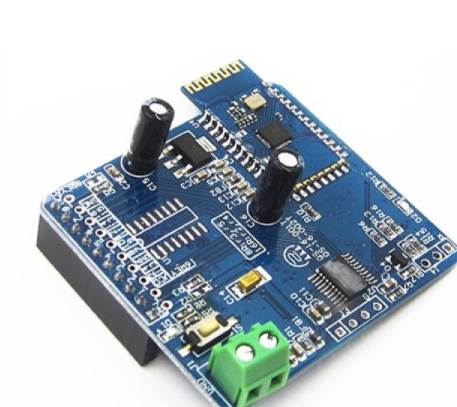
1. There is a chemical reaction between the flux and the alloy surface in SMT patch processing plant, so different alloy components should be selected different flux.
2, due to the poor wettability of lead-free alloy, it requires high activity of patch processing flux.
3. Due to the poor wettability of lead-free alloys, the amount of flux needs to be increased, so the post-welding residue is required to be less and non-corrosive to meet the ICT probe capacity and electromigration.
4. The melting point of lead-free alloy is high, so the activation temperature of the patch processing flux is required to be appropriately increased to adapt to the high temperature of lead-free welding.
5, lead-free flux is water-based solvent-based flux, welding if the water is not completely volatile, will cause solder splash, pores and holes. Therefore, it is required to increase the preheating time, and the welding time of manual welding is longer than that of lead welding.
6. SMT patch lead-free flux must be specially prepared. In the early days, lead-free solder paste was simply a clean solder of Pb-Sn mixed with lead-free alloy, with poor results. The chemical reaction between the flux and the solder alloy in the solder paste affects the rheological properties of the solder paste (which is critical for printing properties). Therefore, lead-free flux must be specially formulated.
Solder for SMT patch
To develop a new type of flux with stronger activity and better wettability, it is necessary to match the preheating temperature and welding temperature, and meet the environmental requirements of lead-free and non-cleaning flux to meet the needs of lead-free welding.
2. Failure cause analysis of PCBA patch processing plant!
PCBA patch processing and production process, due to the influence of operational errors, easy to lead to the poor PCBA patch!
Such as: air welding, short circuit, warping, missing parts, tin beads, warping feet, float high, wrong parts, cold welding, reverse, reverse white/reverse, offset, component damage, less tin, more tin, goldfinger sticky tin, overflow glue, etc., need to analyze these bad, and improve the quality of products.
First, PCBA air welding
1, the activity of tin paste is weak;
2, the steel mesh opening is not good;
3, copper platinum spacing is too large or large copper paste small components;
4, the pressure of the scraper is too large;
5, the element foot flatness is not good (foot warping, deformation)
6, the temperature of the preheating area of the backwelding furnace is too fast;
7,PCB copper platinum is too dirty or oxidized;
8,PCB board contains water;
9, machine mounting offset;
10, solder paste printing offset;
11, the machine splint track is loose, resulting in mounting deviation;
12. MARK point mislighting causes component deflection, leading to air welding;
Two, PCBA short circuit
1. The distance between the steel mesh and PCB board is too large, resulting in too thick solder paste printing short circuit;
2, the component mounting height is set too low will squeeze the solder paste resulting in short circuit;
3, backwelding furnace temperature rise too fast;
4, component mounting offset;
5, the steel mesh opening is not good (too thick, pin opening is too long, opening is too large);
6, the solder paste can not bear the weight of components;
7, steel mesh or scraper deformation caused by solder paste printing is too thick;
8, the activity of tin paste is strong;
9, empty paste spot sealing adhesive paper rolled up resulting in the peripheral component solder paste printing is too thick;
10, reflow vibration is too large or not level;
3. PCBA is warped
1, the size of the two sides of copper platinum produced uneven tension;
2, the preheating rate is too fast;
3, machine mounting offset;
4. Uneven thickness of solder paste printing;
5. Uneven temperature distribution in the backwelding furnace;
6, solder paste printing offset;
7, the machine track splint is not tight resulting in mounting deviation;
8. The head of the machine shakes;
9, the activity of tin paste is too strong;
10, improper furnace temperature setting;
11, copper platinum spacing is too large;
12,MARK point error caused by the yuan melodious hit
Four, PCBA missing parts
1, vacuum pump carbon sheet poor vacuum is not enough to cause the lack of parts;
2, sucking nozzle blocked or sucking nozzle bad;
3. Improper component thickness detection or bad detector;
4. Improper mounting height setting;
5, suction nozzle blowing too much or not blowing;
6, suction nozzle vacuum setting is improper (suitable for MPA);
7, the special-shaped component mounting speed is too fast;
8, head trachea broken;
9, valve seal ring wear;
10. There are foreign bodies on the side of the backwelding furnace track to erase the components on the board;
Five, PCBA tin beads
1. Insufficient preheating for reflow welding and too fast heating;
2, the solder paste after refrigeration, return temperature is not complete;
3, the solder paste hygroscopic splash (indoor humidity is too heavy);
4,PCB board water content is too much;
5, add excessive diluent;
6. Improper design of steel mesh opening;
7, uneven tin powder particles.
6. PCBA deviation
1. The positioning reference point on the circuit board is not clear.
2, the positioning datum point on the circuit board and the datum point of the network board are not aligned.
3. The fixed clamping of the circuit board in the printing press is loose. Positioning thimble is not in place.
4. The optical positioning system of the printing press fails.
5, solder paste leakage screen plate opening and circuit board design documents do not conform to
In order to improve the defects of PCBA patches, strict checks should be carried out in each link to prevent the problems of the previous process from flowing to the next process as little as possible.