which contain data, drawings and specifications for the specific board design to be produced.
PCB design automation software, such as Advanced Circuits PCB, enables design engineers to lay out their circuit board designs according to their needs and requirements, in order to later export data for their circuit board manufacturers. Manufacturers use electronic data and manufacturing drawings to set up automated equipment to produce boards with matching specifications and features.
General printing plate substrate materials can be divided into two categories: rigid substrate materials and flexible substrate materials. An important type of general rigid substrate material is copper clad plate. It is made of reinforced material, dipped in resin adhesive, dried, cut, laminated into blank, and then covered with copper foil, with steel plate as mold, in the hot press by high temperature pressing process. The general multilayer plate with semi-cured piece, is the copper clad plate in the production process of semi-finished products (mostly glass cloth dipped in resin, after drying processing).