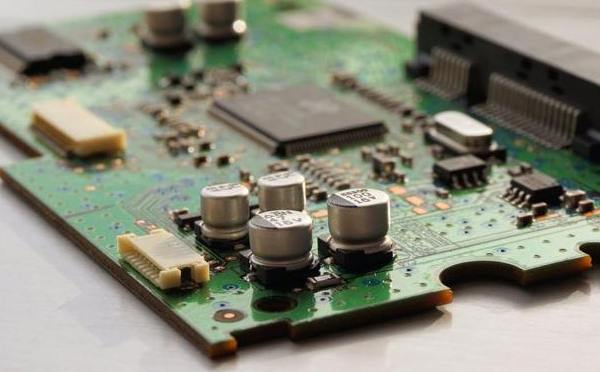
1. Now the domestic electronic processing industry is very prosperous, but serious material consumption and slow processing often occur in the SMT patch proofing, and these two conditions make the cost of developing sample patches become higher virtually. Therefore, today we will talk about how to avoid serious material consumption and high throwing rate in SMT patch processing.
First, in order to eliminate the high casting rate in the process of SMT patch proofing, human factors should not be ignored. For example, the common operation that leads to high casting rate is that the tearing belt is too long and the pressing material is too much when the operator install the material, which will result in material modification or loss. And the solution is that the operator should retain two or three slots when loading, and ensure that each link of the operation specification, it is best to have a unified elastic standard.
Second, in the process of SMT patch making and processing, there was also a situation that there were sundries on the table after the installation of feeder, resulting in shaking and unable to get the material. In this case, it is necessary to train the operator to check whether there are sundries on the machine table and feeder chassis when installing feeder, and clean the table of the machine timely when pulling. And in order to ensure that the material tray is not installed on the feeder, resulting in chucking or throwing, the operator must install the tray to the feeder when refueling
Third, in the process of SMT patch sampling, the high rate of throwing material may also be caused by placing the reverse board, picking the wrong board and wiping the board. The solution is still to require the operator to complete the work according to the standard operation process, and before the work, the position of the assembled board and the direction of entry board as well as the daily notes summarized in the guidance book should be marked. In this way, the construction efficiency and accuracy of the operator can be ensured.
The points just mentioned are that when SMT patch sampling is carried out, if the high throwing rate caused by human factors is avoided, and because many SMT patch processing is urgent, these details that need to be prepared in advance should be taken into account as soon as possible, so as to ensure the efficiency of the whole processing process and reduce the waste of resources.
2. Weld and inspect the first part of wave soldering after SMT patch processing
1, with automatic loading machine, or manual pcb circuit board gently placed on the conveyor belt (or fixture), the machine and equipment fully automatic spraying flux, low temperature drying, preheating, wave welding machine, refrigeration and other practical operations.
2. Catch the pcb circuit board by hand at the exit of the wave peak welding machine.
3. Conduct quality inspection of the first sample welding products in accordance with the standard specification "Welding Spot Product Quality Evaluation" SJ/T10666-1995 or IPC-A-610E. According to the welding results of the first sample, the main welding parameters can be adjusted until the quality of the product meets the requirements of continuous batch production and processing.
We have stressed the inspection of pcb circuit board first sample in advance, its necessity need not be said. Why does the first sample test need to be carried out after the wave welding machine?
In fact, the key production process of pcb board includes: solder paste printing, SMT patch, reflow furnace welding, DIP plug-in, wave welding machine. If there is no problem, through the wave welding machine welding PCB circuit boards can be taken back to assemble into development products.
So if we have to produce and manufacture a product that has already gone through the production process without testing, if the quality of the product is not normal, then the assembled product will also have to be dismantled and repaired.
Therefore, in addition to the case where the user clearly states that the first sample inspection is not necessary, in other cases, the pcb circuit board manufacturer must carry out the first sample inspection after the wave welding, and confirm with the user after passing the inspection. The next step is to carry out mass production and mass production and processing, which is a feasible solution.
3. How long does it take for PCBA processing to calculate the quotation?
In general, we say how long it takes for pcba to process the latest quotation, which starts from which links are included in pcba manufacturing. Perhaps we all know that PCBA is a general term for PCB welding in China, which includes 3 parts (PCB circuit board, SMT patch, component welding), so the latest quotation of PCBA must be determined by these 3 parts.
1. PCB plate: PCB board making data and board making specification documents required for the latest quotation. If the information is complete and all the information is sorted out well, how much money does the special process need to use a separate charge, plus other incidental fees are basically 2 hours can be quoted a complete set of prices out. Not if there are a lot of new offers waiting in front of you.
Two, SMT patch processing plate: this module is mainly an accounting of processing fees. General PCBA factories are according to the number of points to count money, some a piece of a point, some a foot a point, this is the biggest trick, a piece at least 2 feet, if a point may be a single point price will be higher than a foot to count a point price, after all, the number is less, no one to do a loss of money. So don't look at an expensive point and not evaluate it. This can be done in less than an hour.
Three, components module: components include conventional resistance and tolerance and special devices. At present, the market of conventional components is transparent and it is relatively easy to evaluate the price, but some special BGA/IC will be more troublesome. For example, the high-profile Huawei incident in recent two years, many special components will be involved in international embargo, strict approval process, long clearance time and unstable price. So the latest quotation cycle is generally 3 to 4 days.
Basically, after the above decomposition, we will find that the latest quotation of PCBA takes several working days, unless the enterprise with its own reserve materials can evaluate in a very short time, other things may only be PCB and SMT patches relatively fast. There are also some situations, such as a large number of orders, the latest quotation list is very tight, it must be who comes first for who is the first to quote, after all, customers are treated equally.