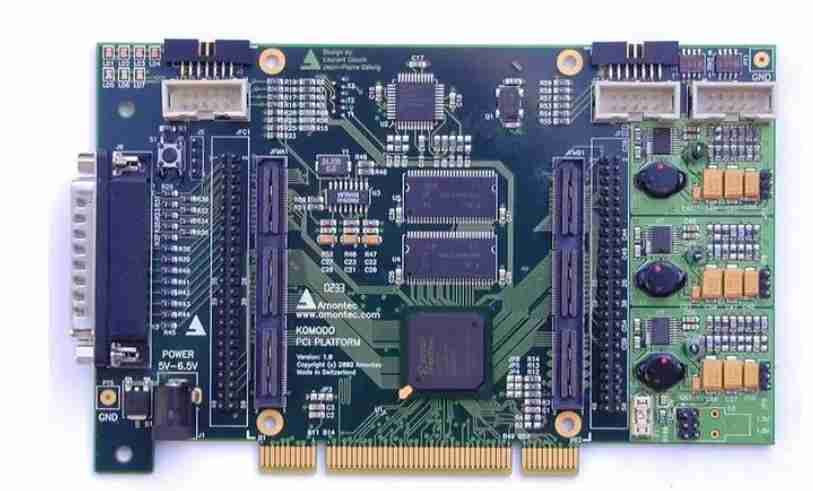
PCBA welding processing mainly refers to the production process of soldering PCB circuit board and components. In the process of welding, it is easy to have poor welding, such as false welding and false welding, which will seriously affect the reliability of products and greatly improve the maintenance cost of products. The following is the knowledge about how to deal with anomalies in patch processing and how to prevent PCBA virtual welding defects.
1. How to prevent PCBA virtual welding defects
The problems of false welding and false welding defects in the welding process of PCBA are caused by many reasons. The main reason is that the solder cannot fully infiltrate the pad and the pin of the component, and the pad of the component and the circuit board cannot be fully welded. In the production process, it can be prevented in the following ways.
1. Moisture-proof storage of components If components are placed in the air for a long time, they will absorb moisture and oxidize, leading to insufficient removal of oxides in the welding process, resulting in virtual welding and fake welding defects. Therefore, in the welding process, to have moisture components for baking, for oxidation components to replace. Generally, the PCBA processing plant will be equipped with an oven to bake the components with water vapor.
2, the selection of well-known brand solder paste PCBA in the welding process of virtual welding and false welding defects, and the quality of solder paste has a great relationship. The composite metal composition of solder paste and the unreasonable configuration of flux are easy to lead to the weak activation ability of flux in the welding process, and the solder paste can not fully infiltrate the pad, resulting in virtual welding and false welding defects. Therefore, you can choose famous brands like Qianzhu, Alpha, Weituo and so on.
3. The problem of virtual welding and false welding to adjust printing parameters is largely due to the lack of tin. In the printing process, the pressure of scraper should be adjusted, the appropriate steel mesh should be selected, and the steel network port should not be too small to avoid the situation of too little tin.
4, adjust the reflow welding temperature curve in reflow welding process, to control the welding time, not enough time in the preheating zone, can not make the flux fully activated, remove the surface oxide of the welding, too long or too short time in the welding zone, will cause virtual welding and false welding.
5. Try to use reflow welding and reduce manual welding. Generally, when using electric soldering iron for manual welding, the technical requirements for welding personnel are relatively high.
6, avoid the temperature of the electric iron is too high or low in the post-welding processing and maintenance of PCBA welding, it is necessary to use the electric iron for manual welding. In the use of electric iron, non-standard operation, resulting in the temperature of the iron head is too high or too low, it is easy to cause virtual welding and false welding.
Therefore, in welding, to keep the iron head clean, according to the size of different parts and solder joints, device shape to choose different power types of electric iron, the welding temperature is controlled between 300℃ - 360℃. Virtual welding and false welding caused in the process of PCBA welding are caused by many factors, and the above is just to list some common reasons. Through the above preventive measures, combined with the actual situation, it can effectively reduce the welding defects of virtual welding and false welding.
2. How to deal with the anomalies during patch processing
In case of abnormal production in the SMT factory or more than 3PCS of defective products with the same bit number and the same problem are found consecutively, the operator shall immediately report to the technician, who shall analyze and solve the problem in time, and analyze whether it is due to the machine...... In case of abnormal production in the SMT factory or more than 3PCS with the same bit number and the same problem are found consecutively, the operator shall immediately report to the technician, who shall analyze and solve the problem in time. And analyze the reason is due to machine failure, materials, technology, design, human factors, environmental factors caused by the product or process and standards or regulations do not conform to the reasons caused by the combination of solutions, and with the implementation and tracking.
If the technician cannot solve the problem, he/she shall inform the engineer to solve the problem in time. If the engineer cannot repair the problem, he/she shall report to the production manager. After the production manager confirms the problem, the engineer shall inform the maintenance engineer of the manufacturer to repair the smt factory and record the abnormal maintenance result on the "Equipment Resume". If the material is abnormally long, the abnormal form shall be filled in time, indicating the abnormal reasons and defective ratio, and inform the production supervisor for confirmation and review. After the confirmation of the production supervisor, it shall be timely submitted to the production manager for confirmation and finally to the quality department for confirmation and analysis.
If it is necessary to return the materials after the reply of abnormal list, inform the material clerk to return the abnormal materials in time. For the abnormal feedback in the later section (welding, testing, maintenance, quality), the bad outflow of the shift in charge shall be filled in the cause of the abnormal occurrence by the longer shift, and the technician shall write the outflow cause analysis and improvement countermeasures, and then submit the filling to the workshop supervisor for confirmation. Elongate, technicians shall strictly implement in accordance with the improvement countermeasures, and the workshop supervisor shall be responsible for tracking and confirming the improvement of subsequent production
3. Teach you how to choose raw materials
Shenzhen SMT processing experts say that the metal base patch because of its performance and characteristics and the performance requirements of electronic products are close, so it has become the best choice for many patch processing enterprises. Metal plate can realize large area patch processing, and has the following performance characteristics:
(1) Metal-based patches with good mechanical properties have high mechanical strength and toughness, which is better than rigid material patches. They can be used for large-area patch processing and can undertake the installation of overweight components. In addition, metal-based patches also have high dimensional stability and smoothness.
(2) Good heat dissipation performance because the metal patch is directly in contact with the semi-cured sheet, it has excellent heat dissipation performance. The metal patch is used for patch processing. During processing, the metal patch can play the role of heat dissipation. The heat dissipation capacity depends on the material and thickness of the metal patch and the thickness of the resin layer. Of course, while taking into account the heat dissipation performance, electrical performance, such as electrical strength, should also be taken into account.
(3) can shield the electromagnetic ferry in the , to prevent the radiation of the electromagnetic ferry has been the concern of designers, the use of high-frequency electronic circuit metal patch can act as a shielding plate, play the role of shielding the electromagnetic ferry.