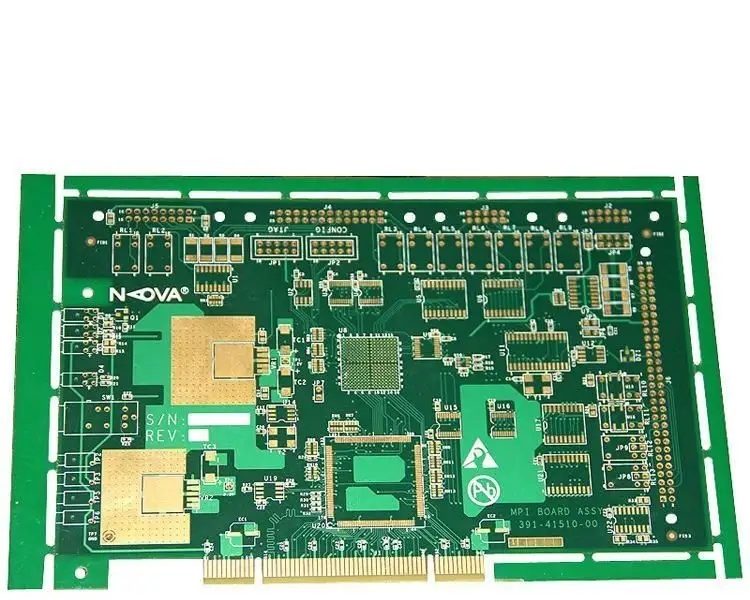
Circuit board manufacturer explains how to disassemble and solder BGA chip
1、 Disassembly of BGA chip
1. Do a good job of element protection. During desoldering, wet cotton wads can be placed on adjacent ICs. Many plastic power amplifiers and soft package word banks have poor high temperature resistance, so the temperature is not easy to be too high during blow welding, otherwise, they are easy to be blown out.
2. Remember to put an appropriate amount of flux on the IC to be removed and blow it into the bottom of the IC as far as possible, so that the ridge can help the solder joints under the chip melt evenly.
3. Adjust the temperature and wind force of the hot air gun. The general temperature is 3-4 gears, and the wind force is 2-3 gears. The air nozzle moves about 3cm above the chip for heating until the tin bead under the chip is completely melted. Use tweezers to clamp the entire chip. Note: When heating the IC, blow around the IC, not in the middle of the IC, otherwise it is easy to blow up the IC, and the heating time should not be too long, otherwise the circuit board will bubble.
4. After the BGA chip is removed, there is residual tin on the bonding pad of the chip and the machine board. At this time, add sufficient solder paste on the PCBA board, use an electric soldering iron to remove the excess solder on the board, and properly apply tin to make each solder leg of the circuit board smooth and round. Then use Tianna water to clean the solder flux on the chip and the machine board. Be careful when removing solder, otherwise the green paint on the bonding pad will be scraped off or the bonding pad will fall off.
2、 Tin planting
1. Get ready. The soldering tin on the IC surface can be removed by adding an appropriate amount of soldering paste on the BGA IC surface, removing the excessive soldering tin on the IC with an electric soldering iron, and then putting the IC into Tianna water for cleaning. After cleaning, check whether the IC solder joints are bright. If there is some oxygen, use an electric soldering iron with flux and soldering tin to make them bright for tin planting.
2. There are many fixing methods for BGA IC, and the following two practical and convenient methods are introduced: the label paper fixing method: align the IC with the hole of the tin plate, stick the IC and the tin plate firmly with the label sticker, after the IC is aligned, press the tin plate firmly with your hand or tweezers, and then scrape the paste and tin with the other hand.
Fixation method of placing napkin under the IC: place several layers of paper towels under the IC, align the tin planting plate hole with the IC foot, press the tin planting plate firmly with hands or tweezers, and then scrape the tin paste.
3. Apply tin paste. If the tin paste is too thin, it is easy to boil during blowing and soldering, resulting in difficulty in balling. Therefore, the more dry the tin paste, the better. As long as it is not so dry that it becomes hard and lumpy, if it is too thin, it can be dried by pressing with napkin paper. Usually, you can pick some tin paste and put it on the inner cover of the tin paste to let it dry naturally. Use a flat blade to pick up a proper amount of tin paste on the tin planting plate, scrape down with force, and press while scraping to make the tin paste evenly fill the holes in the tin planting plate.
4. Adjust the wind power of the hot air gun to gear 2, shake the air nozzle to slowly and evenly heat the tin plate, so that the tin paste can slowly melt. When tin balls are found in individual holes of the tin plate, the temperature is in place. At this time, the hot air gun should be raised to prevent the temperature from rising further. Excessive temperature will make the tin paste boil violently, which will lead to tin planting failure. In severe cases, the IC may be overheated and damaged. If the blowing soldering is successful, it is found that some tin balls are not evenly watered, or even some tin is not applied, first use a scraper to flatten the exposed part of the oversized tin ball along the surface of the tin plate, then use a scraper to fill the holes with tin paste that are too small and missing, and then use a hot air gun to blow again. If the water in the solder ball is uneven, repeat the above operation until the ideal state is reached. For the replanting amount, the tin plate must be cleaned and wiped dry. When removing the tin plate, press it down at the four corners of the IC with the tip of a pair of tweezers while it is hot, so that it can be easily removed.
