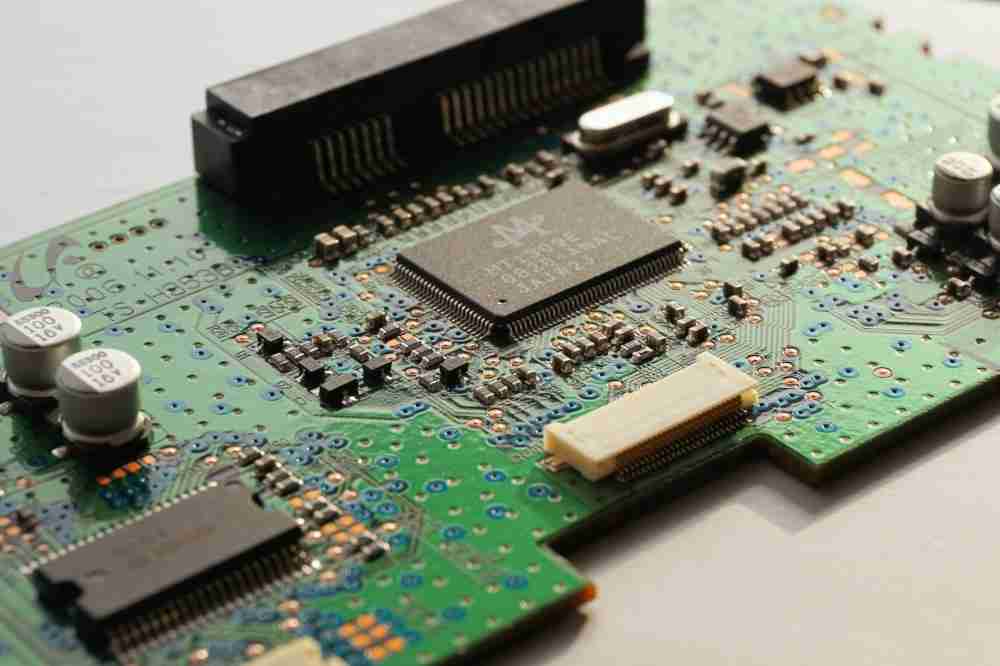
1. Press one time after drilling == "outside again press copper foil ==" and then laser -------- "first order
2. Press one time after drilling == "outside again pressed copper foil ==" then laser, drilling == "outer layer again pressed copper foil ==" then laser ------- "second order.
The first is to see how many times you are laser, is a few steps. The following is a brief introduction of the PCB circuit board HDI process.
Electronic products toward light, thin, short, miniaturized open, the corresponding printed circuit board is also facing high precision, fine line, high density. The trend of printed boards in global shopping malls is to introduce blind buried hole circuit boards in high-density interconnected products, and then more useful space saving, so that the line width, line spacing is thinner and narrower.
one HDI board definition
HDI: Short for high Density interconnection, high density interconnection circuit board, non-mechanical drilling, micro blind hole ring below 6mil, wiring width/gap between the internal and external layers below 4mil, welding disc diameter is not greater than 0.35mm increased layer method of multilayer plate manufacturing formula called HDI circuit board.
Short for Blind via, a buried hole that completes the connection between the inner and outer layers: Buried via is short for Buried via. Blind access holes are mostly 0.05mm~0.15mm in diameter to complete the connection between the inner and inner layers. Laser hole formation is generally used for blind hole formation, including laser hole formation, plasma etching hole and photoinduced hole formation, which can be divided into CO2 and YAG ultraviolet laser machine (UV).
two 1.HDI circuit board material includes RCC,LDPE,FR41)RCC:Resin coated copper. RCC is made up of copper foil and resin with roughened, heat-resistant and oxidation-resistant exterior. Its structure is shown as follows: (Thickness > 4mil) RCC resin layer, has the same process as FR-4 adhesive sheet (Prepreg). In addition, it should also be satisfied with the functional requirements of the multilayer layer method:
(1) High insulation reliability and microthrough-hole reliability;
(2) high glass transition temperature (Tg);
(3) Low dielectric constant and low water absorption;
(4) Higher viscosity and strength of copper foil;
(5) The insulating layer thickness is uniform after curing, because RCC is a new product without glass fiber, which is conducive to laser and plasma etching treatment, and is conducive to the lightweight and thinning of multi-layer circuit board. In addition, resin coated copper foil with 12pm, 18pm and other thin copper foil, simple processing.
