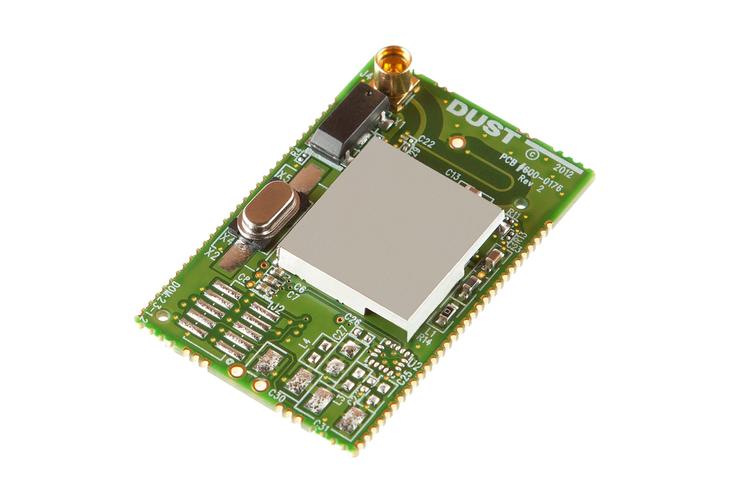
One, the purpose of the process
"Packaging" is a very important STEP in PCB circuit board factories. Japan has done the best. Carefully check the Japanese household electronics, daily products, even food, etc., the same function will make people prefer to spend more money to buy Japanese products, which is to master the mentality of consumers. Therefore, packaging should be discussed separately to let PCB manufacturers know that a small improvement may have a great effect. Another example is Flexible PCB, which is usually a small piece and numerous. In the packaging form of Japanese enterprises, it is possible to make packaging vessels especially by opening mold for the style of certain products, which is convenient to use and can be taken care of as much as possible.
Tow, early packaging research discussion
For earlier forms of packaging, see Table obsolete shipment forms for details of their deficiencies. So far there are still a few small factories in accordance with these methods of packaging.
The domestic PCB circuit board production capacity is expanding rapidly, and most of them are exported. Because of this, the competition is very tight, not only the competition between domestic factories, but also the competition with the top two American and Japanese circuit board factories. In addition to the technical level and quality of the product itself are affirmed by customers, the quality of packaging must be satisfied with customers. Almost some scale of the electronics factory, now will require PCB manufacturers to ship packaging, be sure to pay attention to the items listed below, a little even directly to the specification of shipping packaging.
1. Be sure to vacuum pack
2. The number of plates in each stack is defined according to the size too small
3. Each stack of PE film cover the tightness of the specification and leave the width of the side
4. Specifications of PE film and Air Bubble Sheet
5. Carton weight specifications and others
6. Is there any special provisions for slowing and conflicting objects before placing spanners inside the carton
7. Specifications of resistance after sealing
8. Weight frame for each case
So far the domestic Vacuum Skin Packaging is very similar, the main difference is only the size of the office surface or object surface and the degree of semi-automation.
The vacuum is packed tightly
(1) Preparation: Position PE film, manually operate the mechanical action is normal, set PE film heating temperature, vacuum time, etc.
(2) Stack plate: when the number of laminated plates is fixed, its height is also fixed. At this time, it is necessary to consider how to stack the problem, which can make the maximum output and the most save materials. The following are several principles:
1. The spacing of each spanner depends on the size (thickness) and (standard is 0.2m/m) of the PE film, and the principle that it becomes soft and elongated by heating is used. At the same time of vacuuming, the spanner is covered and the bubble cloth is pasted. Its spacing is usually at least twice as thick as the total plate of each stack. Too large will consume materials; If it is too small, it is difficult to cut and very easy to peel off the adhesive or there is no way to paste.
2. The distance between the outermost plate and the edge shall be at least twice the thickness of the plate.
3. If the PANEL size is half large, according to the above packaging form, it will cost materials and human labor. If the number is large, it can also be roughly similar to the packaging form of soft plate open mold to make utensils, and then do PE film shrink packaging. Another form, subject to the consent of the customer, no holes in each spanner, but separated by cardboard, take a proper number of overlapping. There are also cardboard or varnished paper below.
(3) Start work: A. According to the start work, the heated PE film, by the pressure frame and cover the table B. Then by the bottom vacuum pump suction and close to the circuit board, and bubble cloth adhesive. C. After the heater is removed to cool it, the outer frame is raised. D. After cutting PE film, pull open the chassis to separate each stack of cutting
(4) Packing: the packing form, if specified by the customer, must be in accordance with the customer's packing specification; If the customer does not specify, also must try to take care of the wrench transportation process not for the external force of the principle of the conclusion of the factory's packing specifications, pay attention to the items, have mentioned in front of the export of products, especially the packing must be particularly respected.
(5) Other items to pay attention to:
1. Information must be written on the outside of the box, such as "mouth and wheat tip", material number (P/N), format, cycle, number, sealing and so on. And "Made in Taiwan" (if exported).
2. Attach relevant quality certificates, such as slices, weldability report statements, test records, and various pcb test report statements required by customers, and place them in the form specified by customers. Packaging is not the door to ask, do it, when can save a lot of trouble that should not happen.