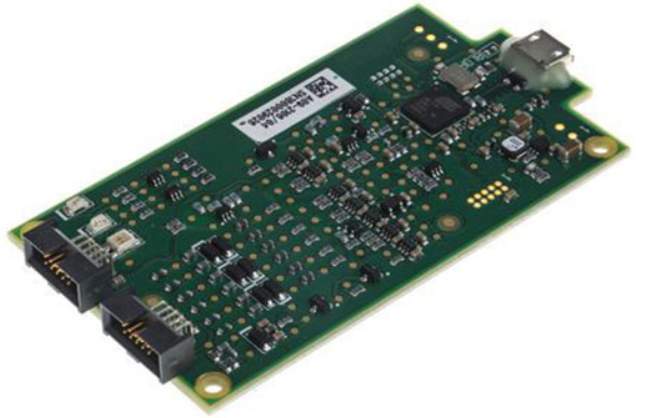
In PCBA manual welding processing, short circuit is a common poor processing, in order to achieve the same effect of manual welding and machine stickers, short circuit is a problem that must be solved. Short circuit is a common problem in PCBA processing. In the short-circuit problem, only timely and rapid solution to the problem, to ensure that the quality of the product function meets the requirements, the next Shenzhen PCBA processing manufacturer kingford for you to introduce a quick solution to the short-circuit problem of PCBA.
Quick solution to PCBA short circuit problem
1. Use the short-circuit positioning analyzer to check.
2. Light the short-circuit network on the PCB drawing, find the most tolerant place for short-circuiting on the circuit board, and pay attention to the IC internal short circuit.
3. If short circuit occurs in the same batch in SMT small batch processing, you can take a board for sectioning operation, and then energize each part separately to check the short circuit part.
4. Be careful when welding the capacitor on the surface of small size PCB, especially the power filter capacitor (103 or 104), which is in large quantity, it is easy to cause short circuit between the power supply and the ground.
5 Manual welding operation to form a good habit, use a multimeter to check whether the key circuit short circuit, each time after manual processing of an IC need to use a multimeter to measure whether the power supply and ground short circuit.
6. If there is a BGA chip, because all the solder joints are covered by the chip can not be seen, and it is a multilayer board (more than 4 layers), so it is best in the design of the power of each chip is divided, with magnetic beads or 0 ohmresistance connection, so that when there is a short circuit between the power supply and the ground, disconnect the magnetic bead detection, it is easy to locate a chip. The above is a quick solution to the PCBA short-circuit problem
2. Risks of PCBA OEM
PCBA OEM is that R & D enterprises to electronic processing plants to provide all the information needed for electronic processing, and then wait for the goods can be received, is a very convenient and worry free processing mode. After SMT patch proofing and processing, PCB plate-making, material procurement and other links are handed over to the SMT patch factory, those tedious links are eliminated, and the rest of our energy can be better focused on product research and development and market development. Everything has advantages and disadvantages. It seems that the processing mode is very convenient. There must be risks, so what risks are there?
PCBA OEM needs to know the risk
1. Maintenance risk
If PCBA OEM manufacturers do not have strong maintenance capabilities, it will lead to difficulties in product maintenance and prolong the maintenance cycle, which will eventually affect the product delivery time and cause considerable losses to customers.
2. Quality risk of materials
As PCBA OEM manufacturers are responsible for the overall production of electronic components and PCB boards, some profit-seeking electronic processing plants may buy some fake and shoddy materials in order to reduce production costs.
3. Procurement cycle risk
In the whole production cycle of electronic processing, material procurement is the most unstable, especially when the components used by customers are relatively scarce, not common supplies or the components are in great demand, and the OEM has no inventory and needs to order. At this time, uncontrollable factors will occur.
4. Capital risk
PCBA OEM mode requires the manufacturer to help the customer buy all the materials. The customer needs to pay an advance payment, usually 70% of the total payment, and then the manufacturer starts to purchase the materials and carry out the electronic processing and production process. Finally, the customer pays the remaining 30% when the product is shipped. Generally speaking, this is a good processing mode, but the customer needs to find a OEM with years of experience and strict quality control.
Why choose Shenzhen kingford?
1. Strength guarantee
▪SMT workshop: We have imported SMT machines and several sets of optical inspection equipment, with a daily output of 4 million. Each process is equipped with QC personnel, who can keep an eye on product quality.
▪DIP production line: We have two wave-soldering machines, among which there are more than 10 old employees who have worked for more than three years. The skilled workers can weld all kinds of plug-in materials.
2. Quality assurance, cost-effective
▪ High-end equipment can stick precision shaped parts, BGA, QFN, 0201 materials. Can also template patch, loose material hand.
▪ Sample and size batch can be produced, proofing from 800 yuan, batch 0.008 yuan/point, no start-up fee.
3. Rich experience in SMT and welding of electronic products, stable delivery
▪ Accumulated SMT SMT processing services for thousands of electronic enterprises, involving many kinds of automotive equipment and industrial control motherboard. The products are often exported to Europe and the United States, and the quality can be affirmed by new and old customers.
▪ On time delivery, normal 3-5 days after complete materials, small batch can also be expedited on the same day shipment.
4. Strong maintenance ability and perfect after-sales service
▪ Experienced maintenance engineers can repair all kinds of patch welding caused by bad products, to ensure the connection rate of each piece of circuit board.
▪ 24-hour customer service staff at any time response, the fastest speed to solve your order problems.