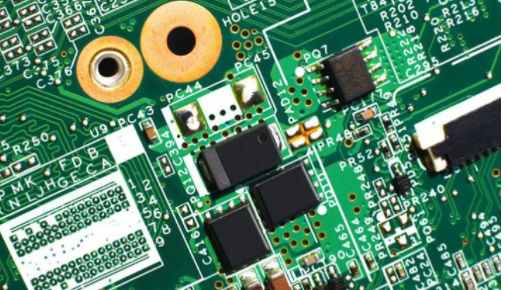
What is the minimum length of SMT patch proofing material braid? Generally, the materials for SMT patch sampling and trial production are short, which makes it difficult to feed the materials. A standard needs to be set. How much length of material braiding can SMT patch factory accept it? Next, Shenzhen kingford, SMT patch manufacturer, will introduce the minimum length requirements of SMT patch proofing material braid.
SMT patch proofing material braid minimum length requirements
In the process of SMT patch production, materials are mainly packed by pallets and braiding, which is convenient for the SMT machine to take materials and improve the efficiency of production. The braid is installed on Feida, and then for the placement machine to take material. In the process of SMT patch proofing, due to the relatively small quantity, the length of braiding will affect the material taking of the patch machine. In the actual SMT patch proofing process, the minimum length of braiding is 10cm, but this is not the industry standard, and the acceptable length of each factory is different, which depends on the quality of the patch machine and Feida, as well as the degree of material loss. If permitted, we will try our best to ask the customer to provide more materials to ensure safe production.
kingford SMT patch sampling and trial production: different types of feeders are different, which is too short and time-consuming. The key is to explain to the customer in advance, so that he can decide whether he is willing to buy more materials, or whether he is willing to extend the construction period and pay more processing fees. The minimum standard set by our company is 10cm
Packaging materials as long as Feida can jam on the line, the general 10cm material belt can be. But there's no harm in preparing a little extra, given the potential for defects such as throwing material. After all, the materials of 0603 are not very expensive, and preparing a little more is only one or two yuan more.
2.PCBA manufacturer briefly describes the refuelling process of SMT patches
In the process of SMT patch processing and proofing, because the order quantity is very small, it is inevitable that there will be frequent line changing, material loading and material changing. Therefore, in this process, there must be a strict standardized process to avoid the occurrence of wrong material updating in the process of replacing the high frequency of lines and materials. Next, Shenzhen PCBA manufacturer kingford will introduce the SMT refuelling process.
SMT patch refueling process
1. Take out the feeder and the used paper plate.
2. SMT operators can take materials from the material rack according to their own station.
3. The operator checks the removed materials with the work number and position table to confirm whether the specifications and models are the same.
4. The operator checks the new pallet and the old pallet, and checks whether the specifications and models of the two pallets are exactly the same.
5, the operator to check its material can indicate whether the enterprise is consistent with the tray.
6. If there is any abnormality in the above inspection, the operator of the SMT machine shall immediately notify the delay processing.
7. Take a sample from the new pallet, and then park the material on a new and old pallet.
8. Take the newly installed Feida material, paste it on the refueling process record sheet, fill in the refueling working time, operator management and other relevant data information.
9. Install Feida back to the SMT placement machine according to the SMT placement machine station; You must perform a valid completion of your own supplementary information record.
10. Its operators notify engineering quality management personnel of material matching and testing, and must make material changes and inspections.
11. IPQC checks whether the data information can be developed correctly and whether the site can be correct according to the site numbering table.
12. The operation check of the above patch machine has been completed before the start of production.
The above 12 steps, as the standard process in the whole refueling process, must be strictly followed in the patch processing. Each step of the process must have the instruction manual of each position, only in this way can the wrong material change be avoided.
SMT patch processing capability
1. Maximum board card: 310mm*410mm(SMT);
2. Maximum plate thickness: 3mm;
3. Minimum plate thickness: 0.5mm;
4. Minimum Chip parts: 0201 package or parts above 0.6mm*0.3mm;
5. Maximum weight of mounted parts: 150g;
6. Maximum parts height: 25mm;
7. Maximum parts size: 150mm*150mm;
8. Minimum spacing of pin parts: 0.3mm;
9. Minimum ball parts (BGA) spacing: 0.3mm;
10. Minimum ball parts (BGA) ball diameter: 0.3mm;
11. Maximum parts mounting accuracy (100QFP) : 25um@IPC;
12. Patch capacity: 3-4 million points/day
Why choose Shenzhen kingford?
1. Strength guarantee
▪SMT workshop: We have imported SMT machines and several sets of optical inspection equipment, with a daily output of 4 million. Each process is equipped with QC personnel, who can keep an eye on product quality.
▪DIP production line: We have two wave-soldering machines, among which there are more than 10 old employees who have worked for more than three years. The skilled workers can weld all kinds of plug-in materials.
2. Quality assurance, cost-effective
▪ High-end equipment can stick precision shaped parts, BGA, QFN, 0201 materials. Can also template patch, loose material hand.
▪ Sample and size batch can be produced, proofing from 800 yuan, batch 0.008 yuan/point, no start-up fee.
3. Rich experience in SMT and welding of electronic products, stable delivery
▪ Accumulated SMT SMT processing services for thousands of electronic enterprises, involving many kinds of automotive equipment and industrial control motherboard. The products are often exported to Europe and the United States, and the quality can be affirmed by new and old customers.
▪ On time delivery, normal 3-5 days after complete materials, small batch can also be expedited on the same day shipment.
4. Strong maintenance ability and perfect after-sales service
▪ Experienced maintenance engineers can repair all kinds of patch welding caused by bad products, to ensure the connection rate of each piece of circuit board.
▪ 24-hour customer service staff at any time response, the fastest speed to solve your order problems.