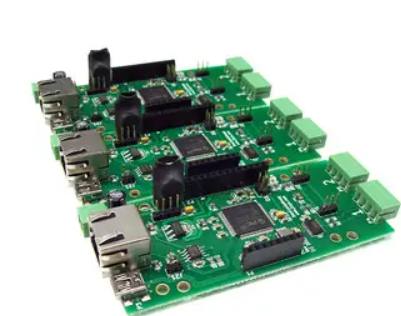
In PCBA processing, 01005 is not only the problem of high precision, but also the processing price is much more expensive than other specifications. Why is the mounting cost of 01005 so high in SMT processing? Next, Shenzhen PCBA processing manufacturer -kingford will introduce what is 01005 process and the reason why 01005 process is expensive in PCBA processing.
What is the 01005 process?
01005 is a number concept that many people don't understand. What does 01005 mean in SMT? We all know that high-end equipment requires high precision technology. Similar to the mobile phone circuit board has a lot of 01005 components. The 01005 component poses a challenge to all mature processes during SMT welding assembly, because its size is only 0.22mm*0.4mm, which is almost impossible for our normal visual performance, and its weight is light (0.04mg). Understanding these features will make it easier to understand the assembly process involved, and more importantly, the layout of the materials and pcb boards will have to be redesigned in order to use the 01005 component.
Once the pcb is completed, the printing of solder paste is a crucial step. The quantity and quality of solder paste will directly affect the performance and beauty of the entire circuit board. Picking up components correctly and stably is the key link of the whole smooth mounting process.
Why is 01005 process expensive in PCBA processing?
Take a typical customer case. This customer is engaged in medical electronics. The previous products are biased towards stability and use traditional components. He is cautious and cautious about components of 01005 specification.
Later, due to the upgrading of the product, the precision and volume of the medical surgical robot were optimized and improved. Therefore, 01005 specification components must be used. In the quotation stage, the customer still expected to look for PCBA processing suppliers according to the target price of 0603. Later, after a round of inquiry, it was found that no one was willing to accept the order at a loss. Finally, he had to raise his target price.
Normally, 01005 itself is also used for the design of high precision and high added value of products, because the process difficulty of using 01005 components is relatively high, the packaging precision is high, the process is complex, not only the processing cost is high, but also the price itself is not cheap. In addition, there are several other items that will lead to the high price of the entire product.
1. The pin spacing of PCB: 01005 original is very close, which leads to the improvement of the processing precision of pcb pad, and the requirements of the process are more complex.
2, solder paste: need relatively high quality solder paste, to control the rate of climbing tin and welding quality.
3. Steel mesh: Because of the problem of pin spacing, the process window is very narrow, and the stability is relatively poor. There will be great requirements for the opening and material of steel mesh.
4. Nitrogen: In order to ensure the welding effect, nitrogen reflow furnace is generally used for welding in 01005, which has higher requirements for equipment and will increase the expenditure of equipment.
For the product 01005, it is mainly small and high-tech. Therefore, when setting 01005 process parameters in SMT processing plant, SPI, AOI, X-ray and other testing equipment must be strictly adopted to optimize process parameters and assist processing.
2.SMT manufacturers analyzed the causes of welding/weld holes in SMT processing
Shenzhen kingford has its own SMT plant, which can provide SMT SMT processing services of 0201 components with minimum package, supporting incoming material and sample processing and PCBA OEM. Next, we will introduce the causes of welding/weld holes in SMT processing.
Standard for hole control of SMT patch machining welds/welds
At present, the hole control standard for welding/weld is generally implemented in accordance with IPC-A-610 standard. The section diameter of hole welding for SMT patch processing should be less than or equal to 25% of the diameter of the welding ball. After conversion according to the formula, the hole on the section of the welding ball is 6%. If there is more than one void, then all the areas are added up to assess whether they exceed the specification of this standard.
Cause analysis and measure of weld hole in SMT patch processing
After years of experience summary and scientific research verification of SMT processing plants, there is no evidence that the holes in single solder joints will cause the failure of solder joints. However, in many cases, the holes located in the section of solder pads are a huge potential quality hazard, whose quality has a much greater impact on reliability, and eventually lead to weld cracking and failure.
The bottom line is that the size of the void is more important than the location of the void.
Then in the process of circuit board production, according to the customer's product and process requirements, the corresponding optimization and improvement, the most important is through solder paste, reflow temperature control and other aspects to avoid the location of the main weld hole, and the size and number of holes should also be controlled accordingly.
For core devices such as QFN, the packaging is unique and the process is difficult. The coating on the side of the welding end is exposed and without welding. Generally speaking, the left and right sides of the welding end have very poor weldability in smt processing, which is prone to poor wetting, bridge and cavity. In this case, the main reason is that thin solder paste is easier to form a larger hole, the main reason is that the thickness of the weld gap is too small, resulting in the volatiles of the welding machine more difficult to discharge through the "channel", so that the "hole" problem occurs.
Therefore, the occurrence of related problems may not only be the cause of one point, but also the result of comprehensive factors.
Shenzhen kingford PCBA processing advantages
1. Strength guarantee
▪SMT workshop: We have imported SMT machines and several sets of optical inspection equipment, with a daily output of 4 million. Each process is equipped with QC personnel, who can keep an eye on product quality.
▪DIP production line: We have two wave-soldering machines, among which there are more than 10 old employees who have worked for more than three years. The skilled workers can weld all kinds of plug-in materials.
2. Quality assurance, cost-effective
▪ High-end equipment can stick precision shaped parts, BGA, QFN, 0201 materials. Can also template patch, loose material hand.
▪ Sample and size batch can be produced, proofing from 800 yuan, batch 0.008 yuan/point, no start-up fee.
3. Rich experience in SMT and welding of electronic products, stable delivery
▪ Accumulated SMT SMT processing services for thousands of electronic enterprises, involving many kinds of automotive equipment and industrial control motherboard. The products are often exported to Europe and the United States, and the quality can be affirmed by new and old customers.
▪ On time delivery, normal 3-5 days after complete materials, small batch can also be expedited on the same day shipment.
4. Strong maintenance ability and perfect after-sales service
▪ Experienced maintenance engineers can repair all kinds of patch welding caused by bad products, to ensure the connection rate of each piece of circuit board.
▪ 24-hour customer service staff at any time response, the fastest speed to solve your order problems.