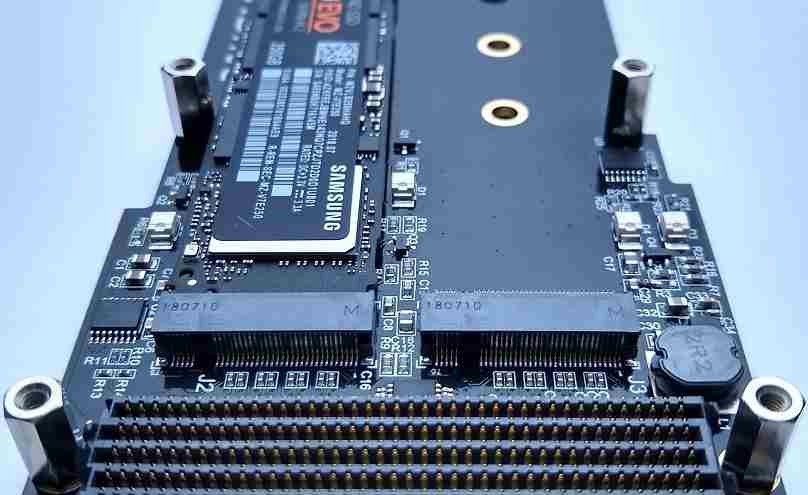
Customers often ask what is the difference between PCBA patch processing with lead and lead-free, and whether the widespread use of metal-free welding data means that all PCBA boards are metal-free. In fact, it is not certain that all SMT processing processes use metal-free welding data, because sometimes, the cost problem or other problems are fully considered. There will be a lot of PCB manufacturers using the lead process again. So how to know the PCBA plate spot welding on the market is heavy metal free or heavy metal free? There are three dimensions to this problem.
Welding surface appearance: On the circuit board, the surface of the lead welding data is bright milky white, while the non-heavy metal welding data is light yellow (because the non-heavy metal welding data has copper). PCBA is the general name of PrintedCircuitBoard+Assembly in English. In other words, the PCB blank board is manufactured by all the SMT patches or DIP software. PCBA is commonly called PCBA. It is a common writing in our country, as it is called the official idiom. If the welding data is rubbed vigorously, the non-heavy metal welding data will leave a light yellow impression in the hand, and the lead welding data will leave a gray black impression.
Solder material composition: Lead welding data is the two main components of tin and lead, and non-heavy metal welding data composition is less than 500PPM), non-heavy metal welding data generally with tin, silver or copper elements.
Main uses: lead products welding welding data, commonly used special tools and components for lead. The special tools and components used for heavy metal-free welding materials to be exported to foreign countries must be heavy metal-free.
Blend these 3 levels, we can clearly distinguish from a lot of PCBA board selection of non-heavy metal welding method of PCB board. PCBA processing SMT and DIP processing is full of integrated parts on the PCB board, the key difference is that SMT does not need to punch holes on the PCB, the PIN of the parts must be inserted into the hole already drilled in the DIP
2.SMT patch processing technology and flow
The basic process composition of SMT patch processing includes: screen printing (or dispensing), mounting (curing), reflow welding, cleaning, testing and repairing screen printing: its function is to leak solder paste or patch glue onto the PCB pad to prepare for the welding of components. The equipment used is screen printing machine (screen printing machine), which is located at the front end of SMT production line.
Solder paste printing: It is to print solder paste to PCB pad.
Curing: Its role is to melt the patch adhesive, so that the surface assembly components and PCB board solid bonding together. The equipment used is curing furnace, which is located behind the SMT machine in the SMT production line.
Mounting: Its function is to accurately install the external assembly components to the fixed position of the PCB. The equipment used is the SMT machine, which is located behind the screen printing machine in the SMT line. produce
Reflow welding: Its function is to melt the welding paste, so that the external assembly components and PCB board solid bonding together. The equipment used is reflow welding furnace, which is located behind the SMT machine in the SMT production line.
Cleaning: Its role is to assemble the PCB board above the welding residue harmful to human health, such as flux, and so on. The equipment used is a cleaning machine, the orientation can not be fixed, can be online, may not be online.
