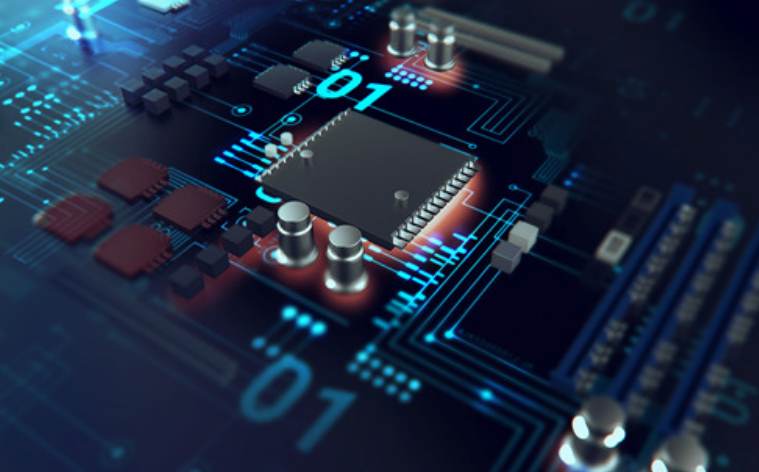
In the process of PCB processing, in addition to batch welding by reflow welding and wave soldering, manual welding is also needed to produce complete products.
Points to pay attention to when conducting PCBA manual welding:
1. The human body can generate more than 10,000 volts of static electricity, and the IC will be damaged when the voltage is more than 300 volts. Therefore, the static electricity of the human body needs to be discharged through the ground wire.
2. Wear gloves or finger covers for operation. Do not touch the board and component gold finger with bare hands.
3. Perform welding in the correct welding temperature, welding Angle, welding sequence, and maintain proper welding time.
4. Take the PCB board correctly: Hold the edge of the PCB when taking the PCB, and do not touch the components on the board.
5. Try to use low temperature welding: high temperature welding will accelerate the oxidation of the iron head, reduce the life of the iron head. If the temperature of the iron head exceeds 470℃. It oxidizes twice as fast as 380 ° C.
6. Do not put too much pressure on welding: do not put too much pressure on welding, otherwise the iron head will be damaged and deformed. As long as the iron head can fully contact the solder joint, heat can be transferred. (According to the size of the solder joint to choose different iron head, this can also make the iron head better heat transfer).
7. Do not knock or swing the solder tip: knock or swing the solder tip will cause damage to the heating core and tin beads splash, shorten the service life of the heating core, tin beads if splashed on the circuit board may form a short circuit, cause poor electrical performance.
8. Use a wet sponge to remove the oxide and excess tin residue of the iron tip. Clean sponge water content should be appropriate, water content can not only completely remove the solder chip on the iron head, but also because of the sharp decline in the temperature of the iron head (this thermal impact on the iron head and the heating element inside the iron, great damage) and welding leakage, welding and other poor, water sticking to the iron head to the circuit board will also cause corrosion and short circuit board. If the water is too little or not wet water treatment, it will make the iron head damaged, oxidation and lead to no tin, also easy to cause virtual welding and other poor welding. It is necessary to check the moisture content of the sponge frequently and clean the tin residue and other debris in the sponge at least three times a day.
9. The amount of tin and flux should be appropriate during welding. Too much solder, easy to cause tin or cover up welding defects, too little solder, not only low mechanical strength, but also due to the surface oxidation layer gradually deepened over time, easy to lead to solder joint failure. Too much flux will pollute and corrode PCB circuit board, which may lead to electrical defects such as leakage, and too little will not work.
10. Keep the tin on the iron head often: this can reduce the oxidation chance of the iron head and make the iron head more durable.
11. The incidence of flux spatter and solder ball is related to whether the soldering operation is skilled and the temperature of the iron head; Welding flux splash problem: when melting the solder wire directly with the soldering iron, the flux will quickly rise and splash. In welding, the method that the solder wire does not directly contact the soldering iron can reduce the flux splash.
12. When welding, pay attention not to make the electric iron hot the plastic insulation layer of the surrounding wire and the surface of the components, especially the products with compact welding structure and complex shape.
13. After welding, it is necessary to self-check:
(1) Whether there is missing welding.
(2) Whether the solder joint is smooth, full and glossy.
(3) Whether there is residual flux around the solder joint.
(4) There is no tin.
(5) Whether the welding pad falls off.
(6) There is no crack in the solder joint.
(7) Whether the solder joint is pointed.
14. During welding, it is also necessary to pay attention to some safety matters, wear a mask, and equip with ventilation equipment such as an extraction fan to keep the ventilation of the welding station.
In PCBA manual welding, pay attention to some basic precautions, can greatly improve the welding technology and product welding quality.