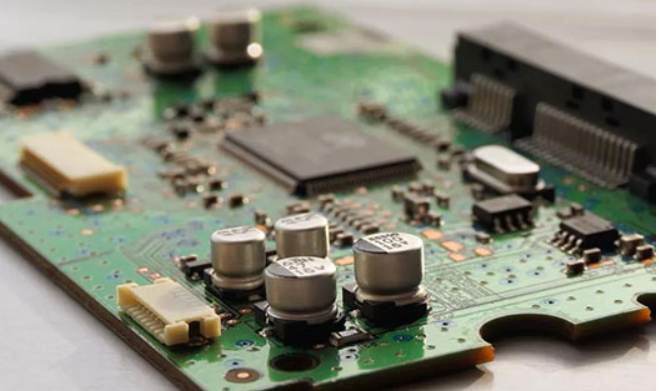
The three common ways for PCB board to deal with holes are through the window, through the hole cover oil and through the hole plug oil. Next, Shenzhen PCB board factory kingford will introduce the meaning of the hole plug oil in PCB board process.
The cause of plugging oil through the hole
Through the hole plug oil is to guide through the hole with ink inside the plug hole production, the emphasis is on the quality and tightness of the plug hole. Through the hole plug oil treatment inspection standard is or light, above must have ink cover, plugging. The second is the hole can not appear yellow phenomenon, and do not touch tin.
The process of through hole plug oil is an important supplement of through hole cover oil. Generally, high-quality PCB board will require through hole plug oil. Through the hole plug oil first through the hole plug on the ink, the plug hole can not be permeated by the hole, so that the ink on the welding resistance ring, will not flow into the hole, so as to achieve the effect of no yellow hole. The smaller the hole, the easier it is to plug. The hole of fortress oil is not too large, with a maximum of 0.5mm. Therefore, it is recommended to cover the hole oil for holes larger than 0.5mm.
The pores mentioned above are usually used for interlaminar conduction. Therefore, in order to avoid short circuit when the board is used, usually do cover oil, not only to ensure the electrical performance, but also to avoid the risk of short circuit with other components in the process of use. Therefore, if some PCB needs to pass the hole as a test point or heat dissipation, it will do the window.
2. Summary of serious causes of PCB board heating
In integrated circuits, excessive temperatures can negatively affect the function, components, and board itself. Next, Shenzhen PCBA processing manufacturer kingford to introduce the serious causes of PCB board fever?
PCB board heating serious cause
1. Component placement is incorrect
Some high-power devices need to reserve natural or forced ventilation for heat dissipation. Without proper airflow to dissipate heat, the PCB will accumulate most of the heat, resulting in a rise in temperature, which can lead to circuit performance degradation or damage. It should be noted that the sensitive element should not be placed near the heat element; By proper heat dissipation and natural or forced cooling, the temperature can be kept within a safe range.
2. Environmental and external thermal factors
When PCB is used in extreme temperature environment, if the temperature conditions of the target environment are not considered in the design, it may lead to excessive pressure on electronic components; Typically, electronic component manufacturers provide specifications for a specific temperature range.
3. Wrong parts and materials
Failure to follow recommended guidelines during the selection of materials for electronic components may result in heat dissipation problems. When selecting electronic components, it is important to look at detailed data and consider all relevant information related to power consumption, thermal resistance, temperature limitation, and cooling techniques. In addition, a quick power calculation is performed on the resistor to ensure that the appropriate power rating for the application is selected. Another problem is the PCB's dielectric material selection. The printed circuit board itself must be able to withstand the worst heat conditions.
4. PCB design and manufacturing defects
Poor layout and manufacturing process can lead to PCB heat dissipation problems. Improper welding may hinder heat dissipation, and insufficient wiring width or copper area may also lead to increased temperature. To prevent heat dissipation, designers must reduce heat dissipation and use other heat dissipation techniques when natural heat dissipation is insufficient. For thermal optimization design, attention should be paid to component specifications, PCB layout, PCB dielectric materials and environmental conditions.
kingford is a circuit board manufacturer specializing in the manufacture of printed circuit boards. It has been dedicated to the production of single, double-sided and multi-layer circuit boards for 20 years. Can provide impedance board, HDI board, blind hole plate and other multi-layer PCB board proofing, small batch production business.
PCB boardmaking ability
Energy production from 2 layers to 14 layers, 14-22 layers can be proofing production.
Minimum line width/spacing: 3mil/3milBGA Spacing :0.20MM
Minimum aperture: 0.1mm Size :610mmX1200mm
Ink: Tamura, Taiyo, Fudoken;
FR4: Shengyi, Kingboard, Harbour, Hongren, Guoji, Hezheng, Nanya,
(Shengyi S1130/S1141/S1170),Tg130℃/ Tg170℃ T g180℃ and other high TG plates)
High frequency plate: Rogers, Taconic, ARLLON;
Surface process: tin spray, lead-free tin spray, gold plating, full plate gold plating, plug gold plating, full plate thick gold, chemical tin (silver), anti-oxidation (OSP) blue glue, carbon oil