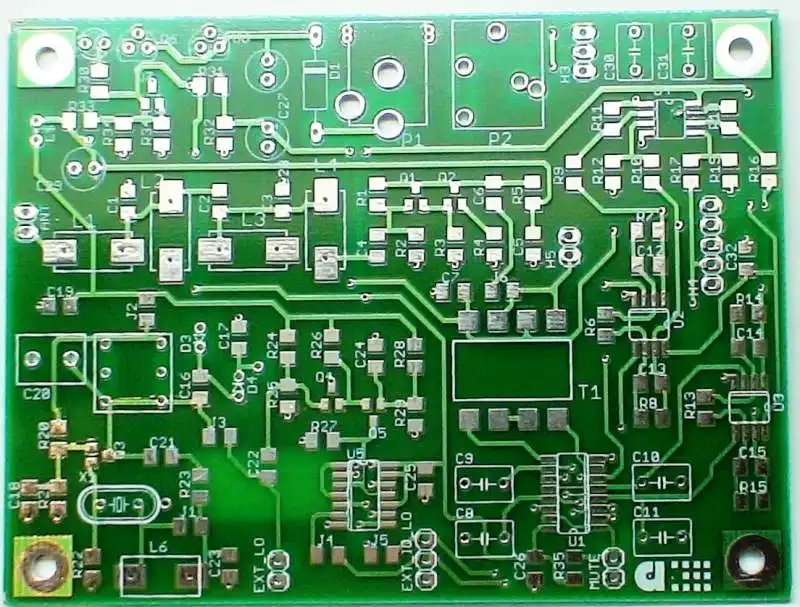
What are the optimization suggestions in wave soldering process
Wave soldering enables manufacturers to weld large printed circuit boards quickly and reliably. The wave soldering process is effective for both the traditional through hole PCB assembly method and the new surface mount method.
Wave soldering refers to the soldering of melted soft solder (lead tin alloy) into a solder wave required by the design through an electric pump or an electromagnetic pump. It can also be formed by injecting nitrogen into the solder pool, so that the printed board with components in advance can realize the soft soldering of mechanical and electrical connection between the component terminals or pins and the printed board pad through the solder wave.
The surface of the tin wave surface of the wave soldering tin furnace is covered by a layer of oxide skin, which almost remains static along the entire length direction of the solder wave. During the wave soldering process, the PCB contacts the front surface of the tin wave, the oxide skin breaks, and the tin wave in front of the PCB is pushed forward in folds, which indicates that the entire oxide skin and the PCB move the wave soldering point at the same speed for molding:
When the PCB enters the front end (A) of the wave surface, the base plate and the pin are heated, and before leaving the wave surface (B), the entire PCB is immersed in solder, that is, bridged by solder. But at the moment of leaving the wave end, a small amount of solder adheres to the bonding pad due to the wetting force, and due to the surface tension, a small state of shrinking with the lead wire as the center appears. At this time, the wetting force between solder and bonding pad is greater than the cohesion of solder between two bonding pads. Therefore, a full and round solder joint will be formed, and the excess solder leaving the wave tail will fall back into the tin pot due to gravity.
Wave soldering process: insert the element into the corresponding element hole → precoat flux → pre bake (temperature: 90-1000C, length: 1-1.2m) → wave soldering (220-2400C) → cut off redundant plug-in pins → check.
As the volume of electronic products is becoming smaller and smaller, the precision of the entire assembly of PCBA is getting higher and higher, which leads to the fact that the volume of the entire electronic components can no longer be described as small, but directly small components. In addition, due to the influence of process, solder materials, PCB quality, equipment and other factors on the welding quality during wave soldering, there are many defects that cannot be seen by the naked eye during wave soldering, which are generally not easy to find during appearance inspection. After being handed over to the customer, solder joints often fail in advance due to power on, vibration, environmental temperature changes and other factors during the use process.
As the volume of electronic products is becoming smaller and smaller, the precision of the entire assembly of PCBA is getting higher and higher, which leads to the fact that the volume of the entire electronic components can no longer be described as small, but directly small components. In addition, due to the influence of process, solder materials, PCB quality, equipment and other factors on the welding quality during wave soldering, there are many defects that cannot be seen by the naked eye during wave soldering, which are generally not easy to find during appearance inspection. After being handed over to the customer, solder joints often fail in advance due to power on, vibration, environmental temperature changes and other factors during the use process.
What are the optimization suggestions in wave soldering process
Some suggestions on wave soldering process:
1. Many defects of wave soldering clock are related to PCB design, and DFM must be considered
2. Many defects are related to the quality of PCB and SMD processing components, so as to avoid the impact of counterfeit components on the quality. Qualified suppliers and controlled logistics and storage conditions shall be selected.
3. Many defects are caused by insufficient flux activity. A good flux can withstand high temperature, prevent bridging, and improve the tin permeability of through-hole.
4. The wave soldering temperature shall be set as low as possible to prevent overheating of components and material damage, especially to control the secondary tin melting in the mixing process.
5. Low solder temperature can reduce solder oxidation, reduce tin slag, and reduce the erosion of molten solder on solder tank and impeller. The formation of FeSn2 crystal is limited.
6. Excellent process control can reduce the defect level. Comprehensive adjustment of process parameters shall be carried out and the temperature curve must be controlled.
7. Pay attention to the maintenance of solder in the tin furnace, and strengthen the daily maintenance of equipment.