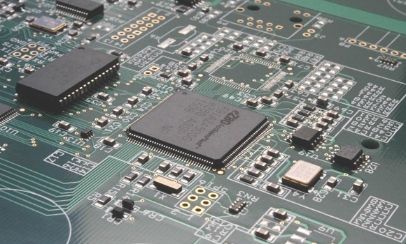
With the speed of updating electronic products, the number of printed circuit boards, which are the main components of electronic waste, is also increasing. The pollution of waste PCB to the environment has also attracted the attention of many countries. Waste PCBS contain heavy metals such as lead, mercury and hexvalent chromium, as well as toxic chemicals such as polybrominated biphenyls (PBB) and polybrominated diphenyl ethers (PBDE) as flame retardants. These substances in the natural environment will cause great pollution to groundwater and soil, and bring great harm to people's life and physical and mental health. There are nearly 20 kinds of non-ferrous metals and rare metals in the waste PCB, which has high recovery value and economic value. It is a real mine waiting to be mined.
One, physical law
The physical method is to realize the recycling by using the mechanical means and the different physical properties of PCB.
1.crushing
The purpose of crushing is to make the metal and organic matter in the waste circuit board as far as possible to dissociate, so as to improve the sorting efficiency. It is found that when the crushing is 0.6mm, the metal can basically achieve dissociation, but the choice of crushing mode and level depends on the subsequent process.
2. Sorting
Separation is achieved by using the differences in physical properties of materials such as density, particle size, electrical conductivity, magnetic conductivity and surface properties. At present, wind shaker technology, flotation separation technology, cyclone separation technology, floating-sinking separation and eddy current separation technology are widely used.
Two, supercritical technology treatment
Supercritical fluid extraction technology refers to a purification method that makes use of the influence of pressure and temperature on the dissolution capacity of supercritical fluid under the condition of no change in chemical composition. Compared with the traditional extraction method, the supercritical CO2 extraction process has the advantages of friendly environment, convenient separation, low toxicity, little or no residue, and can be operated at room temperature.
The main research directions of using supercritical fluid to treat waste PCB are mainly in two aspects: First, supercritical CO2 fluid has the ability to extract resin and brominated flame retardant components in printed circuit board. When the resin binder in PCB circuit board is removed by supercritical CO2 fluid, the copper foil layer and glass fiber layer in PCB can be easily separated, which provides the possibility for efficient recycling of PCB materials. Secondly, the metal in waste PCB is extracted by supercritical fluid directly. Cd2+, Cu2+, Zn2+, Pb2+, Pd2+, As3+, Au3+, Ga3+ and Sb3+ were extracted from simulated cellulose filter paper or sand with lithium fluoride diethyl dithiocarbamate as complexing agent, and the extraction efficiency was above 90%.
Supercritical treatment technology also has great defects, such as: high selectivity of extraction requires the addition of entrainer, resulting in harm to the environment; High extraction pressure requires high equipment; High temperature is used in the extraction process, so energy consumption is high.
Three, chemical method
Chemical treatment technology is the extraction process using different chemical stability of various components in PCB circuit boards.
1. Heat treatment method
Heat treatment is the separation of organic matter and metal by means of high temperature. It mainly includes incineration method, vacuum cracking method, microwave method and so on.
(1) Incineration method
The incineration method is to break the e-waste to a certain particle size and send it to a primary incinerator for incineration to decompose the organic components and separate the gas from the solid. The residue after incineration is the bare metal or its oxides and glass fiber, which can be recovered by physical and chemical methods respectively after being crushed. Gases containing organic components are burned in secondary incinerators and discharged. The disadvantage of this method is that it produces a lot of waste gas and toxic substances.
(2) Cracking method
Pyrolysis is also called retorting in industry. It is to place e-waste in a container under the condition of air isolation and heat it to control the temperature and pressure, so that the organic matter in it is decomposed into oil and gas, which can be collected by condensation and recycled. Different from the incineration of electronic waste, the vacuum pyrolysis process is carried out under the condition of no oxygen, so the production of dioxins and furans can be suppressed, and the waste gas production is less, causing less pollution to the environment.
(3) microwave processing technology
Microwave recycling method is to first break the electronic waste, and then microwave heating, so that the organic matter is heated and decomposed. It is heated to about 1400 ℃ to melt glass fibers and metals to form vitreous substances. After cooling, gold, silver and other metals are separated in the form of small beads. The remaining glass materials can be recycled and used as building materials. This method is significantly different from the traditional heating method, and has the advantages of high efficiency, high speed, high resource recovery and low energy consumption.
2. Hydrometallurgy
Hydrometallurgy involves removing metals from electronic waste and recovering them from the liquid phase, taking advantage of their ability to dissolve in acids such as nitric acid, sulfuric acid and aqua regia. It is a widely used method to deal with electronic waste. Compared with pyrometallurgy, hydrometallurgy has the advantages of less waste gas emission, easy treatment of metal residue after extraction, remarkable economic benefits and simple process flow.
Four, biotechnology
Biotechnology is to solve the problem of metal recovery by the adsorption of microorganisms on mineral surface and the oxidation of microorganisms. Microbial adsorption can be divided into two types: the use of microbial metabolites to fix metal ions and the use of microorganisms to fix metal ions directly. The former is fixed by hydrogen sulfide produced by bacteria. When the surface of the bacteria absorbs ions to reach saturation state, flocs can be formed and settled down. The latter is to use the oxidation of iron trivalent ions to oxidize other metals in precious metal alloy such as gold into soluble substances and enter the solution, so that precious metals exposed for easy recovery. Biotechnology extraction of gold and other precious metals has the advantages of simple process, low cost and convenient operation,but the leaching time is long and the leaching rate is low, so it has not been really put into the disposal of waste PCB circuit boards.