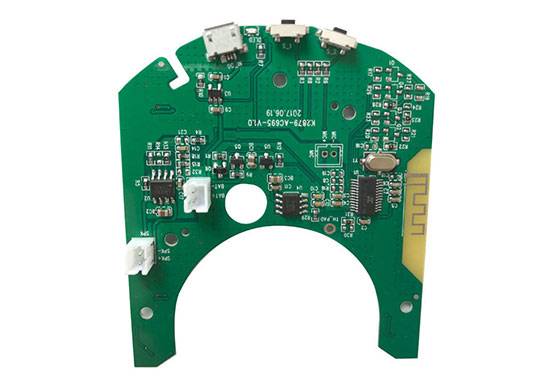
In the process of SMT patch processing, because the order quantity is very small, it is inevitable that there will be frequent line changing, material loading and material changing. Therefore, in this process, there must be a strict standardized process to avoid the occurrence of wrong material updating in the process of replacing the high frequency of lines and materials. Next, Shenzhen PCBA manufacturer kingford will introduce the SMT patch processing efficient refuelling process to you.
SMT patch processing efficient refueling process
1. Take out the feeder and the used paper plate.
2. SMT operators can take materials from the material rack according to their own station.
3. The operator checks the removed materials using the work number and position table to confirm whether the specifications and models are the same.
4. The operator checks the new pallet and the old pallet, and checks whether the specifications and models of the two pallets are exactly the same.
5. The operator checks its material to show whether the enterprise is consistent with the tray.
6. If there is any abnormality in the above inspection, the operator of the SMT machine shall immediately notify the delay processing.
7. Take samples from the new pallets and place the materials on an old and new pallet.
8. Take the newly installed Feida material, paste it on the refueling process record sheet, fill in the refueling working time, operator management and other relevant data information.
9. Install Feida back into the SMT placing machine according to the SMT placing machine station; You must perform a valid completion of your own supplementary information record.
10. Its operators notify engineering quality management personnel of material matching and testing, and must make material changes and inspections.
11. IPQC checks whether the data information can be developed correctly and whether the site can be correct according to the site number table.
12. The operation check of the above patch machine has been completed before the start of production.
The above 12 steps, as the standard process in the whole refueling process, must be strictly followed in the patch processing. Each step of the process must have the instruction manual of each position, only in this way can the wrong material change be avoided.
2. Common SMT polar component identification methods
Polar components need special attention in the entire PCBA processing process, because directional component errors will lead to batch accidents and the failure of the whole PCBA board, so it is very important for engineering and production personnel to understand SMT polar components.
First, SMT polar element definition
Polarity means that the positive and negative electrodes or first pins of a component are in the same direction as the positive and negative electrodes or first pins on the PCB(printed circuit board). If the component does not match the direction on the PCB, it is called bad reverse.
Second, SMT polar element identification method
1. The Resistor is non-polar
2. Capacitor
2.1 The ceramic capacitor is non-polar
2.2 The tantalum capacitor has polarity. PCB board and device positive electrode marking: 1) color band marking; 2) "+" mark; 3) Bevel mark.
2.3 Aluminum electrolytic capacitor has polarity. Part mark: color band represents negative; PCB board marking: color band or "+" symbol represents the positive terminal.
3. Inductor
3.1 There is no polarity requirement for the encapsulation of two welding ends such as chip coil
3.2 Multi-pin inductors have polarity requirements. Part mark: the dot/" 1 "represents the polarity point; PCB board marks: Dots/circles/" * "represent polarity points.
4. Light Emitting Diode
4.1 SMT table sticker LED has polarity. Parts negative electrode mark: green is negative electrode; PCB negative electrode marks :1) vertical bar,2) color band,3) silk screen Angle; 4) Silk-print "U" box on behalf.
5. Diode
5.1 SMT SMT two end diode has polarity. Parts negative electrode mark: 1) color band, 2) groove, 3) color mark (glass body); PCB negative labeling: 1) vertical bar labeling, 2) color belt labeling, 3) silk-screen sharp Angle labeling, 4) "U" box labeling
6. Integrated Circuit
6.1 SOIC Encapsulation has polarity. Polarity marks :1) ribbon,2) symbol, 3) notches, 4) hypotenuse
6.2 SOP or QFP encapsulation has polarity. Polarity marks: 1) Concave/notched marks, 2) one of the points is different from the other two/three points (size/shape).
6.3 QFN Encapsulation has polarity. Polarity marks :1) one point is different from the other two points (size/shape),2) hypotenuse mark, 3) symbol mark (bar/" + "sign/dot).
7. Ball Grid Array
7.1 Parts polarity: concave/notched mark/dot/circle mark; PCB board polarity: Circle/dot/letter "1 or A"/bevel mark. The polarity points of the parts correspond to the polarity points on the PCB.
Shenzhen kingford SMT processing capacity
1. Maximum board card: 310mm*410mm(SMT);
2. Maximum plate thickness: 3mm;
3. Minimum plate thickness: 0.5mm;
4. Minimum Chip parts: 0201 package or parts above 0.6mm*0.3mm;
5. Maximum weight of mounted parts: 150g;
6. Maximum parts height: 25mm;
7. Maximum parts size: 150mm*150mm;
8. Minimum spacing of pin parts: 0.3mm;
9. Minimum ball parts (BGA) spacing: 0.3mm;
10. Minimum ball parts (BGA) ball diameter: 0.3mm;
11. Maximum parts mounting accuracy (100QFP) : 25um@IPC;
12. Patch capacity: 3-4 million points/day.
Why do you choose kingford for SMT processing?
1. Strength guarantee
▪SMT workshop: We have imported SMT machines and several sets of optical inspection equipment, with a daily output of 4 million. Each process is equipped with QC personnel, who can keep an eye on product quality.
▪DIP production line: We have two wave-soldering machines, among which there are more than 10 old employees who have worked for more than three years. The skilled workers can weld all kinds of plug-in materials.
2. Quality assurance, cost-effective
▪ High-end equipment can stick precision shaped parts, BGA, QFN, 0201 materials. Can also template patch, loose material hand.
▪ Sample and size batch can be produced, proofing from 800 yuan, batch 0.008 yuan/point, no start-up fee.
3. Rich experience in SMT and welding of electronic products, stable delivery
▪ Accumulated SMT SMT processing services for thousands of electronic enterprises, involving many kinds of automotive equipment and industrial control motherboard. The products are often exported to Europe and the United States, and the quality can be affirmed by new and old customers.
▪ On time delivery, normal 3-5 days after complete materials, small batch can also be expedited on the same day shipment.
4. Strong maintenance ability and perfect after-sales service
▪ Experienced maintenance engineers can repair all kinds of patch welding caused by bad products, to ensure the connection rate of each piece of circuit board.
▪ 24-hour customer service staff at any time response, the fastest speed to solve your order problems.