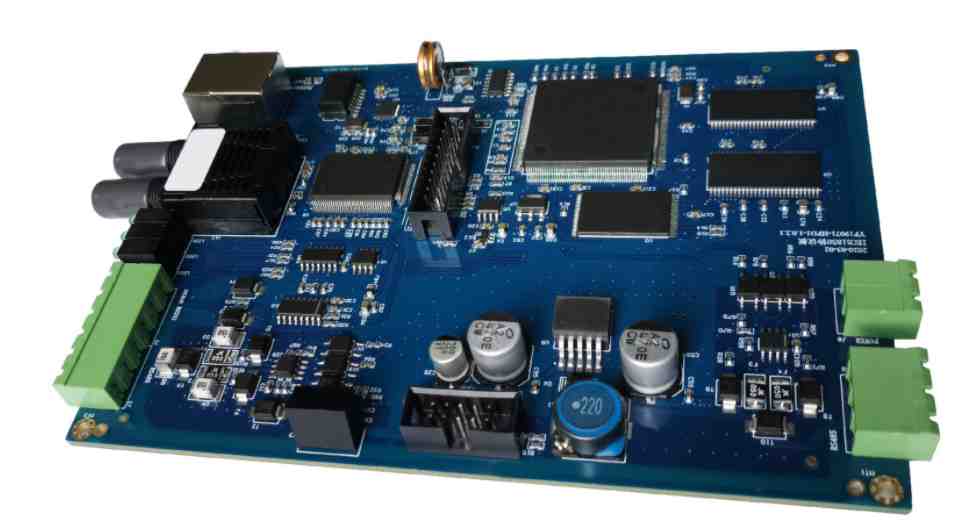
The main reason for the monument is that the solder paste in the molten state, the surface tension at both ends of the pad is not the same, resulting in the material force imbalance, material erection caused by dewelding. We also call the stele phenomenon the stele, drawbridge, and Manhattan phenomenon. The stellage phenomenon occurs in the reflow welding process, and the smaller the component volume, the more likely it is to occur. Therefore, many small CHIP components, especially patch resistors, are prone to this problem in actual production.
The causes of stele cannot be separated from solder paste, parts, base plate design and reflow welding process. The causes of stele are analyzed below. When stele effect occurs, we will confirm and improve the yield of SMT production.
First, the welding pad design is unreasonable:
The pad design and layout is not reasonable, if the pad design and layout have the following problems, it will cause the uneven wetting force on both sides of the component.
1. The test results on the relationship between the size of the pad and the occurrence rate of the tablet phenomenon show that the smaller the size of the pad, the less likely to occur the tablet phenomenon, this is because after the size of the pad is reduced, the coating amount of solder paste is reduced, and the surface tension of the solder paste when melting is also reduced. When the solder pad spacing is too large, it will cause the solder to moisten the element terminal, and the wetting force will pull the element to offset and separate from the solder paste. Usually, in order to avoid the problem of stele, it is recommended that the size of the pad, especially the inner spacing, should meet certain requirements. Therefore, in the design, under the premise of ensuring the strength of welding points, the size of the pad should be as small as possible.
2. The size of the pad is inconsistent and the heat capacity is different
1) One of the components on both sides of the pad is connected with the ground wire or there is a side of the pad area is too large, the shape and size difference of the welding end is large, the heat capacity of the pad is large, the weldability is poor, the surface of the pad and the component is oxidized, the weight of the component is too light, the heat capacity of the two ends of the pad is not uniform.
2) The thermal conductivity of PCB substrate material is poor, the thickness uniformity of the substrate is poor, and the temperature difference on the PCB surface is too large, resulting in uneven heat absorption on both sides of the component pad.
3) Large devices QFP, BGA, radiator around the small chip components at both ends of the pad will appear uneven temperature.
Two, solder paste and solder paste printing
Solder paste factors:
1. Due to poor flux uniformity of solder paste; Tin paste activity is not high; The reason for the poor weldability of components causes the surface tension of solder paste in the molten state is not the same, causing the uneven wetting force of the solder pad.
2. The printing amount of solder paste on two pads is not uniform. One side of the solder paste will absorb more heat and melt time lag, so that the wetting force is not balanced.
Factors affecting solder paste printing thickness:
SMT patch component stele causes and solutions
(1) To reduce the thickness of the steel mesh plate is to reduce the amount of solder paste, and the surface tension of the solder paste when it melts is reduced. When the thickness is reduced, the solder paste is thinner, the heat capacity of the whole pad is reduced, and the probability of the solder paste melting on the two pads is greatly increased.
