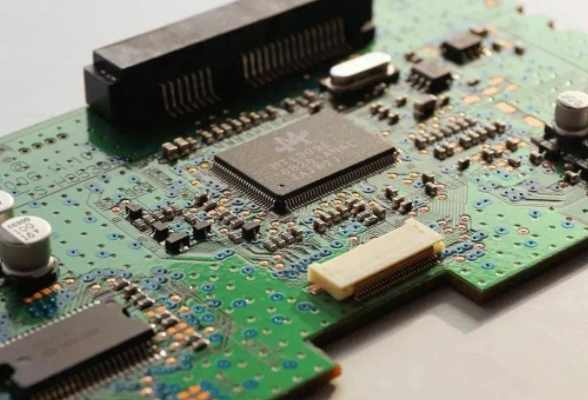
The traditional PCBA processing mode is mainly based on the non-communication of a single link, and there will be many problems in the corresponding factory cooperation. One of the most important factors is that it takes a long process to complete the whole cycle of manufacturing, and the corresponding factory switching and logistics transportation costs are very high. In addition, it does not apply to PCBA proofing orders. Therefore, the advantages of PCBA contract processing will come in handy, because it perfectly solves the problems faced by the traditional processing process.
kingford uses intelligent management software based on big data. Starting from the printed circuit board stage, Kingford covers the whole process of component procurement, PCBA assembly, testing, packaging and delivery, which reduces unnecessary expenditure in terms of time and cost, and at the same time, it can understand the situation of products in various links more clearly.
PCBA contract material processing advantage
I. PCB
It avoids many procedures of early review. It has its own PCB board factory, which has fast PCB manufacturing and short delivery time.
Two, small order
The advantage of one-stop service is that it eliminates the need to spend a lot of time searching for suppliers for small orders. A lot of suppliers do not want to spend more time and labor costs, and refuse or do not cooperate with the production. The PCBA contract factory model is to combine several small orders into a large quantity, can easily meet any order quantity.
3. Shorter PCBA processing cycle
Compared with traditional processes, PCBA processing and assembly cycles are much shorter because the transition from each process to the next process is seamless, so no time is lost. And ultimately, the delivery cycle is greatly shortened.
Fourth, supplier responsibility is more clear
There is no need to deal with more than one supplier, thus reducing the chance of misinformation, reducing the possibility of quality anomalies, and both parties have clearer responsibilities. It also reduces delays caused by a chain reaction caused by an exception from a single supplier.
5. Seamless link from client to manufacturing end
Product assembly, inventory and shipping at a glance. In addition to the logistical convenience of a single point of contact, it also saves time and is more conducive to accurate risk control.
Six, very suitable for small enterprises
The product design and market research of small entrepreneurial enterprises are not mature, and they may not be sure how much quantity they need, so they can only trial production in small batches. At the same time, small companies do not have so perfect staffing, but also need the quantitative flexibility provided by one-stop labor and materials contract.
2. Layout principles of PCB design components
In PCB design, component layout should follow certain principles. Only reasonable and scientific layout can design stable and reliable PCBA products. Next, Shenzhen PCB design company - Shenzhen Honglijie Electronics introduces PCB design component layout principles to you.
PCB design component layout principles
1. The components shall be arranged inside the PCB board, and each outlet foot of the components shall occupy a welding pad separately.
2, components can not occupy the entire PCB panel, the board around to leave a margin of 5~10mm, and the size of the PCB board area and fixed way determines the size of the margin around the board.
3. Components are required to be evenly distributed and uniformly spaced on the entire layout.
4. The installation height of components should be as low as possible. If it is too high, it is easy to fall or collide with adjacent components, so it may lead to poor safety performance of the system.
5, to determine the axial position of the larger components is the installation state of the printed circuit board in the system, the axis direction of the regular arrangement of components should be in the vertical direction of the system, so as to improve the stability of components on the PCB board.
6. The span at both ends of the components should be slightly larger than the axial length of the components. When bending the pin, do not bend at the root. Leave a distance of about 2mm to avoid damaging the components.
7. The layout of components cannot be crossed up and down, and a certain distance should be maintained between adjacent components and the spacing should not be too small.
Why kingford?
1. Strength guarantee
▪SMT workshop: We have imported SMT machines and several sets of optical inspection equipment, with a daily output of 4 million. Each process is equipped with QC personnel, who can keep an eye on product quality.
▪DIP production line: We have two wave-soldering machines, among which there are more than 10 old employees who have worked for more than three years. The skilled workers can weld all kinds of plug-in materials.
2. Quality assurance, cost-effective
▪ High-end equipment can stick precision shaped parts, BGA, QFN, 0201 materials. Can also template patch, loose material hand.
▪ Sample and size batch can be produced, proofing from 800 yuan, batch 0.008 yuan/point, no start-up fee.
3. Rich experience in SMT and welding of electronic products, stable delivery
▪ Accumulated SMT SMT processing services for thousands of electronic enterprises, involving many kinds of automotive equipment and industrial control motherboard. The products are often exported to Europe and the United States, and the quality can be affirmed by new and old customers.
▪ On time delivery, normal 3-5 days after complete materials, small batch can also be expedited on the same day shipment.
4. Strong maintenance ability and perfect after-sales service
▪ Experienced maintenance engineers can repair all kinds of patch welding caused by bad products, to ensure the connection rate of each piece of circuit board.
▪ 24-hour customer service staff at any time response, the fastest speed to solve your order problems.