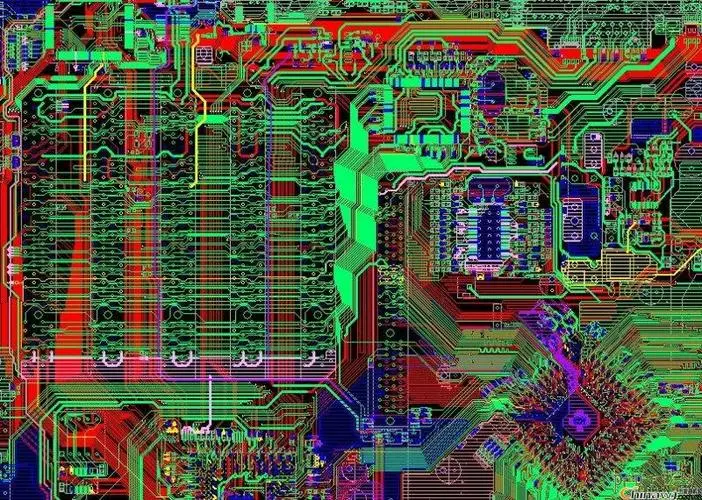
The copper plating layer with copper plating protective agent is not so easy to be oxidized in the air, and it is extremely easy to be oxidized if not used. Cause analysis shows that it is very easy to be oxidized and lose luster, and copper is soft and easy to be activated, which can form good metal metal bonding with other metal coatings, so as to obtain good adhesion between coatings. Therefore, copper can be used as the bottom layer of many metal electrodeposits, and copper plating plays an important role in the production of printed boards. Copper plating of printepd circuit board includes electroless copper plating and electroplating copper, among which copper electrolating is an important process in PCB manufacturing. This article mainly introduces PCB copper electroplating technology, PCB operation technology problems that should be paid attention to, and the causes of some common failures and solutions.
The measures to eliminate such faults include: controlling the proportion of brightener consumption in the plating solution according to the Hall cell test or the workpiece condition; Don't think that the more brighteners, the better the brightness. When the brightener is excessive, there will be a clear boundary between bright and not bright in the low current density area, and the coating of complex parts will be flecked. When the more brightener is added, the less bright it will be. At this time, if the brightness is improved by adding a small amount of hydrogen peroxide, some brighteners should be removed. For any electroplating additive, we must adhere to the principle of adding less and adding more frequently.
There are many brighteners (such as M, N type copper plating), so it is necessary to accumulate appropriate brightener composition ratio in long-term PCB production practice. Experience shows that the ratio of cylinder opening agent and supplement for bright copper plating is very strict, the consumption of sodium polysulfide dipropane sulfonate in the plating solution is large at different bath temperatures, and the consumption ratio of M to N is also different. In order to obtain a general ratio of supplements, only the ratio at 25 ℃~30 ℃ can be considered. The most ideal situation is to prepare various brighteners into standard dilute solutions, and frequently use the Hall cell for test adjustment.
Control the chloride ion content in the plating solution. If it is suspected that the fault is caused by the chloride ion in the plating solution, it should be confirmed by test first. It is also very important not to blindly add hydrochloric acid in the large tank to adjust and control the content of copper sulfate and sulfuric acid in the plating solution, and they are related to anodic dissolution and anode phosphorus content.
The accumulation of brightener decomposition products in the plating solution will result in poor brightness leveling property of the coating and low current density area is not bright. When it is found that the consumption of brightener with the same ratio is much higher than the normal value at the same bath temperature, it should be suspected that there are too many organic impurities. There is too much organic solvent, and there is no copper powder in the plating solution;, However, the PCB coating will precipitate copper powder precipitates with poor adhesion. At this time, deal with the organic impurities in the plating solution. In addition, do not neglect the adverse effects of organic impurities on the brightness of low current density areas. The sensitivity to organic impurities is particularly strong when the current is small. Practice has proved that for the bright copper plating solution that has not been treated for a long time, if only 39/L high-quality activated carbon is used to adsorb organic impurities, the full bright range of Hall cell test piece in the low current density area may be expanded by several millimeters.
This article mainly introduces PCB copper electroplating technology and PCB operation technology problems that should be paid attention to