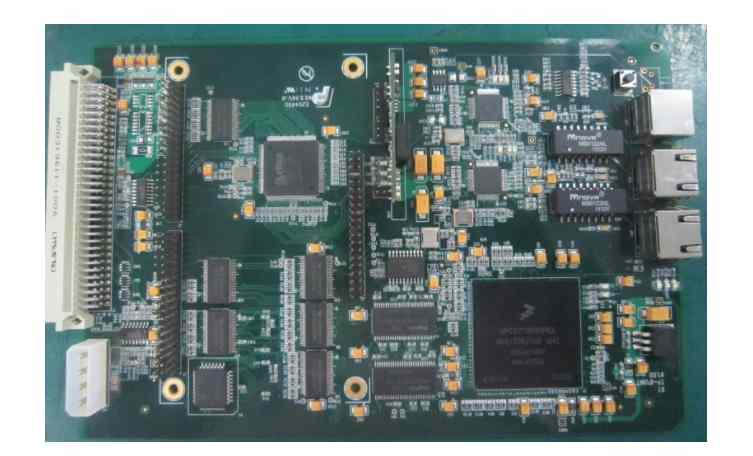
Whether the assembly mode and the design of the process flow are reasonable or not directly affects the assembly quality, production efficiency and manufacturing cost. The SMT lead-free process should also be designed and tested in accordance with the principles of simple selection, good quality, short process route, fewer types of process materials and low cost of SMT patch processing. The following patch processing manufacturers explain how to implement lead-free process and how to eliminate static electricity patch processing related knowledge.
1. How to eliminate static electricity in patch processing
Electronic components according to their types, the degree of electrostatic damage is not the same. Low 100V static voltage will also cause damage to it. In recent years, as the development of electronic components tends to be integrated, the corresponding electrostatic voltage is also decreasing. Especially in the patch processing plant, due to the many working procedures, large personnel flow, operation control difficulty, different from electronic component manufacturers, electrostatic bags, electrostatic carts and ground wires, the anti-static components are relatively simple, easy to control. We all know that the electrostatic voltage induced by the human body is above 2 ~ 4kV, usually due to the slight movement of the human body or the surface of the insulation. In other words, if the electrostatic potential brought by daily life comes into contact with IC, then almost all 1C will be destroyed. Especially in smt plant this risk exists in any SMT processing environment where no electrostatic protection measures have been taken. Electrostatic damage to IC is not only reflected in the manufacturing process of electronic components, but also in the process of IC assembly, transportation and other damage to IC. To solve the above problems, smt processing plants can adopt the following methods to eliminate static electricity:
First, grounding.
Grounding is the direct discharge of static electricity to the ground through a wire, which is an anti-static measure. Direct, effective, effective, the conductor is usually grounded, such as artificial anti-static hand stripping and workbench grounding. Grounding the human body through the wrist strap (1) Grounding the human body through the ESD shoes (or shoelaces) and the ESD floor (3) Grounding the workbench (4) Grounding the test instruments, tool clips, and soldering iron (5) Grounding the ESD floor and mat. ⑥ Anti-static transfer car, box and frame as far as possible grounding. ⑦ Anti-static electric chair grounding.
Two, electrostatic shielding.
Electrostatic sensitive components may be exposed to electrostatic areas during storage or transportation. The electrostatic screen can reduce the noise of external static electricity on electronic components. The usual method is to use electrostatic shielding bags and anti-static turnover box as protection. In addition, anti-static electricity is often easy to produce static electricity on human body clothes have a certain shielding effect.
Three, ion neutralization.
Insulator is often easy to produce static electricity, static electricity to the image. It is not effective to use the grounding method, the method usually used is ion neutralization (Lang separation fruit with shielding), that is, in the working environment with ion fan, etc., to provide the first class potential of the working area. Therefore, in the anti-static materials and anti-static facilities, are derived from this way, can be divided into anti-static meters, grounding system anti-static products, shielding anti-static packaging, transportation and storage of anti-static materials, neutralizing electrostatic elimination equipment, and other anti-static supplies.
In fact, many small domestic companies may lack the detailed control of electrostatic protection. Moreover, domestic SMT processing plants have been engaged in low-end consumer electronics products for a long period of time, and there are no high requirements on the quality of many products, nor a lot of capital investment. However, with the upgrading of the industry and the improvement of the country's overall manufacturing capacity in recent years, In line with the needs of the large market, the detailed control of production and processing has gradually been put on the agenda, and electrostatic control has been gradually paid attention to by more people.
2. How to implement lead-free process in patch processing
1. According to domestic and foreign experience, the following points must be made in the correct implementation of lead-free technology in SMT patch processing:
1. Strengthen the management of upstream suppliers to ensure that the raw materials and components they provide are in line with lead-free standards.
2. The patch factory shall establish a production line that meets the requirements of environmental protection.
3. Strengthen the material management of lead-free production.
4. Conduct training for all staff.
5, the correct implementation of lead-free technology. From the beginning of product design to test loyalty to meet the requirements of ROHS. Process aspects include: selection of suitable lead-free assembly mode and process flow; Selection of components, PCB and lead-free welding materials: All processes in PCB design, printing, patch, reflow welding, wave soldering, manual welding, repair, cleaning and testing of lead-free products should be controlled in accordance with the requirements of the lead-free process.
6. Conducted quality assessment of lead-free products to ensure that they meet ROHS and product reliability requirements.
2. Determine the assembly method and SMT patch
Whether the assembly mode and the design of the process flow are reasonable or not directly affects the assembly quality, production efficiency and manufacturing cost. The SMT lead-free process should also be designed and tested in accordance with the principles of simple selection, good quality, short process route, fewer types of process materials and low cost of SMT patch processing. Priority should be given to reflow welding in the design of lead-free process flow: it is recommended that no or less wave crest welding and manual welding processes should be adopted as far as possible. When there are only a few through-hole components (THCS) and THCS at high temperature can be purchased, reflow welding of through-hole components can be selected to replace wave crest welding, selective wave crest welding, automatic welding robot, manual welding and crimping, etc. When wave soldering process must be used, selective wave welding process can be recommended: some single panel and through-hole components are very much the case, SMT plant still needs to use the traditional wave welding process.