FR4 sheet: Thickness < =4mil. 1080 is generally used when using PP, and try not to use PP2 of 2116. Copper foil requirements: When the customer has no requirements, the copper foil on the substrate is preferred to use 1 OZ in the inner layer of the transmission PCB, HDI board is preferred to use HOZ, internal and external electroplated copper foil is preferred to use 1/3 OZ.
Three. Laser hole:
The principle of CO2 and YAG UV laser pore-forming laser pore-forming: laser light is a powerful beam of light stirred up by the increase of energy when the "ray" is influenced by the outside world, in which the infrared light or visible light has thermal energy, and the ultraviolet light has chemical energy.
The ejection onto the exterior of the object will entail reflection-absorption and Transmission, and the effects of which will occur only to the object being absorbed. And its effect on the plate can be divided into two different reactions: photothermal ablation and photochemical cracking. 1.YAG's UV laser pore-forming: it can set a fine light beam, and the copper foil absorption rate is relatively high, it can remove the copper foil and burn the micro blind hole below 4mil. Compared with CO2 laser pore-forming, there will be no resin residue in the bottom of the hole, but it will simply damage the copper foil at the bottom of the hole, the energy of a single pulse is little, and the processing power is low. (YAG, UV: wavelength: 355, wavelength is appropriate short, can process very small holes, can be resin and copper together) do not need special window technology 2.CO2 laser hole: choose infrared CO2 laser machine, CO2 can not be absorbed by copper, but can absorb resin and glass fiber, generally 4~6mil micro blind hole.
The hole formation method is as follows:
A. The Conformal Mask of copper window opening is to press RCC on the inner Core board of the printed circuit board, then open the copper window, and laser light is used to remove the substrate inside the window to complete the micro blind holes. Details are to make the inner center plate of FR-4 first, so that both sides have blackened lines and Target Pad, and then press together, and then according to the corrosion of copper window film to remove the orientation of the blind hole corresponding copper skin and then CO2 laser light burned the resin in the window, can be hollowed out to the bottom pad and micro blind holes.
The so-called "Large Conformal mask" is to expand the copper window to about 1mil larger than the blind hole side. When the aperture of a prajna is 6mil, its large window can be opened to 8mil.
Four. 1+2+1 is used as an example to illustrate the process of laser drilling blind burials
Manufacturing process: Cutting, Large copper Windows open, L2 ~ L3 buried holes -- -- -- -- -- in addition to the glue residue -- -- -- -- -- -- -- -- -- - plating buried hole - resin plug hole -- -- -- -- -- the inner graphics - pressing -- -- -- -- -- - L1-2 & Large L4-3 layer Windows (Copper window 1mil larger than blind hole aperture each side) (etching) ----- -- L1-2&L4-3 layers Laser drilling blind holes -- -- -- -- -- -- -- in addition to the glue residue twice -- -- -- -- -- -- -- electroplating blind hole (pulse electroplating) -- -- -- -- -- - resin plug hole -- -- -- -- -- -- -- grinding plate + reduce copper -- -- -- -- -- - mechanical drill hole is -- -- -- -- -- normal 2 + 4 + 2 processes and cutting L3 ~ 6 layer graphics - pressing - large copper Windows open →L23&L76 Laser buried hole →L26 mechanical drilling → rubber slag removal → electroplating buried hole → resin plug hole -----L2.