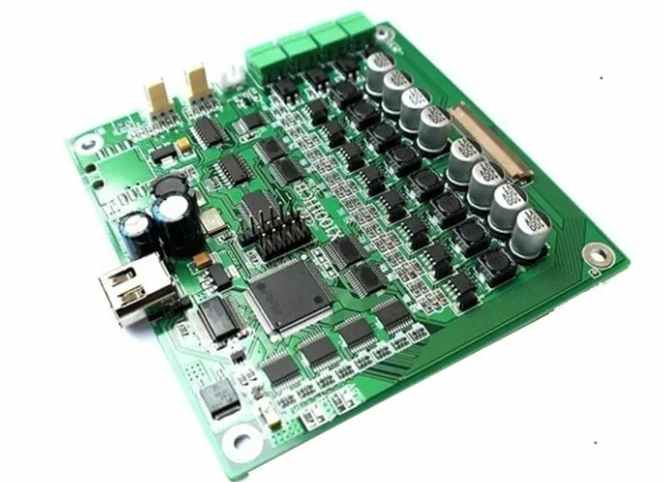
1.PCBA patch processing involves a series of processes such as PCB board manufacturing, pcba incoming materials component procurement and inspection, SMT patch processing, DIP plug-in processing, post-welding processing, program burning, PCBA testing, aging, etc. The supply chain and manufacturing chain are long, and defects in any link will lead to the mass quality of PCBA finished products. Cause serious consequences. Therefore, the quality management of the whole pcba processing process is particularly important.
Then kingford brings analysis from the following aspects:
1.PCB circuit board manufacturing
It is particularly important to hold a pre-production meeting after receiving PCBA processing orders, which mainly involves process analysis of PCB drawings and documents, and submission of manufacturability reports (DFM) according to different customer requirements. Many small manufacturers do not pay attention to this, the result is not only easy to produce poor quality problems caused by poor PCB design, but also produce a lot of rework and repair work.
2. Procurement and inspection of PCBA incoming materials
It is necessary to strictly control the procurement channels of components, which must be obtained from large traders and original factories, so as to avoid the use of second-hand materials and counterfeit materials. In addition, a special PCBA incoming material inspection post should be set up to strictly inspect the following matters to ensure that the components are trouble-free.
①PCB: Check the temperature test of reflow welding furnace, whether the hole of non-fly line is blocked or ink is leaked, and whether the board surface is bent, etc.
②IC: Check whether the screen printing is completely consistent with the BOM, and store it at constant temperature and humidity.
③ Other commonly used materials: check screen printing, appearance, power measurement, etc.
3.SMT patch processing
Solder paste printing and reflow furnace temperature control are the key points of SMT assembly, and it is necessary to use laser steel mesh which requires higher quality and can better meet the processing requirements. According to the requirements of PCB board, part of the need to increase or reduce steel mesh holes, or U-shaped holes, according to the process requirements of steel mesh can be made. The temperature control of the reflux furnace is critical to the wetting of the solder paste and the solidity of the PCBA, and can be adjusted according to the normal SOP operating guidelines.
In addition, strict implementation of AOI test can greatly reduce the adverse effects caused by human factors.
4. Plug-in processing
In the process of plug-in machining, the die design details for over wave soldering are the key. How to use the mold carrier to greatly improve the yield, this is the process experience that PE engineers must constantly practice and summarize.
5. Program burning
In the previous DFM report, the customer may be advised to set up some test points on the PCB (test points) to test the PCBA circuit connectivity after the PCB has welded all the components. If you can, you can ask the customer to provide the program, which can be burned into the master IC through the burner, so that various touch actions can be tested more intuitively in order to verify the functional integrity of the entire PCBA.
6. Test the PCBA
For orders with PCBA test requirements, the main test contents include ICT (circuit test), FCT (functional test), aging test, temperature and humidity test, drop test, etc.
In fact, PCBA processing process and PCBA incoming materials of this knowledge is far more than these, each of the above points can be detailed in a long length. This paper only expounds the key points of quality control of PCBA custom processing from a macro perspective, hoping to be helpful to practitioners.
2. What should we pay attention to during smt patch processing?
1. SMT patch processing technicians should wear the electrostatic ring that has been verified and OK, and check the electronic components of each order without mistakes, mixing, damage, deformation, scratches and other undesirable phenomena before plug-in.
2, the plug-in board of the circuit board needs to prepare the electronic materials in advance, pay attention to the capacitor polarity direction must be correct.
3. After the completion of SMT printing operation, check the defective products without missing insert, reverse insert, dislocation, etc., and transfer the good tinning finished products to the next process.
4. Before SMT patch processing and assembly, please wear electrostatic ring, keep metal sheet close to wrist skin and well grounded, and work alternately with both hands.
5, USB/IF seat/shield cover/high frequency head/port terminals and other metal components, plug-in must wear finger cover operation.
6. The position and direction of the inserted components shall be correct. The components shall be attached flat to the board surface and the height of the components shall be inserted into the position of foot K.
7. If the material is found inconsistent with the specifications in SOP and BOM, report to the team leader in time.PCB board
8. Materials should be handled with care. Components should not be damaged due to that has gone through the early stage of SMT patch processing.
9. smt SMT processing staff shall clean the working table before going to and from work and keep it clean.
Our kinggord is mainly engaged in SMT patchprocessing, DIP plug-in processing, post-welding processing, testing and other processing services