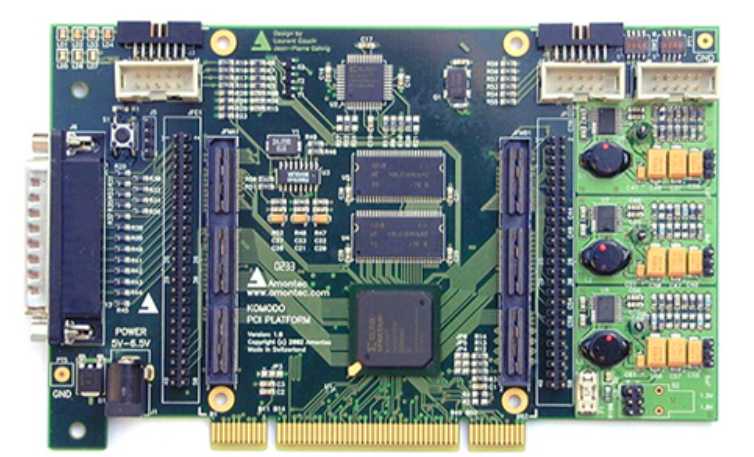
The cleaning process needs to consume energy, manpower and cleaning materials, especially the waste gas, waste water discharge and environmental pollution caused by cleaning materials, which has become a problem that must be paid attention to.
In recent years, the use of non-cleaning flux for welding has become the mainstream technology in most PCBA manufacturing enterprises. Unless it is to manufacture aerospace and aviation high-reliability and high-precision products, in the production process of PCB processing, clean free materials (mainly clean free flux) and clean free process are used, which makes a beneficial attempt to reduce production costs and protect the environment.
CFCS are usually used in the traditional cleaning process, and CFCS have a damaging effect on the ozone layer, so they are gradually banned. In this way, no - cleaning welding technology becomes the best way to solve this problem. For general electronic products, the use of no-cleaning flux and reduce residual dirt in the manufacturing process. For example, to keep the production environment clean, workers wear gloves to avoid contamination of components and circuit boards with oil and water vapor, and carefully adjust the process parameters of equipment and materials during welding, cleaning procedures can be eliminated and no-cleaning welding can be realized. However, for high-precision and high-reliability products, the above methods are not enough to realize no-cleaning welding, and further technical measures must be taken.
There are two technologies available to achieve clean free welding, one using a clean free flux with a low solid composition, the other welding in an inert gas or in reactive nitrogen. In fact, only the combination of no-wash flux and appropriate no-wash welding process and equipment can complete no-wash welding and realize no wash after welding.
Wave soldering or reflow welding is carried out in inert gas, so that the surface oxidation of solder and welding site on the SMT circuit board is controlled to a minimum, forming good solder wetting conditions, and then using a small amount of weak active flux can obtain satisfactory results. The commonly used inert gas welding equipment has two kinds: open and closed.
Open inert gas welding is suitable for wave soldering and reflow welding equipment with channel structure. Nitrogen is used to reduce the oxygen content in the channel, so as to reduce the degree of oxidation, improve the wettability of solder and improve the reliability of welding. But the disadvantage of open inert gas welding equipment is to use formic acid substance, will produce harmful gas; And its process is complex, the cost is high. The enclosed inert gas welding equipment also adopts the passageway structure, except that the inlet and outlet of the passageway are provided with a vacuum chamber. Before welding, put the PCB circuit board into the vacuum chamber, seal and vacuum, and then inject nitrogen. Repeat the operation of vacuuming and injecting nitrogen, so that the oxygen concentration in the chamber is less than 5×10-6mg/m3. Since the concentration of original oxygen in nitrogen is also less than 3×10-6mg/m3, the total oxygen concentration in the cavity is less than 8×10-6mg/m3. The circuit board is then passed through the preheating and heating zones. After welding, the circuit board is sent to the vacuum chamber at the exit of the channel. After closing the channel door, the circuit board is removed. In this way, the whole welding is carried out in a fully enclosed inert gas, which not only can obtain high quality welding, but also can realize no cleaning.
Enclosed inert gas welding can be used for wave soldering or infrared hot air reflow welding. Because of the welding in nitrogen, the oxidation of solder is reduced, the wetting time is shortened, the wetting ability is improved, the welding quality is improved and there is little spatter solder ball, and the circuit is very little pollution and oxidation. Because of the closed system, oxygen and nitrogen concentration can be controlled effectively. In closed inert gas welding equipment, wind velocity distribution and air supply structure are the key to achieve uniform heating.