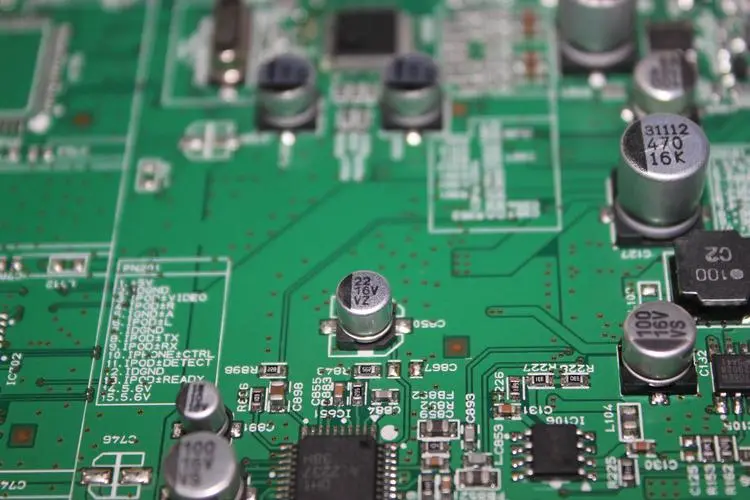
This paper discusses the key steps to build a PCB low EMI prototype before microwave anechoic chamber conformance testing, including the design of low radiation circuits and pre compatibility testing. Pre compatibility testing includes simulation and EMI analysis of the printed circuit board (PCB) layout model using 3D electromagnetic field simulation software, and near-field electromagnetic scanning of the prototype PCB using spectrum analyzer (SA). Finally, the microwave anechoic chamber test was performed to verify the design.
Minimum EMI circuit design
To ensure low emissivity (RE), best practices must be applied when designing circuit schematics and PCB layouts, including adding ferrite beads to power supply circuits, USB data lines, Ethernet and other signals to filter EMI. In addition, a sufficient number of decoupling capacitors can be properly placed on the power supply circuit to minimize the impedance of the power distribution network, thereby reducing the noise ripple amplitude generated by the digital load and reducing the radiation risk. At the same time, optimizing the design of the closed loop compensation network of the switching power supply to achieve a stable closed loop can ensure that the voltage output is controllable and the switching noise ripple amplitude is reduced to the maximum. The reduction of noise ripple amplitude can significantly reduce the EMI risk of the prototype.
PCB routing of high frequency or fast rising/falling edge signal shall refer to continuous circuit (such as reference ground plane) to reduce EMI risk. The routing shall not pass through any split plane or hole. If signals need to be transmitted between layers through vias, at least one grounding vias shall be placed adjacent to the signal vias as the return path of signal current from the receiving end to the transmitting end. If there is no proper return path, the return current may be transferred randomly in the PCB and become a potential EMI source.
Excellent grounding scheme is also the key factor to minimize EMI. All PCB designs must avoid grounding loops, because grounding loops will form radiation transmitters when the return signal current passes through. An excellent grounding scheme can be constructed by designing the grounding as a wide reference plane. The ground plane of different circuit groups (such as RF, analog and digital circuits) shall be physically isolated and circuit connections shall be established through ferrite beads to help prevent high-frequency noise from spreading between circuit groups.
After PCB layout design is completed, simulation shall be performed for EMI analysis to ensure that PCB has low radiation emission risk before manufacturing. Omitting EMI simulation may not guarantee the EMI performance of PCB, which will lead to redesign. If the EMI simulation results meet the technical specification requirements, the designer can start PCB manufacturing, and then use the spectrum analyzer to perform near-field electromagnetic scanning on the prototype PCB. Pre compatibility tests such as EMI simulation and near-field electromagnetic scanning can increase the confidence of designers and ensure that the prototype has low EMI. After completing the pre compatibility test, the tested device can perform the actual microwave anechoic chamber EMI consistency test.
Simulation EMI analysis
After completing PCB layout design, import the layout file into EMPro 2013.07 to execute 3D EMI simulation. The finite element method (FEM) is used to simulate the three-dimensional electromagnetic field by selecting the differential signal. Three dimensional electromagnetic field simulation is the process of setting electromagnetic boundary conditions and model mesh size and solving Maxwell equation. To ensure the accuracy of simulation results, the boundary size should be set to more than 8 times the PCB thickness, and the grid size should be set to less than 1/5 of the PCB width. Computers running three-dimensional electromagnetic fields need to be configured with more than 16G of memory and more than 100G of storage capacity to ensure smooth analysis.
Set the far field sensor to capture the emission electromagnetic field, calculate the far field emission power using the EMI simulation template of EMPro, and then set the electric field probe with a distance of 10m to draw the frequency domain response diagram. Then, the three-dimensional electromagnetic field simulation of the finite difference time domain (FDTD) mode is performed, and the simulation results are compared with those of the FEM mode.
See the electric field intensity simulation diagram (Figure 1) of 30MHz~1GHz frequency (electric field intensity unit: dB μ 5. Frequency unit: GHz), the radiated power level (the blue curve is FEM mode simulation, and the red curve is FDTD mode simulation) is lower than about 45dB μ Maximum FCC threshold of V (dashed green line).
Near field electromagnetic measurement
After the prototype PCB is made and assembled, the near-field electromagnetic scanning of the prototype is performed using a spectrum analyzer. The single turn coil connected to the spectrum analyzer captures the near-field emitted by the prototype. Figure 2 shows the frequency domain signal in the frequency range of 30MHz~1GHz (the power level of electromagnetic field is in dB, and the frequency is in Hz).
Peak of maximum power intensity (- 66.4dBm) appears near 400MHz. The coil acting as the near-field sensor moves within 3 inches of the device under test. The resolution bandwidth of 30kHz spectrum analyzer can realize low background noise (- 80dBm) measurement, so the spike (radiation of different discrete frequencies) is clearly visible. To enhance the confidence of the prototype in passing the far field (3m and 10m) EMI consistency test in the microwave anechoic chamber, the near field peak power should be lower than - 65dBm.
EMI conformance testing
Results of 3m far field EMI consistency test of prototype in microwave anechoic chamber. The red line shows the maximum radiated emission power level of CISPR 11 Class A: less than 56dB in the frequency range of 30MHz~1GHz μ V。 The brown curve below the red line indicates the protection frequency band specified in the EMC guidelines of TechnoTech (formerly Agilent). The vertical and horizontal components of the radiation wave are represented by blue and green curves, respectively. 38dB at 400MHz and 560MHz μ V and 37 dB μ The peak power of V is lower than the maximum threshold.
Summary
Low EMI circuit design and pre compatibility testing (such as 3D EMI simulation and near-field electromagnetic scanning) are very important, which can avoid unnecessary PCB remanufacturing, save development cost and time, shorten the time for EMI consistency testing in microwave anechoic chambers, and ensure that electronic devices are put on the PCB market on time or even in advance.