Detection: Its function is to assemble the PCB board welding quality and installation quality detection. The equipment used includes magnifying glass, microscope, online tester (ICT), flying needle tester, active optical testing (AOI), X-RAY testing system, functional tester, etc. Bearing according to the needs of detection, can be equipped in the production line of the appropriate local.
Repair: Its function is to detect the fault of PCB board rework. The tools used are soldering iron, repair workstation, etc. The equipment is located in any position in the production line.
SMT process test:
I. Single-side assembly:
Incoming material inspection => Silk screen welding paste (spot patch glue) => Patch => Drying (curing) => Reflux welding => Clean. Detection => repair
Two, double-sided assembly:
A: incoming material inspection => PCB side A screen printing solder paste (spot patch glue) => Patch => Drying (curing) => A-side reflow welding => Clean. Turn over a board. PCB side B screen printing solder paste (spot patch glue) => Patch => Dry => Reflow welding (preferably only for B side => Clean. Detection => Repair)
This process is suitable for PCB with PLCC and other large SMDS on both sides.
B: Incoming material inspection => PCB side A screen printing solder paste (spot patch glue) => Patch => Drying (curing) => A-side reflow welding => Clean. Turn over a board. PCB B spot patch adhesive => Patch => Cure => B side wave soldering => Clean. Detection => Repair)
This process is suitable for reflow welding on side A and wave soldering on side B of PCB. This process should be used in PCB B-side assembled SMDS as long as the SOT or SOIC(28) pin is below.
Iii. Single-side mixed loading process:
Incoming material inspection => PCB side A screen printing solder paste (spot patch glue) => Patch => Drying (curing) => Reflux welding => Clean. Plug-in => Wave soldering Clean. Detection => repair
Four, double-sided mixed loading process:
A: incoming material inspection => PCB B spot patch adhesive => Patch => Cure => Turn over a board. PCB side A plug-in. Wave soldering Clean. Detection => repair
Stick before insert, suitable for SMD components more than separate components
B: Incoming material inspection => PCB side A plug-in (pin bent) => Turn over a board. PCB B spot patch adhesive => Patch => Cure => Turn over a board. Wave soldering Clean. Detection => repair
Insert before paste, suitable for separate components more than SMD components
C: incoming material detection => PCB side A silk screen solder paste => Patch => Dry => Reflux welding => Plug-in, pin bent => Turn over a board. PCB B spot patch adhesive => Patch => Cure => Turn over a board. Wave soldering Clean. Detection => repair
Side A mixed, side B pasted.
D: incoming material detection => PCB B spot patch adhesive => Patch => Cure => Turn over a board. PCB side A silk screen solder paste => Patch => A-side reflow welding => Plug-in => B side wave soldering => Clean. Detection => repair
Side A mixed, side B pasted. First stick double-sided SMD, reflow welding, after insertion, wave soldering
E: incoming material detection => PCB side B screen printing solder paste (spot patch glue) => Patch => Drying (curing) => Reflux welding => Turn over a board. PCB side A silk screen solder paste => Patch => Dry => Reflow welding 1(optional partial welding) => Plug-in => Wave crest welding 2(such as less plug-in components, can use technology welding) => Clean. Detection => repair
Side A pasted, side B mixed.
V. SMT process ------ double-sided assembly process
A: Incoming material detection, PCB side A silkscreen welding paste (spot patch glue), patch, drying (curing), side A reflow welding, cleaning, turning over; PCB side B screen printing welding paste (spot patch glue), patch, drying, reflow welding (best only for side B, cleaning, testing, repair)
This process is suitable for PCB with PLCC and other large SMDS on both sides.
B: Incoming material detection, PCB side A silkscreen welding paste (spot patch glue), patch, drying (curing), side A reflow welding, cleaning, turning over; PCB's B-side patch glue, patch, curing, B-side wave soldering, cleaning, testing, repair)
This process is suitable for reflow welding on side A and wave soldering on side B of PCB. This process should be used in PCB board B-side assembled SMDS as long as the SOT or SOIC(28) pin is below.