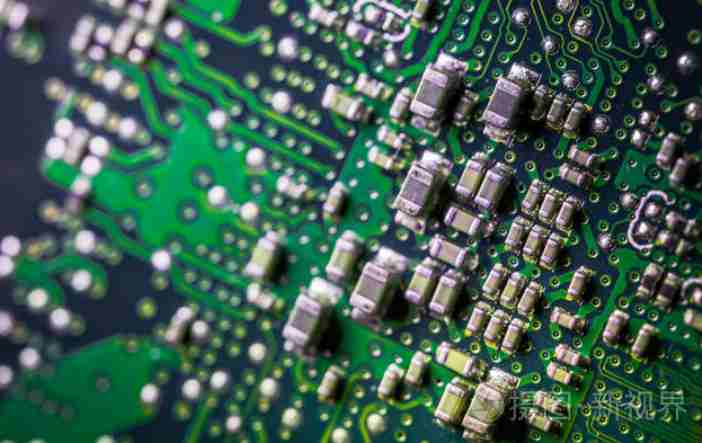
Although some information about board prototyping has been around for a while, getting a straight answer can be confusing. There's a lot of information out there, and even the most experienced engineer may have trouble telling whether information about their particular prototype PCB is right or wrong. One example is the difference between blind and buried holes in circuit boards. Here is all the information about what blind and buried hole technologies are in PCBS.
What are blind and buried holes?
We all know that the copper track on a printed circuit board is a conductive path used to connect two points in a PCB.
Blind hole channel:
Blind holes are copper-plated holes that connect to only one outer layer of the PCB. However, it is important to know that the holes do not reach all the way to the board, making it "blind" or "invisible" to the naked eye.
Channels for burying holes:
On the other hand, buried through-holes connect at least two layers without reaching the outer edge of the plate. Therefore, it is buried within the circuit and completely internal.
Additional useful information about blind and buried holes in prototype PCB manufacturing:
In general, these two types of through-holes are used for higher density boards, as simple boards do not actually require a different design structure since they consist of only one layer.
Blind hole channel:
Blind holes must be defined with a separate drill file and the ratio of hole diameter to bit diameter must be less than or equal to 1.
The smaller the hole, the smaller the distance between the outer layer and the corresponding inner layer.
Each hole has an inner layer.
Channels for burying holes:
Because these embedded through holes are used to connect different parts of the inner layer of the prototype circuit board, each hole must be made from a separate drill file.
What are the technical processes of surface mounting of electronic components?
, printing and dispensing
Printing and dispensing It is to print the patch to the welding plate of PCB, to prepare for the welding of electronic components. The equipment used for the surface mounting of electronic components is the solder paste printing machine located at the SMT front. After printing, the point needs to carry out the dispensing step, which is to drop the glue directly onto the fixed position of the PCB, and then fix the component directly on it, which can increase the service time of the component. Now on the market the use of larger components are the use of artificial dispensing.
Two, curing and reflow welding
Curing is the most critical step in the surface mounting of electronic components, its role is to make components accurately fixed on the PCB board, so that the assembly components and PCB board can be more perfect together. The reflow welding technology is a technical step in the surface mounting of electronic components. Generally, those who can carry out this step are more experienced technicians in the industry.
Three, cleaning and testing
Cleaning and detection can be said to be the last two steps in the process of surface mounting of electronic components. We all know that cleaning is to clean the residual useless things on PCB, and the cleaning process also needs to be careful, such as to check which positions have not been fixed, which is also a disguised inspection method.
First, the principle of AOI detection
Principle: Using the optical principle, the camera on the equipment will scan PCB, collect images, and compare the collected solder joint data with the qualified data of the machine database. After image processing, PCB welding status will be marked.
Two, the advantages of AOI detection
Because some electronic products are becoming smaller and smaller, PCB circuit boards are becoming more and more precise, the difficulty of manual inspection of PCB board is increasing, the speed of inspection is slower than that of the machine, and the long time inspection is easy to produce eye fatigue, resulting in missed detection. In order to improve work efficiency, AOI can reflect its superiority.
The advantages of AOI are as follows:
1. Save manpower and reduce labor costs;
2. Increase production efficiency and improve production capacity;
3. Unified detection standards, no differences due to different lines;
4. Timely feedback and statistics of production problems;
5. Collected test data, provided process analysis, and strengthened process capability;
6. Increase the rate of good products in storage.
Iii. AOI test the position of SMT patch processing line in small target
1. After the use of the patch machine: it can effectively prevent the missing of components, polarity, displacement, stela, reverse and so on.
2. Use after reflow welding: Located at the end of the production line, the detection system can check for missing, offset and skew of components, solder spot correctness and solder paste deficiencies, welding short circuit as well as toe warping and all polarity defects.