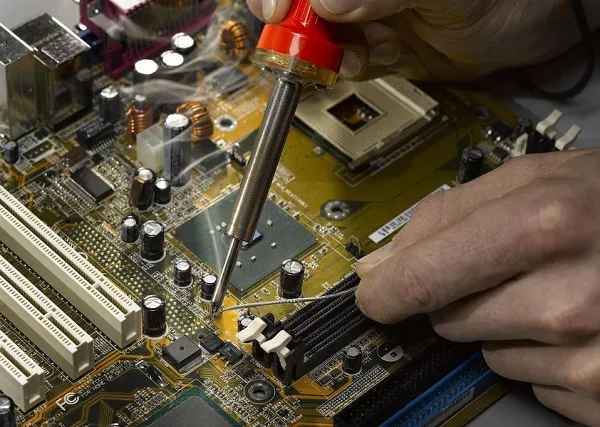
PCBA is a series of processing processes such as PCB circuit board manufacturing, component procurement and inspection, SMT patch processing, plug-in processing, program firing, testing, aging and so on. PCBA processing process involves more links, we must control the quality of each link to produce good products.
1. PCB circuit board manufacturing
After receiving the order of PCBA, analyze the Gerber file, pay attention to the relationship between the hole spacing of PCB and the bearing capacity of the board, do not cause bending or breaking, whether the wiring considers the high-frequency signal interference, impedance and other key factors.
2. Procurement and inspection of components
Procurement of components requires strict control of channels, must be from large traders and the original factory to pick up goods, 100% to avoid second-hand materials and fake materials. In addition, a special incoming inspection post is set up to strictly check the following items to ensure that components are faultless.
PCB: reflow welding furnace temperature test, no flying line, hole plugging or ink leakage, whether the board surface is bent, etc.
IC: Check whether the screen printing is completely consistent with the BOM, and keep at constant temperature and humidity; Other common materials: check the screen printing, appearance, power measurement value, etc. Check items according to the spot inspection method, the proportion is generally 1-3%.
3, SMT SMT processing
The temperature control of solder paste printing and reflow welding furnace is the key point. It is very important to use laser steel mesh with good quality and in line with process requirements. According to the requirements of PCB, some steel mesh should be enlarged or reduced, or U-shaped hole should be used to make steel mesh according to the technological requirements. Furnace temperature and speed control for reflow is critical for solder paste infiltration and welding reliability, and can be controlled according to normal SOP operating guidelines. In addition, AOI testing needs to be strictly implemented to minimize the adverse effects caused by human factors.
4. DIP plug-in processing
In the plug-in process, the mold design of over wave welding is the key point. How to use the mold to maximize the probability of providing good products after the furnace is a process that PE engineers must constantly practice and summarize experience.
5. Program firing
In the previous DFM report, the client can be advised to set up some test points on the PCB, in order to test the PCB and PCBA circuit conductivity after all components are welded. If there are conditions, you can ask the customer to provide the program, through the burning device to burn the program into the main control IC, you can more intuitively test the various touch action brought by the functional changes, in order to test the integrity of the whole PCBA function.
6. PCBA board test
For orders with PCBA test requirements, the main test contents include ICT, FCT, aging test, temperature and humidity test, drop test, etc., which can be operated according to the customer's test plan and the report data can be summarized.
PCBA patch processing is formed by a variety of assembly processes, according to the different types of customer products, the assembly process requirements are also different. The process flow of PCBA processing can be roughly divided into SMT patch, DIP plug-in, PCBA test, finished product assembly; These four processes are essential and the most important. Next, Shenzhen PCBA processing plant One Nine forty-two technology for you to elaborate on the four important process flow, hope to bring you some help!
PCBA
First, SMT SMT process
In the process of SMT, electronic components were purchased according to the BOM provided by the customer. After confirming the production plan, process documents were issued, SMT programming, steel mesh production, material preparation and on-line were started. SMT SMT process is: solder paste printing →SPI test → patch →IPQC first check → reflow soldering →AOI test; In SMT SMT process, we should focus on the control of solder paste printing quality and reflow furnace temperature, 70% of SMT SMT defects are from the printing and reflow temperature parameters.
Second, DIP plug-in process
Due to the precision of current electronic products, there are very few plug-in components in PCBA processing (except for the type of power board), which are generally done by manual plug-in. DIP plug-in process: distribution of electronic components at the station → plug-in →IPQC first piece check → loading of jig → wave soldering → cutting foot → repair welding → plate washing → full appearance inspection; In the DIP plug-in process, we should focus on controlling the orientation of the plug-in components and whether the components float when the jig is loaded.
3. PCBA test process
PCBA test is the most critical quality control link in the whole PCBA processing process. It is necessary to strictly follow the PCBA test standard and test the test points of the circuit board according to the customer's test scheme. There are four main types of PCBA test: ICT test, FCT test, aging test, and reliability test.
Iv. Finished product assembly process
The finished product assembly process is a process of assembling the shell of the PCBA board in good condition. The finished product surface is not scratched and then the finished product is tested. Finally, the electrostatic packaging is completed. The finished product assembly process must be in strict accordance with the engineer's product operation instructions and procedures, ignoring a process will increase manufacturing costs.
PCBA processing process is a link link, any problem will have a great impact on the quality of the whole product, so it is necessary to strictly control the process of each process to avoid the outflow of unqualified products. The above content is provided by Shenzhen SMT Processing plant - One Nine Forty-two Technology. For more knowledge about PCBA processing, please visit Shenzhen One Nine Forty-Two Technology Co., LTD.