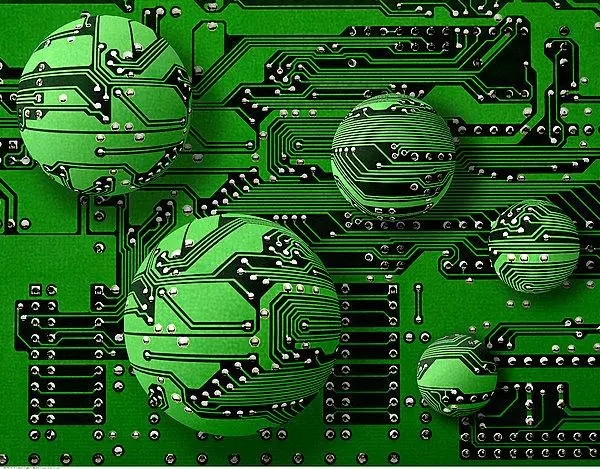
PCB process Detailed explanation of PCB cleaning process
PCB manufacturer and PCB designer explain PCB cleaning process
1. Cutting: cut large sheets into small ones
Plate washing: wash and air dry the dust and impurities on the plate machine.
2. Inner layer dry film: a layer of photosensitive material is pasted on the copper foil on the board, and then the circuit diagram is formed after exposure and development of the black film.
Chemical cleaning:
(1) Remove oxides and garbage on Cu surface; Roughly use Cu surface to enhance the adhesion between Cu surface and photosensitive materials.
(2) Process: degreasing - water washing - micro etching - high-pressure water washing - circulating water washing - water absorption - strong wind drying - hot air drying.
(3) Factors affecting plate washing: degreasing speed, degreasing agent concentration, micro etching temperature, total acidity, Cu2+concentration, pressure, speed.
(4) Vulnerable defects: open circuit - poor cleaning effect, resulting in film throwing; Short circuit - garbage generated if it is not clean.
3. Copper sinking and plate electricity
4. Outer dry film
5. Pattern Plating: Carry out in hole and line circuit to meet the requirements of copper plating thickness.
(1) Degreasing: remove the oxidation layer and surface contaminants on the board surface;
(2) Acid leaching: remove pollutants in pretreatment and copper cylinder;
6. Circuit board charge:
(1) Degreasing: remove grease and oxides on the surface of the circuit diagram to ensure that the copper surface is clean.
7. Wet green oil:
(1) Pretreatment: remove the surface oxide film and roughen the surface to enhance the adhesion between green oil and circuit board surface.
8. Tin spraying process:
(1) Hot water washing: clean dirt and some ions on the surface of PCB;
(2) Brushing: further clean the residual debris on the circuit board surface.
9. Gold precipitation process:
(1) Acid degreasing: remove the light grease and oxide on the copper surface to activate and clean the surface and form a surface state suitable for nickel gold plating.
10. Circuit board contour processing
(1) Plate washing: remove surface contaminants and dust. 11. NETEK copper surface treatment
(1) Degreasing: remove grease and oxides on the surface of the circuit diagram to ensure that the copper surface is clean.
Steps to clean the copper surface:
1. Dry film pressing
2. Before inner layer oxidation treatment
3. After drilling (remove the glue residue, and remove the colloid produced during drilling to coarsen and clean it) (mechanical grinding plate: fully clean the hole with ultrasonic cleaning, and remove the copper powder and adhesive particles in the hole)
4. Before chemical copper
5. Before copper plating
6. Before green paint
7. Before tin spraying (or other welding pad treatment process)
8. Before gold finger nickel plating
Secondary copper pretreatment:
Degreasing - water washing - micro etching - water washing - acid leaching - copper plating - water washing will remove the oxidation, fingerprints, minor objects and other impurities that may be left on the board surface during the production of the outer circuit board in the previous process. And with the surface activation, so that the adhesion of copper plating is good.
Before shipment, a cleaning shall be carried out to remove ion pollution.