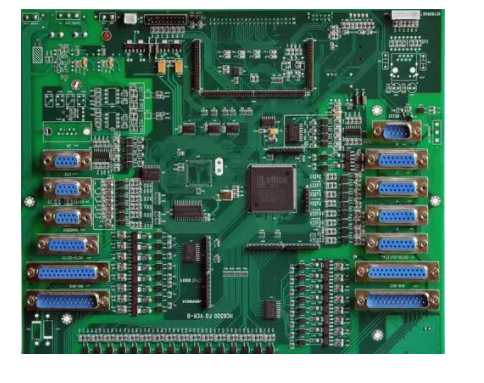
The pcb manufacturing process of the new order and the returned order is different, then what is the process of the new pcb order mounting?
(1) Preparation of pcb files (gerber files and bom files) in the early stage
(2) Off-line programming, input the data in gerber and bom list into the installed computer through programming
(3) Preparatory work before Pcb assembly (components, pcb, solder paste)
(4) Startup of all pcb manufacturing equipment
(5) According to the feeder, put the component material tray to be assembled on the Feida for preparation.
(6) Online programming, through online programming to check whether the data is consistent.
Automatic pcba welding process
(7) After the solder paste printing of pcb board, pcb mounting.
(8) The first piece of Pcb prototype circuit board test paste
(9) Test that there is no problem with the first piece of pasting, and carry out batch pasting
(10) Test after Pcb assembly. Test the circuit board online and offline to check whether the installation positions of components are consistent.
(11) reflow welding
(12) Power off
The above is the pcb welding process of automatic mounting machine in the pcb assembly process.
2. Storage of surface assembled smt components
Surface assembly components are generally ceramic packaging, metal packaging and plastic packaging. The first two kinds of packaging have good air tightness, no sealing problem, and the components can be stored for a long time. However, for the SMD products with plastic packaging, due to the poor air tightness of the plastic itself, special attention should be paid to the storage of the components assembled on the plastic surface.
Most of the IC components used in electronic products, their packaging are molded plastic packaging, because mass production is easy to reduce the cost. However, because plastic products have certain hygroscopicity, plastic components (SOJ, PLCC, QFP) belong to moisture sensitive components. Because the general reflow welding or wave soldering is instantaneous heating of the whole SMD, when the high heat in the welding process is applied to the plastic-sealed SMD shell with hygrosis, the thermal stress generated will cause cracks in the connection between the plastic-case and the pin, which will cause leakage and damp of the shell and slowly fail, and also loosen the pin, resulting in early failure.
smt component
1. Storage of surface assembly components for plastic packaging
Note that: The room temperature in the warehouse is lower than 40 ° C and the relative humidity is less than 60%, which are the environmental requirements of the storage site for surface assembled components of plastic packaging. Plastic packaging SMDS are packaged in a wet bag with desiccant when leaving the factory, and indicate that its anti-moisture effective for one year, not open when not in use.
2, plastic packaging surface assembly device opening use
Before opening the package, observe the humidity indicator card inside the package bag. When all black circles are blue, all SMDS are dry and safe to use. It is also safe when 10% and 20% of the circles turn pink; When 30% of the rings turn pink, it means that the SMD is at risk of hygroscopic, and that the desiccant has deteriorated. When all the rings turn pink, it indicates that all the SMDS are seriously hygroscopic. Before pasting, dry all the SMDS in the packaging bag.
3. Main process parameters of SMT glue and dispensing machine
In the dispensing process, the patch glue and the dispensing machine can change the main process parameters as follows:
(1) rheology of the patch adhesive. The rheological property (thixotropy) of the patch adhesive means that the viscosity decreases quickly at a high shear rate and can rise rapidly when the shear action stops. Good rheology ensures that the patch glue flows smoothly from the needle and forms a qualified glue spot on the PCB.
(2) The initial adhesive strength of the patch adhesive. The initial adhesive strength of the patch is the strength of the patch before curing. It should be sufficient to resist the shift strength of bonded components.
(3) glue point contour. The correct contours of glue point mainly have two kinds: peak shape (also known as triangle) and round head shape. The peak shape is formed by the patch with higher yield value, and the round head shape is formed by the patch with lower yield value. Compared with the peak shape, the circular point formed in the high speed dispensing process has more ideal bonding characteristics.
(4) glue point diameter. The glue point diameter GD is determined by NID of the needle and ND of the distance between the needle and PCB board.
Since the surface tension between the patch adhesive and PCB must be greater than the surface tension between the patch adhesive and the needle, which is determined by the diameter of the glue point GD and the NID of the needle, the following relationship is generally required between the two: GD > 2NID.
smt patch glue
(5) glue point height. The glue point height R should be at least greater than the pad height A and the SMC/SMD terminal metallization layer height B. The height and diameter of the glue point affect the bond strength. The ideal bond strength generally requires that the glue point can adhere to or touch more than 80% of the surface of the SMC/SMD binding area after mounting and extrusion. For this reason, R > 2A+B is generally taken.
(6) Wait/delay time. The waiting/delay time from the dispensing system to the dispensing signal to the release of the patch from the needle is different because of the type of patch glue, the structure, form and structural parameters of the syringe and needle, which should be selected and adjusted according to the actual situation, generally between tens to hundreds of milliseconds.
(7) Z-axis recovery height. Reasonable Z-axis recovery height should ensure that the dispensing head has the correct escape point "elastic off" effect, and should not be too high, so as not to waste time due to "empty stroke" and reduce the working frequency of dispensing. If the Z axis recovery height is not enough, the needle will drag the glue point when moving, resulting in wire drawing phenomenon.
(8) Time/pressure. The dispensing time/pressure value is set and adjusted according to the actual situation of dispensing equipment, patch glue and bonding object. It should be noted that, even if it is the same dispensing system and the same bonding object, when the amount of patch glue in the dispensing injection cylinder is different, the same time/pressure parameters will produce different dispensing effects.
In short, different SMC/SMD bonding has different process parameters, according to the type of SMC/SMD (shape, quality, etc.) to choose a reasonable dispensing thickness, number of glue points, direct glue point, direct dispensing machine nozzle, coating pressure and time, coating working temperature and other process parameters.