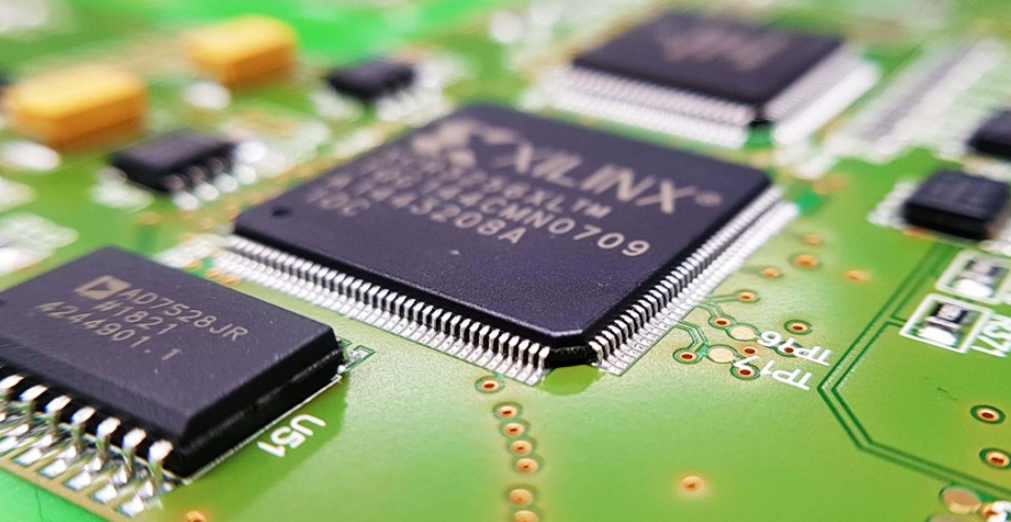
The normal coating thickness of most PCB products in PCBA processing is 25 to 127 microns, and the coating thickness of some products is even lower. The specific thickness should be determined according to the actual use scenario and customer requirements.
How to use the tool to measure the coating thickness of three anti - paint?
Circuit boards must use the thinnest coating material to provide maximum protection in order to minimize heat retention, additional weight gain, and various other issues. There are three main ways to measure the thickness of conformal coatings.
1, wet film thickness meter
Wet film thickness can be measured directly using a suitable instrument. These meters contain a series of notches, each tooth having a known calibration length. A film measurement is made by placing the meter directly on the wet film, and this measurement is then multiplied by the percentage of solids of the coating to calculate an approximate dry coating thickness.
2. Micrometer
Micrometer thickness measurements were made at several locations on the board before and after coating occurred. The cured coating thickness is subtracted from the uncoated thickness and divided by 2 to obtain the thickness on one side of the plate. The standard deviation of the measurement is then calculated to determine the uniformity of the coating. A harder coating that will not deform under pressure is preferred for micrometer measurements.
3. Ultrasonic thickness measuring instrument
The meter uses ultrasonic waves to measure coating thickness. It has the advantage over eddy current probes because it does not require a metal back. The thickness depends on the amount of time it takes for sound to travel from the transducer, through the coating, and reflect back off the PCB surface. This method is relatively safe and will not damage the PCB board.
The thicker the coating thickness, the better the effect misleading many users think that the thicker the better. In fact, three anti paint is divided into: acrylic three anti paint, silicone three anti paint, polyurethane three anti paint, different kinds of three anti paint coating thickness requirements are different, industries on three anti paint coating thickness requirements are not the same.
Because each type of product has different requirements for coating thickness in the process of use, each product has different coating thickness in different environments and different needs.
For example, ordinary electronic products, the three anti paint requirements are not particularly high, there is no special thickness requirement when coating, generally 20-30 micron thickness can meet. Special requirements can be taken multiple coating, to be fully cured on the board after the three anti paint for the second coating.
And industrial products and military products on the performance of the three anti paint is relatively high, the thickness of the coating is about 30-50 microns, at the same time, the selection of relatively better performance of the three anti paint types, play a better role in protecting the PCB circuit board.
Three anti-paint spraying steps
Step 1: clean the board surface, keep the board surface without oil dust (mainly in the welding process of residual solder flux composition, because it is mainly acidic substances will affect the durability of components and three anti-paint adhesion with the board surface,
Step 2: drying, to clean the cleaning agent and water are dried to ensure that the board is dry,
Step 3: Deploy three anti-paint according to the data provided by the manufacturer of three anti-paint to deploy the appropriate viscosity of three anti-paint, it is recommended to adjust the viscosity of the appropriate ratio to 15-18 seconds, stir evenly, and then stand for 3-5 minutes to let the bubbles completely disappear, you can load into the spray gun spraying, if brush brush, it is recommended to buy a soft wool brush, (The hard hair of the pig brush should be brush marks on the surface of the paint film after the brush is rough and hard. The surface of the paint film is not smooth, which will affect the appearance, and the pig brush will produce bubbles if it is too hard in the construction.)
Step 4: Spraying, three anti paint with 200 mesh filter into the spray can, adjust the air pressure and spray shape of the spray gun, the pressure is too small three anti paint atomization is not good spray out of the paint film will have small pits, especially when the viscosity of the paint is a little larger, Similar to the surface of the orange peel (the surface of the board when there is oil will appear like the appearance of the orange peel) when the air pressure is too big three anti paint spray on the surface will be blown open by the air pressure paint will appear in a pile of piles, in the process of drying will appear flow hanging. It is suggested to adjust the spray gun spray shape to fan, nozzle and board into 45° Angle of uniform movement of the spray gun to spray evenly on the board, spray the first gun back to the second gun is to make the second gun paint mist pressure the first gun paint film, and so on until all spray finish the board, so as to ensure the uniform paint film will not leakage. The speed of the spray gun can not be too fast according to the data of the three anti-paint to ensure that the paint film can have a thickness of at least 50 microns.
Step 5: Bake the board after spraying into the baking box to bake, according to the data provided by the three anti paint factory set the curve baking temperature, the three anti paint is self-drying if it is vertical baking box then it is recommended to stand outside for 3-5 minutes after entering the baking box of no more than 80 degrees to bake for 5-10 minutes, If it is a tunnel furnace, it is recommended to set the front area at 60 degrees, the middle area at 80 degrees and the back area at 70 degrees. Spraying good surface if directly into the high temperature baking then the surface of the paint film than inside the paint dry faster, is equivalent to a layer of film to the bottom of the paint wrapped in the inside. When the bottom of the paint in the drying process of the solvent needs to volatilize is volatilized will not come out of the surface of the membrane drum through, will form a lot of pores and bubbles.
Step 6: detect the printed circuit board, the board inside the baking oven that out to detect whether there is leakage jet bubble, the board paint film is uniform and complete without bubbles.
Baking temperature of three anti - paint
At room temperature, 10 minutes dry, 24 hours curing, if you want to hurry up, you can bake at 60 degrees temperature for 30 minutes, you can meet the curing requirements. Good quality three anti paint, 80 temperature baking for half an hour, you can be completely cured.