3、 Installation of BGA chip
1. First, apply a proper amount of solder paste on the side of BGA IC with solder legs. Adjust the temperature of the hot air gun to gear 2 and blow gently to make the solder paste evenly distributed on the IC surface. So as to position the tin bead of IC for welding. Then adjust the temperature of the hot air gun to gear 3, heat the machine plate first, and blow the flux. Then place the BGA IC with solder beads on the circuit board according to the position before removal. At the same time, move the IC back and forth, left and right, with hands or tweezers, and gently pressurize it. At this time, you can feel the contact between the solder legs on both sides. After alignment, the IC will not move because a little solder paste is coated on the IC pin, which is sticky. If the position deviates, reposition it.
2. After the BGA IC is positioned, it can be welded. As with the solder ball planting, adjust the hot air gun to the appropriate air volume and temperature, make the center of the air nozzle align with the central position of the IC, and heat slowly. When the IC sinks down and the solder paste overflows, it indicates that the solder ball has fused with the solder joint on the PCB. At this time, you can gently shake the hot air gun to make the heating even and full due to the effect of surface tension. The solder joint between BGA IC and PCB will be automatically aligned and positioned. Please do not press BGA forcibly during heating, or solder will overflow, which may easily lead to tripping and short circuit. Clean the plate with Tianna water after welding.
4、 Dismantling method of BGA chip with glue
At present, BGA ICs of many brands of mobile phones are filled with sealant, which makes disassembly more difficult. The unglued techniques for the disassembly of this type of IC. The following is a detailed introduction.
For the sealing glue of Motorola mobile phones, there are many brands of sol water on the market that can easily remove the glue. After many experiments, it is found that the CPU of V998 is soaked in banana water, and the effect of removing the glue is good. Generally, the sealing glue is easily removed after soaking for 3-4 hours. Note: Before soaking the V998 phone, the font library must be removed, or it will be damaged. Because 998 font library is a flexible BGA, it cannot be soaked in banana water, Tianna water or glue solution. These solvents are highly corrosive to the glue in the flexible BGA font library, which will cause the glue to expand and cause the font library to be scrapped. Of course, if you don't have glue solution, you can also disassemble it directly. Motorola's sealant is low temperature resistant and easy to soften, while the CPU is relatively high temperature resistant. As long as you pay attention to the method, it can also be successfully disassembled.
1. First, adjust the air speed and temperature of the hot air gun to the appropriate position (the general air volume is at level 3 and the heat is at level 4, which can be adjusted according to different brands of hot air guns)
2. Move the hot air 5cm above the CPU and blow it. After about half a minute, use a small blade to start from the direction where there are many CPU grounding pins. Generally, pry from the first pin, that is, above the * register. Be careful not to stop the hot air.
3. After the CPU is removed, the glue is removed, and the hot air gun is used to blow at the same time. Carefully use a knife to scrape slowly bit by bit until the bonding pad is clean.
The base glue of Nokia mobile phone was first injected by special injection molding. At present, there is no better way to drop the glue. Please pay attention to the operating skills when disassembling:
1. Fix the machine board, adjust the temperature of the hot air gun to be between 270 ℃ and 300 ℃, increase the air volume, and preheat the removed IC sealant for about 20 seconds without blowing the resistance and capacitance elements. Then move the air gun, and preheat the machine board after it cools down. It preheats the machine board for three times. Each time, add a heavier oily flux, so that the oil can flow into the welding pad for protection.
2. Adjust the temperature of the hot air gun to 350 ℃ - 400 ℃, continue to heat the IC, and gently press the IC with tweezers while heating. When you see the tin beads extruding from the sealant, you can pick several holes on the sealant with tweezers from the side with fewer components to let the tin beads flow out. Remember to keep putting oily flux at this time.
3. Remove the IC, and when no more tin beads emerge under the IC, use a fine pointed tweezers with hooks to put them under the IC at the tin emitting place, and then remove them with a gentle pick.
Clean the sealant. After most ICs are removed, the sealant will remain on the motherboard. First, put flux on the tin spot on the motherboard, and then use a soldering iron to suck the tin bead off the sealant. After several times of suction, you can clearly see the bright bonding pad at the bottom. The main function is to completely separate the solder spot from the sealant. Adjust the temperature of the air gun between 270 ℃ and 300 ℃ to heat the sealing glue of the main board. At this time, the sealing glue is basically separated from the bonding pad. Use tweezers to pick the safe place between the solder joints. The force of picking should be well controlled. If the plan is just right, one pick can remove a large piece. The removal speed of sealant on the IC is different. First clean the IC, then stick double-sided adhesive tape on the back of the IC, fix it on the desoldering table, adjust the air gun temperature to 270 ℃ - 300 ℃, put flux, heat the sealant, and remove it with tweezers.