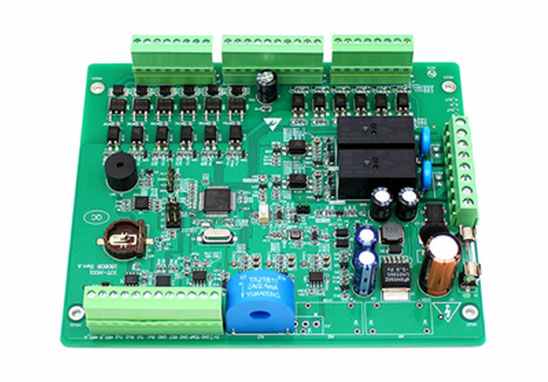
Circuit board to realize the function of running, relying on a bare PCB board is unable to complete, the bare board is required to mount components, plug-in and realize welding, this step by step process is called PCBA. Next, Shenzhen PCBA processing manufacturers will introduce the four links of PCBA processing technology.
In terms of technology, the process of PCBA can be roughly divided into four main links: SMT patch processing →DIP plug-in processing →PCBA testing → finished product assembly.
I. SMT patch processing link
SMT patch processing will purchase components according to BOM BOM provided by customers and confirm the PMC plan of production. After the preparatory work is completed, we will start SMT programming, manufacture laser steel mesh and solder paste printing according to the SMT process.
The components will be mounted on the circuit board through SMT mounter, and online AOI automatic optical detection will be carried out if necessary. After testing, the perfect reflow furnace temperature curve is set to let the circuit board flow through reflow welding.
After the necessary IPQC inspection, the plug-in material can then be passed through the circuit board using the DIP plug-in process and then through wave soldering. Then it is time to carry out the necessary post-furnace process.
After all the above processes are completed, QA will conduct a comprehensive test to ensure product quality.
2. DIP plug-in processing link
The process of DIP plug-in processing is: plug-in → wave welding → cutting foot → post-welding processing → washing plate → quality inspection
Iii. PCBA test
PCBA Test is the most critical quality control link in the whole PCBA processing process, which needs to strictly follow the PCBA test standards and test the test points of the circuit board in accordance with the customer's Test Plan.
PCBA test also includes 5 main forms: ICT test, FCT test, burn-in test, fatigue test and harsh environment test.
Iv. Assembly of finished products
The PCBA board that is tested OK will be assembled for the shell, then tested, and finally shipped.
The production of PCBA is one link after another. Any problem in any link will have a great impact on the overall quality, and each process needs to be strictly controlled.
The above is about the four main links of PCBA process production. Each major link is assisted by countless small links. Each small link will have one or some test processes to ensure product quality and avoid the discharge of unqualified products.
2. Where can we do small batch processing of SMT proofing?
kingford specializes in SMT proofing small batch processing services, including procurement of upstream electronic components to PCB production and processing, SMT patches, DIP plug-ins, PCBA testing, finished product assembly and other one-stop services.
SMT proofing small batch processing process
1. Single-side external assembly process: solder paste printing - patch - reflow welding.
2. Double-sided appearance assembly process: Side A printed solder paste - patch - reflow welding - flip plate - Side B printed solder paste - patch - reflow welding.
3. Single-side mixed assembly (SMD and THC on the same side) : solder paste printing -- patch -- reflow welding -- manual plug-in (THC) -- wave soldering.
4. Single-side mixed assembly (SMD and THC on both sides of PCB respectively) : B-side printing red glue -- patch -- red glue curing -- flip plate -- A-side plug-in -- B-side wave soldering.
5, double-sided mixed installation (THC on side A, A, B have SMD on both sides) : A5 side printing solder paste - patch - reflow welding - flip - side B printing red glue - patch - red glue curing - flip - side A plug-in - side B wave welding.
6, double-sided mixed assembly (A and B have SMD and THC on both sides) : Side A printing solder paste - patch - reflow welding - flip plate - Side B printing red glue - patch - red glue curing - flip plate - side A plug-in - side B wave welding - side B plug-in attached with computer and related products, communication products and consumer electronics.
Why do you choose kingford for PCBA processing?
1. Strength guarantee
▪SMT workshop: We have imported SMT machines and several sets of optical inspection equipment, with a daily output of 4 million. Each process is equipped with QC personnel, who can keep an eye on product quality.
▪DIP production line: We have two wave-soldering machines, among which there are more than 10 old employees who have worked for more than three years. The skilled workers can weld all kinds of plug-in materials.
2. Quality assurance, cost-effective
▪ High-end equipment can stick precision shaped parts, BGA, QFN, 0201 materials. Can also template patch, loose material hand.
▪ Sample and size batch can be produced, proofing from 800 yuan, batch 0.008 yuan/point, no start-up fee.
3. Rich experience in SMT and welding of electronic products, stable delivery
▪ Accumulated SMT SMT processing services for thousands of electronic enterprises, involving many kinds of automotive equipment and industrial control motherboard. The products are often exported to Europe and the United States, and the quality can be affirmed by new and old customers.
▪ On time delivery, normal 3-5 days after complete materials, small batch can also be expedited on the same day shipment.
4. Strong maintenance ability and perfect after-sales service
▪ Experienced maintenance engineers can repair all kinds of patch welding caused by bad products, to ensure the connection rate of each piece of circuit board.
▪ 24-hour customer service staff at any time response, the fastest speed to solve your order problems.