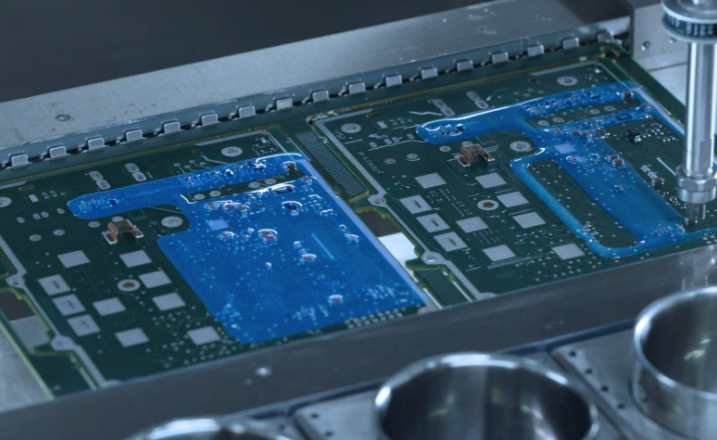
With increasing miniaturization comes tremendous advances in component and wiring technologies, such as highly integrated microics in BGA enclosures and the reduction of insulation spacing between conductors to 0.5mm, just to name a few. The wiring design of electronic components has more and more influence on whether the test can be carried out well in the manufacture process of PCBA. Here are some important rules and practical tips.
By following certain procedures (DFT-Design for Testability, testable design), production test preparation and implementation costs can be greatly reduced. These procedures have evolved over the years and, of course, have to be expanded and adapted to new manufacturing and component technologies.
As the structural size of electronic products gets smaller and smaller, two issues of particular interest are emerging:
First, there are fewer and fewer accessible circuit nodes;
Second, the application of methods such as In-Circuit-Test is limited.
To solve these problems, measures can be taken in circuit layout, new testing methods can be adopted, and innovative adapter solutions can be adopted. The solution of the second problem also involves making the test system used as a separate process take on additional tasks. These tasks include programming memory components through a Test system or performing integrated component self-tests (BIST, Built-in self-tests). Transferring these steps into a test system creates more added value overall. In order to successfully implement these measures, corresponding considerations must be taken during the product research and development stage.
1. What is testability
The meaning of testability can be understood as: the test engineer can test the characteristics of a component in the simplest possible way to see whether it can meet the expected function. To put it simply:
How simple is the method of testing whether a product conforms to a technical specification?
How fast can you program tests?
How thorough is the discovery of product faults?
How simple is the approach to accessing test points?
Mechanical and electrical design procedures must be considered in order to achieve good testing. Of course, there is a cost to achieving optimum testability, but it has a range of benefits to the overall process and is therefore an important prerequisite for the successful production of the product.
2. Why develop test-friendly technologies
In the past, if a product could not be tested at the previous test point, the problem was simply pushed to a new test point. If a product defect is not found during production testing, the identification and diagnosis of the defect is simply pushed to functional and system testing.
On the contrary, today people try to find defects as early as possible, which has the advantage not only of low cost, but also because today's products are so complex that some manufacturing defects may not be detected at all in functional testing. For example, some components to pre-load software or programming, there is such a problem. (e.g. Flash memory or ISPs: In-System Programmable Devices). The programming of these components must be planned at the development stage, and the test system must master this programming.
It costs some money to test a friendly PCB design, however, it costs more to test a difficult PCB design. Testing itself has a cost, and the cost of testing increases with the increase of the number of tests; From online testing to functional testing and system testing, the cost of testing is increasing. Skipping one of these tests can be even more costly. The general rule is that the cost of each additional level of testing increases by a factor of 10. By testing friendly PCB designs, faults can be detected early, and the cost of testing friendly PCB designs can be quickly compensated.
3. How does documentation affect testability
Only by making full use of the complete data in component development, it is possible to compile a test program that can fully detect faults. In many cases, close collaboration between the development and test departments is necessary. Documentation has an indisputable impact on the test engineer's understanding of component functions and formulation of test strategies.
To get around the problems caused by lack of documentation and poor understanding of component function, test system manufacturers can rely on software tools that automatically generate test patterns according to random principles, or on non-vector methods, which are only a stopgap solution.
Complete pre-test documentation includes parts lists, PCB design data (mainly CAD data) and detailed information about the functions of the service components (such as data sheets). Only when you have all the information is it possible to write test vectors, define component failure styles, or make certain pre-adjustments.
Certain mechanical data is also important, such as those needed to check that components are soldered and positioned properly. Finally, for programmable components, such as flash memory, PLD, FPGA, etc., if not in the final installation of programming, is in the test system should be programmed, also must know the respective programming data. The programming data of the flash element should be intact. If the flash chip contains 16Mbit data, 16Mbit data should be used to prevent misunderstandings and address conflicts. For example, this can happen if you use a 4Mbit memory to provide only 300Kbit of data to a component. Of course, the data should be prepared in a popular standard format, such as Intel's Hex or Motorola's S recording structure. Most test systems, provided they can program flash or ISP components, can interpret these formats. Much of the information mentioned above is also necessary for component manufacturing. Of course, a clear distinction should be made between manufacturability and testability, as these are completely different concepts and thus constitute different premise