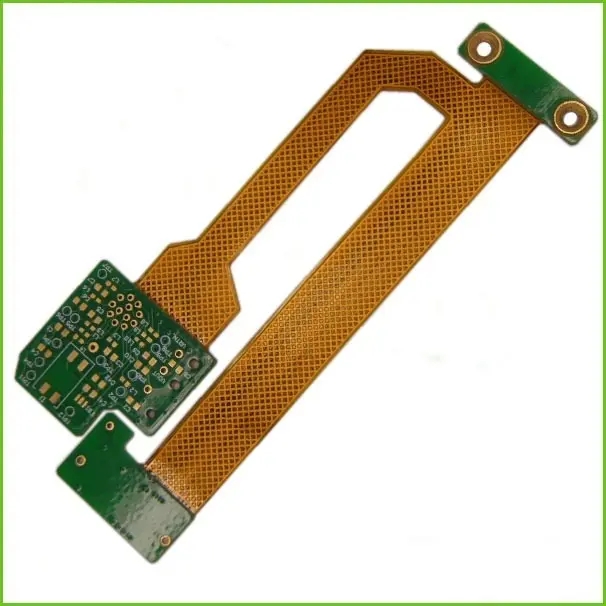
Development of FPC manufacturing technology, higher requirements of FCCL
PCB manufacturers, PCB designers and PCBA manufacturers will explain the development of FPC manufacturing technology and the higher performance requirements for FCCL
With the increasing application of FPC in new fields, its product structure, product function and product performance have also undergone great changes. The change trend is shown in the following aspects: (1) FPC has been widely used in the application of IC substrate, not only in the CSP and COF directly installed on a single chip, but also in the SIP composed of several ICs in a package as a flexible substrate; (2) FPC multilayer and rigid flex PCB have developed rapidly; (3) Micronization of FPC circuit graphics; (4) The development achievements of embedded components of flexible substrate have come out; (5) Adapt to the rapid development of halogen-free and lead-free FPC; (6) The composition of flexible substrate is developing to adapt to high signal transmission speed.
The above development trends put forward higher and newer performance requirements for FPC substrate materials. The new requirements for performance focus on the following properties: high frequency (low dielectric constant), high flexibility, high heat resistance (high TG), high dimensional stability, low moisture absorption, halogen-free, etc.
1. Adapt to high-density FPC
At present, the manufacturing method of FPC is mostly the subtraction method. The substrate material used is FCCL. With the development of high-density FPC, the conductor distance of single sided FPC is reduced from 100 um to less than 50 um. The conductor spacing of double-sided FPC is also reduced from 200 um to less than 100 um. The hole diameter of through hole (TH) has changed from 300 um to less than 100 um. The diameter of the through hole (IVH) is generally 100um. Recently, 50um IVH diameter has been designed and manufactured. The refinement of wire width and wire spacing requires that the FCCL it uses be thinner. Specifically, the thickness of the insulation layer PI film in the FCCL structure should be reduced to less than 25um. The conductor layer (mostly copper foil) of the circuit formed by it is reduced from the original 35um to 17.5um, 12um, 9um, or even 5um. FCCL uses thin copper foil, which is also beneficial to the production of fine circuits. But at the same time, due to the thin insulation layer and conductive layer (copper foil) of FCCL, it is easy to break and damage the plates in FPC production operations, resulting in the increase of unqualified products. Therefore, it is very important to solve this problem in the design of FPC production process. The process or equipment must be improved in the process of transporting FPC production.
2. High flexibility
Recently, new liquid crystal displays and high pixel digital cameras have improved the wire fineness and wire number in terms of the soft boards used. This makes FPC design more like double-sided FPC or multi-layer FPC. And the FPC used is only a few millimeters wide. Double sided FPC is generally lower in flexural flexibility than single sided FPC. When the double-sided FPC is subjected to repeated bending and flexing, greater tensile and contraction stresses will occur simultaneously on the circuit diagram. Therefore, how to use special base materials in the composition of FCCL to solve the problem of improving the flexural properties has become a new topic faced by the FCCL industry.
With the change of FPC application environment and method in recent years, improving system characteristics has become a new topic in technology development. FPC with high flexibility requirements is generally applied to the CD/DVD/HDD cartridge head of audio electronic products and computers. However, in recent years, with the wider application of vehicle navigation system, FPC has been used in vehicle applications. Compared with the family environment, the vehicle environment has more severe ambient temperature conditions. It is mainly shown that the working environment of FPC is under higher temperature. In particular, HDD components in automotive electronic products work for a long time in an ambient temperature close to 60 ℃.
