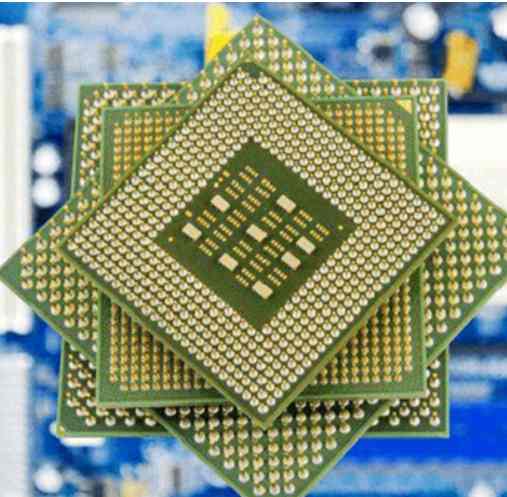
SMT chip processing quality and production efficiency for PCB circuit board is very key, SMT chip processing material is the brick of PCB circuit board, plays a vital role. During SMT process design and production lines, appropriate process materials must be selected according to process flow and process requirements. SMT patch processing materials include solder, solder paste, adhesive and other welding and patch materials, as well as flux, cleaning agent, heat transfer medium and other process materials. Here is to introduce the main role of assembly process materials.
The types and functions of SMT patch processing materials
(1) Solder and solder paste
Solder is an important structural material in surface assembly process. Different types of solder are used in different applications, which are used to join the metal surface of the object to be welded and form solder joints. Reflow welding is the use of solder paste, which is a welding material, and can use its viscosity to prefix SMC/SMD.
(2) flux
Flux is an important process material in surface assembly. It is one of the key factors affecting the quality of welding. It is needed in various welding processes. Its main role is to aid welding.
(3) binder
Binder is a bonding material in surface assembly. When the wave soldering process is adopted, the components are generally pasted and fixed on the PCB with adhesive. When PCB double-sided SMDS are assembled, even if reflow welding is adopted, the adhesive is often coated in the center of PCB pad pattern to strengthen the fixation of SMDS and prevent SMDS from shifting and falling during assembly operation.
(4) cleaning agent
Cleaning agent is used in surface assembly to clean the residue remaining on SMA after welding process. Under the present technical conditions, cleaning is still an indispensable part of the surface mounting process, and solvent cleaning is the most effective cleaning method.
SMT process materials are the basis of surface mounting process, and corresponding assembly process materials are selected for different assembly processes and processes. Sometimes in the same assembly process, the materials used will be different due to different subsequent processes or assembly methods.
2. How to do BGA repair in PCBA processing?
In PCBA processing, sometimes there will be some problems of poor BGA welding. If there is a problem in the welding of a BGA, the whole board will have problems, at this time, BGA repair is needed. Next, we will share how to do a good BGA repair in PCBA processing.
PCBA processing BGA repair four methods
First, formal assembly method (using ball tooling).
1. Place the clean and smooth BGA welding pad upward on the BGA support platform at the bottom of the ball tooling.
2. Prepare a small template matching the BGA pad, and the opening size of the template should be 0.05 ~ 0.1mm larger than the diameter of the welding ball; The small template is installed on the frame holding the template above the ball tooling, aligned with and fixed to the pad of the lower BGA device.
3. Place the BGA of printed paste flux or solder paste on the BGA support platform at the bottom of the ball tooling, and the printing face is upward.
4. Move the template to the top of the BGA (previously aligned position), skim the welding ball evenly on the template, shake the ball tooling, so that the template surface exactly in each hole to retain a welding ball, the excess welding ball from the template with a pair of pliers.
5. Remove the template
6. Check whether there is a lack of welding ball on each pad of the BGA device. If there is a tweezer, mend the welding ball.
Second, manually mount the solder ball.
1. Place the BGA device printed with paste flux or solder paste on the work table, with the shape of flux or solder paste facing upward.
2. Like SMT patch, paste the solder ball one by one on the paste flux or solder with tweezers or blotting pen.
Three, directly print the right amount of welding paste, through the re-flow welding to form the welding ball.
1. Increase the thickness of the template and slightly enlarge the opening size of the template when SMT machining the template.
2, printing solder paste.
3, flow welding. Due to the action of surface tension, the solder ball is formed after welding.
Four, flow welding
Repeat the flow welding as described in the BGA repair process in the previous section. When welding, the welding sphere of the BGA device is upward, the hot air volume is adjusted to the minimum, so as to prevent the welding ball from blowing out of position. After the reflow welding treatment, the welding ball is fixed on the BGA device. The reflow welding process of the ball can also be carried out in the reflow welding furnace. Install and weld Wells as soon as possible to prevent ball oxidation and damp components.
Among the above 4 ball placement methods, the positive installation method (using ball placement tooling) has the best effect; Inversion method (using ball equipment) is the method of BGA device packaging, because we purchased from the solder paste manufacturer of the solder ball size precision is poor, resulting in some small diameter of the solder ball can not be paste flux or solder paste live up; The efficiency of attaching solder ball by hand is relatively low. The most simple method is to directly print the star welding paste and form the welding ball through re-flow welding, but the density of the welding ball is not good and it is easy to produce holes.
Why choose kingfordSMT SMT processing?
1. Strength guarantee
▪SMT workshop: We have imported SMT machines and several sets of optical inspection equipment, with a daily output of 4 million. Each process is equipped with QC personnel, who can keep an eye on product quality.
▪DIP production line: We have two wave-soldering machines, among which there are more than 10 old employees who have worked for more than three years. The skilled workers can weld all kinds of plug-in materials.
2. Quality assurance, cost-effective
▪ High-end equipment can stick precision shaped parts, BGA, QFN, 0201 materials. Can also template patch, loose material hand.
▪ Sample and size batch can be produced, proofing from 800 yuan, batch 0.008 yuan/point, no start-up fee.
3. Rich experience in SMT and welding of electronic products, stable delivery
▪ Accumulated SMT SMT processing services for thousands of electronic enterprises, involving many kinds of automotive equipment and industrial control motherboard. The products are often exported to Europe and the United States, and the quality can be affirmed by new and old customers.
▪ On time delivery, normal 3-5 days after complete materials, small batch can also be expedited on the same day shipment.
4. Strong maintenance ability and perfect after-sales service
▪ Experienced maintenance engineers can repair all kinds of patch welding caused by bad products, to ensure the connection rate of each piece of circuit board.
▪ 24-hour customer service staff at any time response, the fastest speed to solve your order problems.