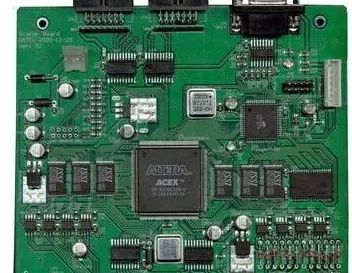
In the process of SMT chip production and use, improper operation will inevitably occur in the whole manufacturing process and use of PCBA, including machining errors, improper use, parts aging and other factors that may lead to abnormal work, and even affect the use of the whole product. However, many products do not need to be completely replaced. At this point, it is necessary to repair and maintain the internal circuit board. The following is kingford's maintenance method.
Inspection module
When SMT Chip Factory products need to be repaired, it is necessary to first determine if there are any errors, omissions and reversals in the components of each solder joint. It is also the case to confirm that no material is authentic. If we eliminate errors, omissions, inversions and issues of authenticity, we can take a faulty circuit board and first check that the circuit board is intact, that each component is apparently burned out and that it is inserted correctly.
Welding condition analysis
Circuit board defects are basically 80% solder spot defects. Whether the welding of the joint is sufficient and abnormal, we should refer to the ISO9001 quality system management standard first. It is also necessary to refer to various SMT machining welding quality standards to check for any obvious defects such as false soldering, false soldering, short circuit, and noticeable lifting of copper skin. If yes, we need to repair the defect point of the product, if not, you can continue to the next step.
Component orientation detection
In the process, we basically eliminated some of the visible defects. Now, we still have to carefully check the most commonly used components on the circuit board, such as diodes, electrolytic capacitors and other directional regulations, or if the components required for the negative electrode are inserted in the wrong direction.
Tool inspection of parts
If all visual judgments are correct, then we need to borrow some AIDS at this point. It is most commonly used in SMT chip factories to use multimeters to simply measure our components, such as resistors, capacitors, transistors, etc. The main test is to check whether the resistance value of these components does not conform to normal values, whether it is large or small, whether the capacitor is open, whether the inductor is open, etc.
Power-on test
After all of the above processes are completed, the general problems of the components are essentially eliminated and the circuit board is not ablated and damaged by short circuits or Bridges. Then you can plug in the power and check whether the corresponding function of the circuit board is normal
2. Hot day circuit board surface is easy to "oxidation leads to tin"!
Sequence: there is a quality complaint: the solder surface is not on the tin high occurrence period for summer, a winter will disappear without a trace or lower, like seasonal disease, in this systematic for everyone to answer questions and how to prevent some basic problems!
One: Why do not tin occur more in summer, high temperature to promote oxidation?
1) Because of the hot weather, such as PCB from more than 30 degrees of outdoor to 22 degrees of indoor, it is very easy to lead to the PCB surface "sweating" phenomenon, which may lead to PCB moisture resulting in surface oxidation
2) If the internal environment of the SMT factory is not good or the temperature is high after the PCB is unpacked, if the air is acidic or alkaline, the surface will be oxidized easily under the catalysis of high indoor temperature, which will lead to no tin
3) During SMT welding, please pay special attention not to touch PCB with hands and wear white gloves to prevent PCB surface oxidation
4) It is particularly important to pay attention to that after welding one side, we should weld the other side as soon as possible, otherwise it is very easy to pollute the other side when welding the first side, leading to the tin on the other side of the tin
5) After brushing the solder paste, the furnace must be immediately, or the chemical composition of the solder paste will lead to oxidation of the solder pad
Two: Have lead spray tin, lead-free spray tin, sinking gold that kind of process is easy to tin, not easy oxidation?
Lead spray tin is the best on tin, complaint rate is relatively low, gold is also on the surface of the relatively easy oxidation, and the least easy on the tin is lead-free spray tin, because lead-free solder joint is high, if not because your products have strict requirements recommended to use lead, military enterprise board is all with lead spray tin!
Three: How to avoid losses and reduce disputes?
This is very important, please read carefully: the most difficult thing to distinguish the responsibility is the solder plate is not tin, involving circuit board factory, customers, and SMT welding factory, so in order to reduce disputes,
1. The SMT factory must be asked to brush several pieces of solder paste through the furnace before welding to check the tin condition. If the situation is abnormal, stop welding and check the reason
2, double-sided welding, need to complete the tin test on both sides of the tin effect
3, Jialichuang for a large amount of lead-free tin spray plate, generally before leaving the factory will do hand plate, tin immersion test together to the customer!
Iv. Quality disputes and resolution
Under the condition of full guarantee until 3 o 'clock, if there is any problem of tin failure, you will immediately complain to our system, and we will ask you to send some unwelded boards to us for welding test (Calictron opens steel mesh and gives it to Calictron SMT factory department for furnace test). If there is no problem in furnace test, it appears that your SMT welding has some problems. If the solder can not be welded, we will oxidize it and give it to Jialichuang for processing! So try to do a good job of welding the first side!