With the technical development of mobile phones and small electronic products in recent years, the requirements for the high bending characteristics of FPC are becoming more and more strict. Especially the electronic components and CPUs used in electronic products, with the increase of their functions, their calorific value has also increased significantly. In this way, the average working temperature in the whole machine will rise. Therefore, the flexibility of FPC at high temperature has become an important item required by the whole machine.
For another example, in notebook computers and automotive electronic products, during the continuous use of the whole product, its working environment temperature can even reach 80 ℃. The FPC used can obtain high flexibility at room temperature, but the flexibility of FPC will deteriorate due to the softening of the adhesive and the reduction of its storage elasticity at this high temperature. During bending, stress accumulation will also occur in the copper foil. Therefore, it is a very important problem for FCCL to suppress the resulting plate warping and cracking in the substrate.
The three-layer adhesive for FCCL acts as the bonding between the film of the FCCL and the copper foil. When the ambient temperature for determining the flexural properties is above Tg of the adhesive, the storage elasticity of the adhesive resin decreases and the flexural properties of the FCCL deteriorate due to the softening of the adhesive resin. When the FCCL is flexed, the stress accumulation will also occur in the copper foil, and the plate warpage will become worse due to inhibition. When the FCCL is flexed, stress accumulation will also occur in the copper foil, which will lead to plate warping and cracking in the substrate due to inhibition. Therefore, in the development of FCCL with high heat resistance requirements, improving the Tg of adhesives has become a very important problem. Although the measured values of flexural properties of FCCL made of high Tg adhesive and ordinary adhesive are not different at room temperature, they are significantly different at high temperature and high humidity.
3. High frequency
As the electronic components installed on the FPC are constantly improving in the amount of information and transmission speed, the constituent materials of the flexible copper clad laminate should be constantly updated and improved to improve the high-speed and high-frequency characteristics of the FCCL itself.
4. High Tg
In recent years, the demand for high TgFPC substrate materials is increasingly strong. The main reasons are as follows:
(1) With the increase of the functions of electronic components and CPU used in electronic products, their calorific value has also increased significantly. This makes the average working temperature in the whole product rise. Therefore, FPC substrate materials are required to have higher heat resistance.
(2) In order to ensure its high reliability, it is more important to ensure the ion migration resistance (CFA) of FPC that can realize high-density installation and its circuit graphics. The high heat resistance of FPC substrate is conducive to the improvement of ion migration resistance.
(3) With the expansion of application fields, the demand for high Tg FPC substrate materials is more intense. For example, the COF directly installed on the surface of FPC requires the flexible substrate to have higher heat resistance, so as to obtain high reliability and high product qualification rate for direct bonding of chips on FPC.
5. Halogen free
The development of halogen-free three-layer FCCL in the world is generally slower than that of rigid FR-4 CCL. The main reason is that PFC factories generally require that the price of halogen-free FCC products should not be higher than that of traditional bromine containing FCC products. And its heat resistance and dimensional stability should not be lower than that of bromine containing FCCL products. In terms of realizing halogen-free three-layer FCCL, it is more difficult to develop halogen-free epoxy resin adhesive for FCCL because halogen-free epoxy resin adhesive generally has a negative impact on flexibility, heat resistance and various reliability.
The investigation results show that FPC manufacturers' attitudes towards the use of halogen-free FCC can be divided into four types. Among them, the manufacturers that have adopted halogen-free FPC products in the whole set of electronic and communication products, accounting for 14% of the total number of manufacturers surveyed. The majority of manufacturers of complete machine electronics and communication products have the attitude of "part of them are halogen-free", accounting for 42% of the total number of manufacturers surveyed.
This year, the manufacturing technology of high-density FPC, multi-layer FPC, soft and hard bonding boards, and multilayer FPC with the method of lamination has made greater progress. This makes the selection of FCC varieties in FPC manufacturing more inclined to adopt FCC products with high density, high flexibility, high frequency (low dielectric constant), high heat resistance (high Tg), etc. that are suitable for FPC. PCB manufacturers, PCB designers and PCBA manufacturers will explain the development of FPC manufacturing technology and the higher performance requirements for FCCL.