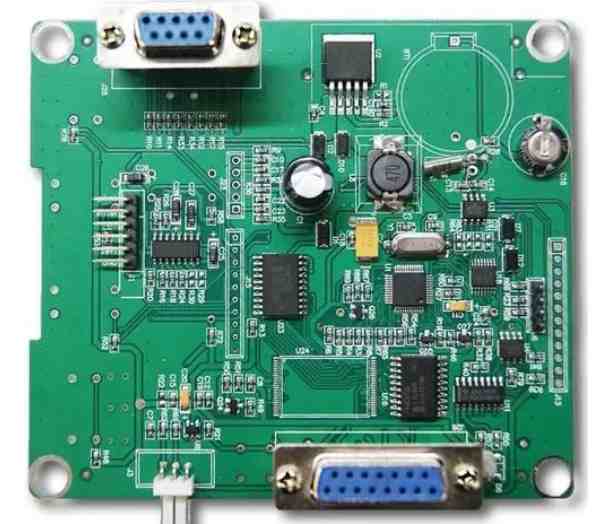
According to statistics, about 60-70% of welding defects in the process of SMT patch processing of electronic products are caused by poor solder paste printing. Therefore, the printing quality of solder paste determines the yield of SMT patch processing. The key to zero defect manufacturing is to ensure the printing quality of solder paste and prevent welding defects caused by poor printing of solder paste.
Solder paste collapse
The main adverse phenomena in the solder paste printing process of SMT patch processing are as follows:
After printing, the solder paste is not enough to maintain a stable shape, and the edge collapses and gradually spreads to the outside of the pad, forming a connection between adjacent pads. If this phenomenon can not be corrected in time, after reflux, welding short circuit is bound to occur.
Cause analysis
1. The pressure of the scraper is too large, and the solder paste is excessively squeezed, which may flow into the gap between the steel mesh and PCB. When the situation is serious, the solder paste of the adjacent pad may therefore be connected to form poor collapse.
2, the solder paste viscosity is too low, the viscosity is the key parameter of the solder paste to maintain the shape, if the viscosity is too low, after printing, the solder paste edge loose and collapse phenomenon, for fine spacing components will form the solder paste short circuit problem.
3. The metal content is too high. If the solder paste is placed on the steel net for too long or recycled solder paste is used, the diluent component in the solder paste is volatile, and the metal content is unchanged, the viscosity may decrease and the collapse phenomenon may occur.
4, solder particle size is small, particle size of the solder paste, steel mesh tin is better, after printing the solder paste shape is not so good, and printing because of the metal particles more easily spread in the steel mesh and the formation of solder paste short circuit phenomenon.
5, the moisture absorption of the solder paste, if the air humidity is large or the solder paste in the air exposure time is too long, it may lead to the solder paste to absorb the water vapor in the air and dilute, reduce the viscosity, the solder paste can not maintain the shape and collapse
6. The ambient temperature is too high, the flux viscosity in the solder paste will decrease, and the collapse phenomenon will occur after printing. Moreover, if the time is too long, the diluent components in the solder paste will further volatilized, but the viscosity will increase, resulting in printing difficulties.
2. What is the RoHS lead-free process commonly used in SMT patch processing and production
RoHS stands for Hazardous Substance Limit. RoHS, also known as Directive 2002/95/EC, originated in the European Union and restricts the use of specific hazardous materials found in electrical and electronic products (known as EEs). All applicable products on the EU market after 1 July 2006 must pass RoHS compliance
What are the RoHS restrictions on materials?
Substances prohibited by RoHS are lead (Pb), mercury (Hg), cadmium (Cd), hexvalent chromium (CrVI), polybrominated biphenyls (PBB), polybrominated diphenyl ethers (PBDE), and four different phthalates (DEHP, BBP, BBP, DIBP).
Why is RoHS compliance important?
Restricted materials are harmful to the environment and contaminate landfills, and are dangerous in terms of occupational exposure during manufacturing and recycling.
Due to environmental issues, Jingbang provides lead-free PCBA circuit board manufacturing services, whose surface finish requires strict concentrations of six hazardous substances, including lead (Pb), mercury (Hg), cadmium (Cd), hexvalent chromium (CrVI), polybrominated biphenyls (PBB) and polybrominated diphenyl ethers (PBDE). Of these six substances, lead is the most widely used in electronic electroplating. Therefore, lead-free is the best way for PCBA surface finish.
Our RoHS certificate.
PCBA production surface finish can be selected by the customer. In addition to HASL Lead-free, PCB manufacturers offer the following lead-free solutions:
Sink gold (ENIG)
Sunken silver
Sunk tin
Hard gold
If you always order leaded PCBA boards, we recommend that you choose one of these lead-free solutions later.
3. Reasons for component displacement caused by PCBA patch processing and production
The main purpose of SMT patch processing is to accurately install the surface assembly element on the fixed position of PCB. However, in the process of SMT patch processing, some process problems may occur, which will affect the quality of the patch, such as the displacement of the element. The displacement of the equipment presented in the patch processing is the foreshadowing of some other problems presented in the welding process of the equipment board, which needs attention. So what is the reason for the displacement of PCBA patch processing equipment? The following global Wei science and technology Xiaobian for us to analyze the introduction.
Reasons for unit displacement in PCBA patch processing:
1. The use time of solder paste is limited. After exceeding the use time, the flux will change and the welding will be poor.
2, the viscosity of the solder paste itself is not good, the equipment in the transfer of oscillation, shaking and other problems caused by the equipment shift.
3. The flux content in the welding paste is too high, and the excessive flux flow in the reflow welding process leads to the displacement of the element equipment.
4, the equipment in printing, patch after the transfer process due to vibration or incorrect transfer mode caused by the equipment shift
5, PCBA patch processing, the air pressure of the nozzle is not adjusted well, the pressure is not good, resulting in the displacement of equipment.
6. The mechanical problem of the SMT machine itself caused the incorrect placement of the equipment.
Once the device is shifted in the patch processing, it will affect the performance of the circuit board, so in the process of processing the need to understand the reasons for the device shift, and targeted processing