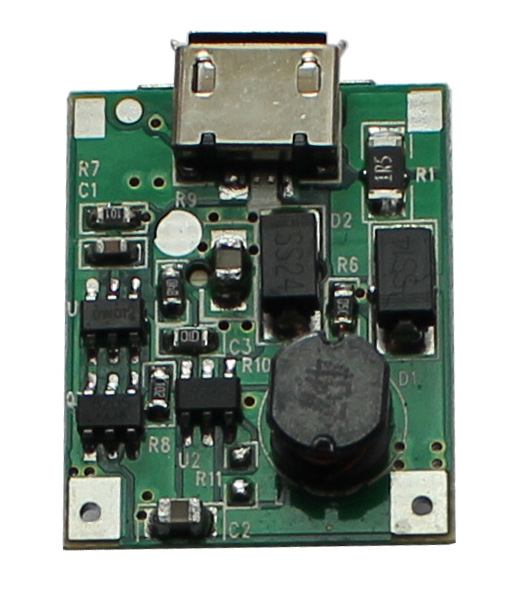
1. Laser fine perforated PCB board
With the continuous transformation and upgrading of Chinese manufacturing industry from manufacturing to intelligent manufacturing, high value-added, high technical barriers and higher end fine processing has become an important development direction. With the increasing demand for high precision machining, the related fine machining technology also develops rapidly. Among them, laser fine machining technology has gained more and more recognition and attention in the market.
As one of the important branches of laser fine processing, laser fine drilling is widely used in the PCB industry. Compared with the traditional PCB drilling process, laser processing speed is not only fast in the PCB industry, but also can realize the traditional equipment can not realize the small hole, microhole and invisible hole drilling, which more meets the needs of the PCB market!
PCB, called printed circuit board, is an important device in the electronics industry. As an important carrier of connecting components, it supports the development of the electronics industry. Most electronic products are inseparable from the application of PCB circuit boards. Therefore, laser fine punching in PCB industry has become the mainstream application of market processing. Through CO2 laser or ultraviolet laser drilling PCB circuit board, you can drill blind holes, through holes at high speed, this way of processing efficiency, good effect.
The development of PCB industry has gradually driven the development of laser fine technology, to the laser processing industry, especially the laser drilling industry has brought more development opportunities!
2. The main application of laser fine punching in PCB circuit board
In recent decades, with the continuous development of the manufacturing industry, the miniaturization and high speed of electronic products have put forward higher and higher requirements for the circuit board, and the key to improve the miniaturization of the circuit board is the increasingly narrow line width and the divergence level between the smaller and smaller micro hole. Printed circuit board slowly from a single layer to double panel, multi-panel, multi-layer and flexible board, also constantly reduce the size, improve performance, thinking of high density, high precision, microporous, small spacing and high reliability direction development, among which a variety of role of the hole size is also inclined to small aperture development.
At present, the PCB industry is gradually developing towards the direction of thin, high integration and high precision. The traditional process has different problems such as burr, dust, stress, vibration and unable to process curves. In the field of PCB, the advantages of laser technology are gradually highlighted. Its advantage is that non-contact processing without stress, will not make the plate deformation; No dust is produced; Can be processed with components PCB board; Can be any graphics processing.
In the process of PCB production and manufacturing, drilling is one of the very important process, and PCB board for the hole requirements are also very high, with the development of science and technology, laser technology application continues to develop, laser drilling has been an essential part of the current PCB production process.
Characteristics of laser drilling:
The fabrication of microholes on the circuit board and the molding of the circuit board as the hot spot of laser processing not only in China, but also in foreign countries have produced a sensation, laser processing with its superiority has brought huge benefits. Laser drilling technology also because laser has high coherence, high directivity, high brightness, high monochromator and other characteristics, showing in addition to mechanical drilling incomparable advantages. The laser beam has a high energy density, is fast to operate, and does not have much impact on areas that are not exposed to radiation. The thermal influence area is small, so that the workpiece generated by heat deformation is minimal; Laser beam as a very convenient and flexible processing method, can be used to transform, guide, focusing direction, can be used with numerical control system, processing a variety of workpiece, improve the processing quality and production efficiency.
In the drilling process of PCB board manufacturing process, two laser technologies can be used for PCB laser fine drilling:
1. The wavelength of CO2 laser is in the far infrared band
2, ultraviolet laser wavelength in the ultraviolet band.
CO2 laser machining is a kind of laser machining method which is widely used in PCB drilling. Its operating principle is: CO2 gas in the power increase and ensure the discharge time unchanged, can generate practical pulsed infrared laser, it has penetration, can penetrate the vast majority of organic materials. The application of CO2 laser in the fabrication of industrial microholes for printed circuit boards requires microhole diameters larger than 100μm(Raman,2001). For the fabrication of these large aperture holes, the CO2 laser is very productive, due to the very short punching time required for the production of large holes. Uv laser skills are widely used in the fabrication of microholes with diameters less than 100μm. With the use of microcircuit diagrams, the aperture can even be less than 50μm.
Ultraviolet laser technology is typically processed by lasers. Through the use of a process sometimes called "cold ablation," the ultraviolet laser beam creates a reduced heat-affected zone that minimizes the effects of edge machining, carbonization, and other thermal stresses.
Applications using the small beam size and low stress properties of UV lasers are drilling, including through holes, microholes, and blind buried holes. Ultraviolet laser systems drill holes by focusing vertical beams and cutting straight through the substrate. Depending on the material used, holes as small as 10μm can be drilled.
Ultraviolet lasers are especially useful for drilling multiple layers of PCB's, which are hot-die-cast together using composite materials. These so-called "semi-cures" can separate, especially after being processed with a higher temperature laser.
The UV laser skill is very productive when making holes less than 80μm in diameter. Therefore, in order to meet the needs of increasing micropore productivity, many PCB manufacturers have begun to introduce the dual-head laser drilling system. The following are equal to the three primary types of dual-head laser drilling systems in the market today:
(1) double-ended ultraviolet drilling system;
(2) double-ended CO2 laser drilling system;
(3) Stick laser drilling system (CO2 and UV).
Such drilling systems in all HDI PCB fabrication processes have their own advantages and disadvantages. Laser drilling systems can simply be divided into two types, two bit single wavelength system and two bit dual wavelength system. Whatever the type, there are two primary talents that affect drilling:
(1) laser energy/pulse energy;
(2) Beam positioning system.
The energy of the laser pulse and the transmitted power of the beam determine the drilling time. The drilling time refers to the time when the laser drilling machine drills a micro-through hole. The beam positioning system determines the moving speed between the two holes. Together, these factors determine the velocity of the microhole required by the laser drilling mechanism. The dual-head UV laser system is most suitable for drilling holes smaller than 90μm in integrated circuits and has a high aspect ratio. The double-ended CO2 laser system uses Q-switched RF encouraging CO2 lasers. The primary advantages of this system are high repeatability (up to 100kHz), short drilling time, wide control surface, and the ability to drill a blind hole with only a few shots. However, the drilling quality will be lower.