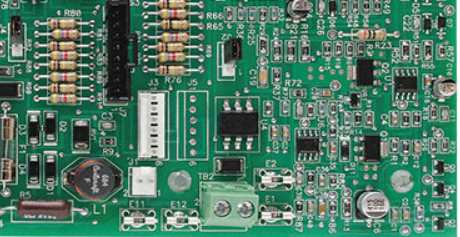
Usually PCB board can be shipped after the finished product inspection is OK, and then it can be packed in vacuum. Then how long is the shelf life of PCB board? Next, Shenzhen PCB Board factory -kingford will introduce to you.
PCB shelf life introduction
PCB board to vacuum packaging, which is a lot of circuit board manufacturers attach great importance to the problem. Because once the PCB board is not sealed well, its surface gold, tin spray and solder plate parts will be oxidized and affect welding, not conducive to production.
The circuit board is not like other products, it can not contact with air and water. First of all, the vacuum of PCB board can not be damaged. When packing, a layer of bubble film needs to be wrapped around the side of the box. The water absorption of bubble film is better, which plays a good role in moisture-proof. Then classify the emissions and label them.
After sealing the box must be separated from the wall, stored away from the ground in a dry ventilated place, but also avoid sunlight. The temperature of the warehouse is best controlled at 23±3℃, 55±10%RH, under such conditions, the surface treatment of gold, electric gold, tin spray, silver plating PCB board can be stored for 6 months, the surface treatment of silver, tin, OSP PCB board can be stored for 3 months. For the PCB board that is not used for a long time, the circuit board manufacturer had better brush a layer of three anti-paint on it. The role of three anti-paint can be moisture-proof, dustproof and anti-oxidation. This will increase the PCB board storage life to 9 months.
2. The PCBA processing plant selects the importance of SMT placing machine
Today's electronic products are pursuing personalization and miniaturization. The traditional piercing plug-in can not meet the market demand. SMT patch processing conform to the trend of The Times, to achieve non-porous patch, to achieve the miniaturization of electronic products.
In the PCBA processing plant, the important features of SMT mounters are accuracy, speed and adaptability. Adaptability is usually the ability of the patch machine to adapt to different installation requirements. Next, I will introduce the importance of PCBA processing plant to select a good SMT placing machine.
PCBA processing plant select the importance of SMT placement machine
I. Types of components that can be mounted
SMT machines with a wide range of component types have better adaptability than those that only use SMC or a small number of SMDS. The main factors that affect the type of parts installed on the patch machine are installation accuracy, installation tools, centering mechanism and part compatibility, and the number and type of feeders accommodated by the patch machine. Some mounters can only accommodate a limited number of feeders, while others can accommodate most or all types of feeders and can accommodate a large number of feeders. Obviously, the latter is more adaptable than the former. The feeding capacity of the SMT machine is usually expressed as the maximum number of 8mm braided feeds that can be installed on the SMT machine.
Two, the adjustment of the patch machine
When a patch machine is converted from assembling one type of PCB to assembling another type of PCB, it is necessary to reprogram the patch machine, change the feeder, adjust the PCB transmission mechanism and position the workbench, and adjust/replace the patch machine head. Program the patch machine. Two programming methods are commonly used in the patch machine: manual instruction programming and computer programming. Low-level installers usually use manual instructional programming, while advanced installers use computer programming.
Replacement of feeder. In order to reduce the time taken to change the feeder, the most common method is to use a "quick release" feeder, and the faster method is to change the feeder rack so that the feeder for each component on the PCB type is mounted on a separate feeder rack for easy replacement.
PCB transmission mechanism and positioning table adjustment. Adjust the width of the PCB positioning table and the conveying mechanism for conveying the PCB when the replacement PCB is different in size from the currently installed PCB. Automatic placement machine can be automatically adjusted under program control, low level placement machine can be manually adjusted.
Adjust and replace the sticker head. When the type of component to be installed on the PCB exceeds the mounting range of the sticker head, or when the PCB type is changed, the sticker head is usually replaced or adjusted. Most patch machines can be changed/adjusted automatically under program control, while lower level patch machines use manual replacement and adjustment.
Why do you choose kingford for SMT processing?
1. Strength guarantee
▪SMT workshop: We have imported SMT machines and several sets of optical inspection equipment, with a daily output of 4 million. Each process is equipped with QC personnel, who can keep an eye on product quality.
▪DIP production line: We have two wave-soldering machines, among which there are more than 10 old employees who have worked for more than three years. The skilled workers can weld all kinds of plug-in materials.
2. Quality assurance, cost-effective
▪ High-end equipment can stick precision shaped parts, BGA, QFN, 0201 materials. Can also template patch, loose material hand.
▪ Sample and size batch can be produced, proofing from 800 yuan, batch 0.008 yuan/point, no start-up fee.
3. Rich experience in SMT and welding of electronic products, stable delivery
▪ Accumulated SMT SMT processing services for thousands of electronic enterprises, involving many kinds of automotive equipment and industrial control motherboard. The products are often exported to Europe and the United States, and the quality can be affirmed by new and old customers.
▪ On time delivery, normal 3-5 days after complete materials, small batch can also be expedited on the same day shipment.
4. Strong maintenance ability and perfect after-sales service
▪ Experienced maintenance engineers can repair all kinds of patch welding caused by bad products, to ensure the connection rate of each piece of circuit board.
▪ 24-hour customer service staff at any time response, the fastest speed to solve your order problems.