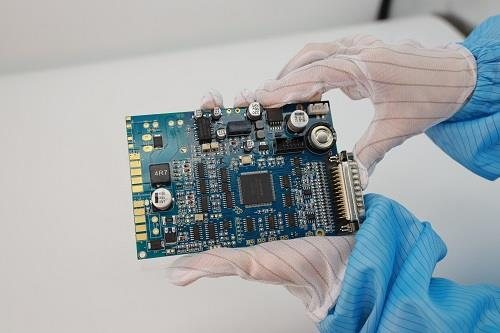
Shenzhen kingford is a professional manufacturer of printed circuit board manufacturing circuit board, for many years focused on single, double-sided, multi-layer circuit board production. Can provide impedance board, HDI board, blind hole plate and other multi-layer PCB board proofing, small batch production business. Next, we introduce the composition of PCB manufacturing cost.
PCB manufacturing cost composition
The production cost of PCB products refers to the total of direct materials, direct labor, direct labor and other direct or indirect costs actually consumed in the production process. In the production cost questionnaire of PCB enterprises, the percentages are generally as follows: equipment and maintenance account for 40%-43% of the total cost, material loss accounts for 19%-22%, and product repair and maintenance costs account for 17%-21%. Labor costs account for 15%-17% of PCBA's total costs, and other costs account for 2%.
As can be seen from the above, PCB production costs are mainly concentrated in equipment, maintenance costs, loss of raw materials and wastes, PCB production material costs and other fixed assets. Therefore, the production cost can be reduced from the above aspects. The production cost of PCB is generally divided into manufacturing cost and quality cost. Product manufacturing cost refers to the direct cost of direct materials, direct labor and so on actually consumed by enterprises in the process of producing products and providing services.
In PCB production, direct materials refer to electronic components, screen templates, welding materials, dispensing materials, cleaning materials, etc. Direct labor refers to wages, labor costs, bonuses, allowances, overtime pay, etc. Other manufacturing costs refer to all costs related to the manufacturing process except materials and labor, including various items consumed in the workshop, material costs used for machine and equipment maintenance, water, electricity, lighting, air conditioning costs, office expenses, etc.
Quality cost refers to the cost incurred by enterprises to ensure satisfactory quality and the loss caused by failure to obtain satisfactory quality. Among them, the prevention cost refers to the cost to prevent the occurrence of quality defects; Appraisal cost refers to the cost of testing and inspection in order to assess whether the product has the required quality; Internal defect cost refers to the loss caused by the product not reaching the stipulated quality requirements (the whole process) before leaving the factory. The cost of external defects refers to the loss caused by the failure of the product to meet the specified quality requirements after delivery. External quality assurance costs refer to the costs of providing objective evidence, demonstration and certification in order to meet the quality assurance requirements stipulated in the contract.
PCB manufacturing advantage
Energy production from 2 layers to 14 layers, 14-22 layers can be proofing production.
Minimum line width/spacing: 3mil/3milBGA Spacing :0.20MM
Minimum aperture: 0.1mm Size :610mmX1200mm
Ink: Tamura, Taiyo, Fudoken;
FR4: Shengyi, Kingboard, Harbour, Hongren, Guoji, Hezheng, Nanya,
(Shengyi S1130/S1141/S1170),Tg130℃/ Tg170℃ T g180℃ and other high TG plates)
High frequency plate: Rogers, Taconic, ARLLON;
Surface process: tin spray, lead-free tin spray, gold plating, full plate gold plating, plug gold plating, full plate thick gold, chemical tin (silver), anti-oxidation (OSP) blue glue, carbon oil
2. Manufacturing requirements of steel mesh processed by PCBA
Next, introduce the manufacturing requirements of steel mesh for PCBA processing.
1. Size of frame and steel mesh
Before PCBA processing, custom designed steel mesh is needed to make printing more perfect and suitable. The most important thing about steel mesh is the size and frame of steel mesh. The steel mesh adopts the stretching mode of AB glue and nylon gauze, and a layer of protective paint (S224) must be evenly scraped at the joint of the aluminum frame and glue. In order to ensure that the steel mesh has enough tension (stipulated to be greater than 35N/cm, the general requirement is 30~50N/cm) and good flatness, the distance between the steel mesh and the inner side of the frame is not less than 25mm, preferably in the range of 50-100mm. See Figure 1.
Manufacturing requirements of steel mesh for PCBA processing
The internal size of the frame is not the maximum size available for the steel mesh. The most useful maximum size for printing is the internal size of the frame, because the bonding area between the steel mesh and the inside of the frame, the bonding area between the steel mesh and the nylon mesh requires a certain distance from the printing area. Roll to 220 mm or larger. Of course, this also depends on the width of the press rail, the size of the wiping mechanism, and the size of the frame. For example, the DEK265 press has a frame size of 29"x29" and a maximum printing area of 510mmx489mm.
2. Tension
The tension of steel mesh refers to the tension of nylon mesh applied to the steel mesh, which can be measured by tension meter. The principle is to test the thrust required by the sinking unit distance of part of the net, in N/cm, as shown in Figure 2.
Manufacturing requirements of steel mesh for PCBA processing
In order to ensure the flatness of the steel mesh, there needs to be enough tension, which is generally greater than 35N/ cm, usually in the range of 30-50N/cm.
Three, hole wall shape and roughness
Ideally, the opening portion of the steel mesh should be inverted tapered, meaning that the dimensions below the opening are approximately 0.01 mm wider than the dimensions above (depending on the thickness of the steel mesh). As shown in Figure 3:
In the above cases, the opening of the steel mesh should be polished:
QFP, SOJ, PLCC, SOP, socket and CSP devices with spacing of 0.5mm or less, all printed steel mesh.
4. Dimensional tolerance
At present, the processing accuracy of electropolishing steel mesh of main domestic steel mesh manufacturers is as follows.
1. Opening dimension accuracy: 0-0.010mm.
2. Opening position accuracy: 0.005 ~ 0.03mm.
3. Net frame opening accuracy: within 2mm.
4. Material thickness: 0.030 ~ 0.600mm.
5. The center accuracy of the graph in the net frame: within 1mm.
6. Accuracy of material thickness: within 0.003.
7. Side wall (hole wall) roughness: 0.005 ~ 0.006mm.
Why choose Shenzhen kingford?
1. Strength guarantee
▪SMT workshop: We have imported SMT machines and several sets of optical inspection equipment, with a daily output of 4 million. Each process is equipped with QC personnel, who can keep an eye on product quality.
▪DIP production line: We have two wave-soldering machines, among which there are more than 10 old employees who have worked for more than three years. The skilled workers can weld all kinds of plug-in materials.
2. Quality assurance, cost-effective
▪ High-end equipment can stick precision shaped parts, BGA, QFN, 0201 materials. Can also template patch, loose material hand.
▪ Sample and size batch can be produced, proofing from 800 yuan, batch 0.008 yuan/point, no start-up fee.
3. Rich experience in SMT and welding of electronic products, stable delivery
▪ Accumulated SMT SMT processing services for thousands of electronic enterprises, involving many kinds of automotive equipment and industrial control motherboard. The products are often exported to Europe and the United States, and the quality can be affirmed by new and old customers.
▪ On time delivery, normal 3-5 days after complete materials, small batch can also be expedited on the same day shipment.
4. Strong maintenance ability and perfect after-sales service
▪ Experienced maintenance engineers can repair all kinds of patch welding caused by bad products, to ensure the connection rate of each piece of circuit board.
▪ 24-hour customer service staff at any time response, the fastest speed to solve your order problems.