Solder paste printing factors:
If the steel mesh holes in order to avoid the problem of tin beads and increase the spacing between the pad, or solder paste printing offset, the probability of reflux welding will increase. Therefore, the control of solder paste printing problem is very key, of course, this is easy to find in the actual production. However, the opening design of steel mesh is more difficult to find, and it is usually recommended that the opening spacing of steel mesh be consistent with the C value in the table.
The size of the opening hole of the general template of the steel mesh should be 10% smaller than the corresponding pad, and the second way is recommended
In the design of steel mesh, keeping proper value in the inner distance of two mesh holes can effectively prevent the occurrence of stele.
SMT patch component stele causes and solutions
3. Patch displacement
Element positioning, Z-axis direction force is not uniform, will lead to the element immersed in the solder paste depth is not uniform, melting due to the time difference will lead to the wetting force on both sides of the imbalance, if the component patch shift will directly lead to the monument.
In general, the component offset produced during mounting is automatically corrected during reflux by pulling the component due to surface tension when the solder paste is melted, which is called "adaptive". But when the deviation is serious, pull will make the element stand up instead, producing the phenomenon of erecting tablet.
This is because: the heat transfer from the welding end of the SMD patch element to the solder paste is uneven, and the end with less solder paste melts first when heated; The stickiness between the ends of the component and the solder paste is uneven.
With the continuous improvement of mounting precision, the smaller 0603, 0402, 0201 and other components are more and more used, but the vertical tablet phenomenon caused by mounting offset accounts for a greatly increased proportion of the entire defect incidence, becoming a key factor. This requires optimizing the mounting procedure.
Four, the furnace temperature curve is not correct
If the reflow furnace body is too short and the temperature zone is too small, the working curve of PCB heating will be incorrect, resulting in uneven temperature distribution in the reflow furnace and uneven temperature distribution on the board surface, so that the humidity difference on the board surface is too large, resulting in uneven wetting force.
Adjust the appropriate temperature curve according to different products; It is necessary to consider the thermal balance of the entire PCB board. If the heat difference on the PCB board is large during reflux, it may lead to thermal shock problem; if the temperature rises too fast, the heat distribution on the PCB board may be unbalanced and the stele problem may occur. The temperature rise slope is less than 2°C per second. Reflow welding furnace must first test when welding, find the appropriate temperature curve process before mass welding.
5. Oxygen concentration in nitrogen reflow welding
Nitrogen reflux can effectively improve the welding quality. Generally speaking, if a nitrogen furnace is used, the reoxidation of PCB, PAD, tin powder particles and other parts will be effectively inhibited due to the protective effect of nitrogen during the heating process. Therefore, the FLUX can be quickly welded without too much oxide hindering. Its dissolving time is faster, its instant tension becomes stronger. If the parts at this time as long as slightly unbalanced nitrogen will be more likely to show this imbalance, resulting in a monument.
However, there is no standard value. According to practical experience, too low oxygen content may lead to the erection of the monument. Oxygen content greater than 1000PPM generally will not lead to the erection of the monument. Usually the oxygen concentration is controlled at 1000-1500ppm, which is conducive to the completion of welding and not easy to erect the monument.
The use of better solder paste and nitrogen has the same wonderful, nitrogen belongs to the "preventive measures" to avoid parts, PCB PAD tin powder particles in the heating process of oxidation, the use of better solder paste belongs to the "treatment measures", the generated oxides can be quickly and effectively removed, from the wetting balance can be seen, The solder paste with better solder quality has faster wetting time. If the parts are slightly unbalanced at this time, the solder paste with better solder quality is easy to show this imbalance, resulting in a monument.
conclusion
1. The root cause of the tablet component is the uneven wetting of the solder to the two welding terminals;
2, the same design of two pads, size, inner distance, heat capacity and other aspects of balance can prevent the occurrence of monument, using Thermal relief design can avoid the problem of monument;
3. In the design of steel mesh, maintaining the appropriate value on the inner distance of the two mesh holes can effectively prevent the occurrence of stele;
4, if the quality of the installation is not good, the equipment accuracy is limited, too large deviation may also lead to the problem of the monument;
5. Rapid temperature rise may lead to uneven heat distribution on PCB board and lead to stele problems. A temperature rise slope of less than 2°C per second can prevent stele problems.
6, nitrogen reflux can effectively improve the welding quality, but the oxygen content is too low and may lead to the occurrence of monument, oxygen content greater than 1000PPM generally will not lead to monument problems;
7. In the weldability test, it is necessary to pay attention to the balance of wetting time and wetting force in the two terminals of the component, otherwise the stele problem is inevitable