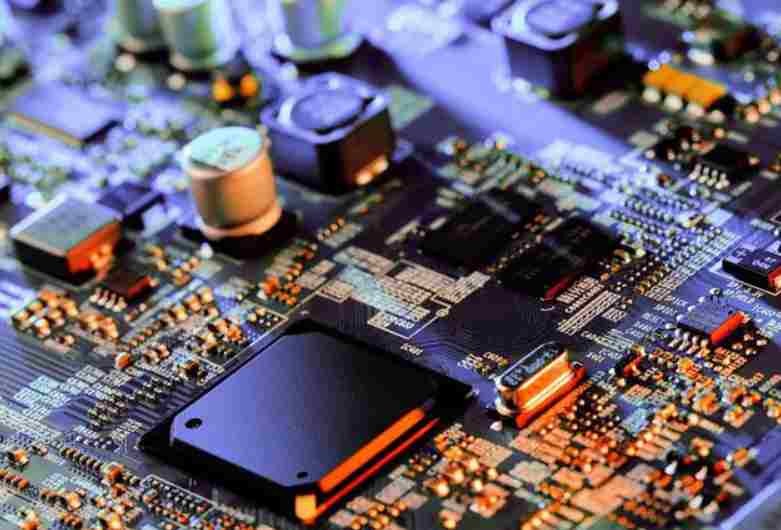
1. Welding is the most important link in smt patch processing. If it is not done well in welding, it will affect the entire production of pcb board. In order to avoid the impact of poor welding on smt machining quality, it is necessary to pay attention to welding.
To this end, we summarized the following seven factors that will affect welding, I hope you can help after reading.
First, welding heating bridge. The welding thermal bridge in the patch processing is to prevent the solder from forming a bridge, if there is a mistake in this process, it will lead to uneven distribution of solder. The correct welding method is to put the soldering iron head in the middle of the pin of the solder pad, so that the tin line is close to the soldering iron head, and when the solder paste melts, the tin line is moved between the solder pad and the pin, and the soldering iron is placed on the tin line, so as to produce a good solder spot and reduce the impact on processing.
Two, pin welding force. In the process of processing, the welding force of the pin is too large, which is easy to cause problems such as warping, delamination or depression of the welding plate of the patch. Therefore, in the process of welding, in order to ensure the quality of smt patch processing, it is not necessary to exert too much force, and only need to contact the soldering iron head with the pad.
Three, the choice of iron head. In the process of welding, the size selection of the iron head is also very critical. If the size is too small, it will increase the retention time of the iron head, resulting in the appearance of cold welding points. Too large a size will result in too fast heat and burn the patch. Therefore, we need to choose the size suitable for the iron head according to the length and shape of the iron head as well as the heat capacity and contact surface.
Four, temperature setting. Temperature is also a very important step in the welding process. Setting too high temperature will cause the welding plate to tilt, and excessive heating of solder will damage the patch. Therefore, we should pay attention to the setting of temperature, and setting a good temperature is particularly important for the processing quality.
Five, the use of flux. In the process of the implementation of the relevant process, if the use of flux is too much, it will lead to the stability of the bottom welding foot, which may cause corrosion or electron transfer.
Vi. Transfer welding operation. Transfer welding refers to placing the solder first on the iron head and then transferring it to the joint. If improper operation will cause poor wetting. Therefore, we should first place the soldering iron head between the pad and the pin. When the tin line is near the soldering iron head, wait for the tin to melt and move the tin line to the opposite side. Then place the tin wire between the pad and the pin. The soldering iron is placed on the tin line, and the tin line is moved to the opposite side when the tin is melted.
Seven, modify or rework. The biggest taboo in the process is to modify or rework in pursuit of perfection. And this practice should not only be repeated modification or rework in pursuit of perfect product quality, which is easy to cause so easy to cause the metal layer of the circuit board /pcb circuit board fracture
There is also the layering of the board, which not only consumes time but also may cause the scrap of the pcba plate, so do not carry out unnecessary decoration and rework.
2. Why is the production equipment of smt factory important?
First, advanced equipment is the premise of precision technology implementation
Global Wei Technology, as an enterprise engaged in Medical electronics, vehicle electronics and other high-end products PCBA processing customization. High-end products are not just a noun, strictly speaking it is a verb, is the need to pass a series of precision process under the product, is the crystallization of high-tech technology. For example, the current mainstream 7nm chip, if we use the machine 10 years ago to paste, we dare not guarantee that the paste will not succeed, at least we dare to guarantee that the paste rate will not reach 10%. Therefore, for automobiles, medical and other high precision products, the quality of welding is not only the strength but also the responsibility of life. If we do not have advanced equipment, no matter how detailed the process analysis in the smt process guide is, no matter how clear it is, it will be a matter of discussion.
Second, advanced equipment is the guarantee of market competitiveness
Any smt patch factory home, have their own unique strength points. But the core of competitiveness must be able to adapt to the market to provide customers with high quality products and services. Any superficial work in the electronics manufacturing industry will not make the product go smoothly. Under the premise of successful matching of engineering team and engineering process ability, advanced equipment becomes the icing on the cake operation, but also the guarantee of a factory to maintain its market competitiveness.
Third, advanced equipment is the basis of customer service
The core of the real economy is the ability to create real products through deep processing of raw materials and socialized labor. It is about every aspect of the nation, society and the individual. Therefore, as a part of China's physical manufacturing industry, kingford' s good service to our physical customers is our social responsibility and the meaning of existence. To provide services for customers is to achieve the delivery of finished products from drawings, so the pcba patch is a bridge between us and customers. Advanced production equipment is our service customer base.