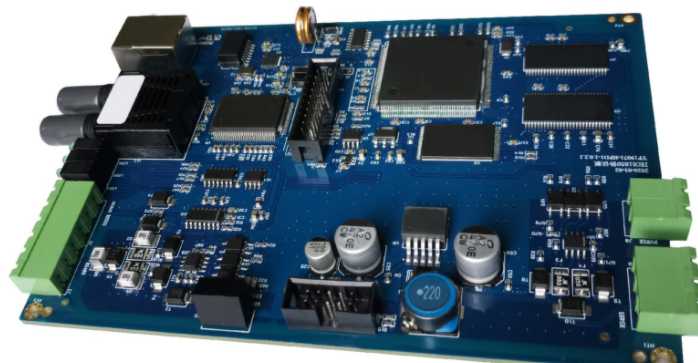
1. Recently, some customers have inquired about the problem of SMT solder joints' gaping, which puts forward high requirements on the product's gaping rate. All circuit boards used in medical ventilators need to be stable and reliable at all times. Planners emphasize that the assumption of emptiness will increase the oxidation of the product, leading to the deepening of the aging reaction of the product in advance. It has certain influence on the stability of the later stage of the product. Therefore, in order to reduce the cavitation rate, vacuum reflow welding equipment is required in the patch processing. As more and more new products are produced, there is a higher demand for quality. On the demand of new equipment, the investment of new equipment on the demand of PCBA processing plant constantly trudge SMT processing technology talent, together to increase the training and teaching of technicians. In order to ensure the high standard of welding quality, in order to trek product reliability and stability.
However, standing in the SMT patch processing point of view is unavoidable.
Any manufacturer can not say that their patch welding spot is not a little empty.
So how does emptiness come about? What are the causes of vagueness? Through the engineering technology of kingford, it is mainly caused by the following reasons:
First, welding paste. The different alloy composition of the solder paste and the size of the particles will form bubbles in the process of solder paste printing. Some air will continue to remain in reflow welding, and it will produce emptiness after splitting through high temperature bubbles.
Two, PCB welding pad surface treatment. Pad surface treatment also has a critical effect on the production of gaping.
Three, reflux curve setting. It is assumed that the temperature of reflow welding is too slow or too fast, which will make the residual air inside unable to be useful for cleaning.
Four, reflux environment. This is a reference to whether the equipment is vacuum reflow soldering.
Five, pad planning. Pad planning is not reasonable, is also a very important reason.
Six, micropores. This is one of the most simple ignored points, assuming that there is no reservation of microholes or incorrect orientation, may produce emptiness.
The above is kingford for you to provide some reasons for SMT patch processing blank analysis
2. How to analyze the solder paste printing quality of smt patch factory?
About a kind of technology in patch processing, in fact, tin paste process in patch processing, tin paste printing is a very conventional production process, but recently some friends say that this process often has some quality problems, so today Xiaobian to give friends a simple summary, so interested friends go on to see, there are problems in our summary process:
The first kind: insufficient solder paste (partial lack or even overall lack) will lead to insufficient solder solder quantity of components after welding, components open circuit, components offset, components erect.
The second: solder paste adhesion will lead to circuit short welding, components offset.
The third kind: solder paste printing overall offset will lead to poor welding of the whole plate components, such as less tin, open circuit, offset, vertical parts, etc.
The fourth: solder paste pull tip easy to cause short circuit after welding.
Of course, we are equipped with equipment to detect defects caused by solder paste printing, that is, SPI solder paste detector. What does SPI solder paste detector detect?
It is mainly used to detect the bad volume, area, height, deviation, loss, damage, height deviation of solder paste printing, in order to ensure the quality of solder paste printing,