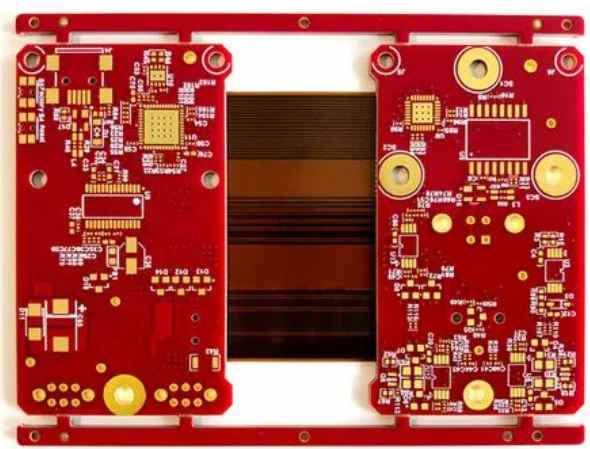
Many SMT factories often encounter some poor quality during production. Shenzhen kingford, as a professional third-party SMT processing factory, summarizes some packaging and problems that are most likely to occur in SMT processing (according to the difficulty) :
(1) QFN: The most common adverse phenomena are bridge connection and virtual welding (open welding).
(2) Dense foot components: such as SOP QFP below 0.65mm, the most likely adverse phenomenon is bridge connection, virtual welding (open welding).
(3) Large spacing and large size BGA: the most likely adverse phenomenon is solder joint stress fracture.
(4) Small spacing BGA: the most likely adverse phenomenon is bridge, virtual welding (open welding).
(5) long fine spacing table stick connector: the most likely adverse phenomenon is bridge, virtual welding (open welding).
(6) Micro switch, socket: the most likely adverse phenomenon is the internal rosin.
The main causes of common problems are:
(1) The bridge connection of micro-spacing components is mainly caused by poor printing of welding paste.
(2) The solder joint cracking of large size BGA is mainly caused by moisture.
(3) The bridge and virtual welding of small spacing BGA are mainly caused by poor printing of welding paste.
(4) The opening welding of transformer and other components is mainly caused by the poor coplane of the pin of the components.
(5) long fine distance table stick connector bridge and open welding, largely because PCB welding deformation and socket layout direction is not.
(6) The internal rosin into the micro switch and socket is mainly caused by the capillary effect formed by the structural design of these components.
2. Possible influence of reflow welding on SMT machining quality
Reflow welding is a processing technique widely used in the electronics manufacturing industry to weld electronic components onto printed circuit boards (PCB). Reflow welding is widely used in SMT (surface mount technology) because of its higher production efficiency and higher welding quality compared with traditional manual welding. However, reflow soldering may have some effects on SMT machining quality, which will be analyzed below.
1. PCB deformation caused by temperature gradient
In reflow soldering process, PCB is exposed to high temperature environment, so as to melt the solder between the solder spot and PCB, forming a solid solder spot. However, due to the large temperature gradient in reflow processing, that is, the temperature changes in different areas of the PCB are large, which may cause deformation of the PCB. Once the PCB is deformed, the connection between the welded points and the PCB may become loose or broken, thus affecting the reliability of the product.
To mitigate this effect, manufacturers usually use various methods to improve the thermal stability of PCBS, such as increasing the thickness of the PCB, changing the PCB material, or using multiple layers of PCB.
2. Component damage caused by temperature gradient
Components used in SMT machining are usually very small electronic components, which are very sensitive to temperature changes. Due to the large temperature gradient in reflow welding process, if appropriate measures are not taken, the components may be damaged. For example, if a component is placed in a high temperature area of a PCB, it may cause the plastic casing of the component to melt, thus damaging the internal circuit of the component.
To mitigate this, manufacturers often take various measures, such as placing components in cooler areas or using components that are more resistant to high temperatures.
3. Oxidation in reflow welding process
During reflow processing, the soldering agent may be oxidized to form metal oxides, which may cause the connection between the solder joint and the PCB to loosen or break. In addition, the reliability of the solder joints may be affected due to the presence of oxidation, thereby reducing the quality of the overall product.
Shenzhen kingford is a professional PCBA OEM manufacturer, which can provide one-stop services from upstream electronic components procurement to PCB production and processing, SMT patches, DIP plug-ins, PCBA testing, finished product assembly, etc.
Why choose Shenzhen kingford?
1. Strength guarantee
- SMT workshop: With imported SMT machines, multiple sets of optical inspection equipment, the daily production can be 4 million. Each process is equipped with QC personnel, who can keep an eye on product quality.
DIP production line: there are two wave soldering, among which there are more than 10 veteran employees who have worked for more than three years. The workers have high proficiency and can weld all kinds of plug-in materials.
2. Quality assurance, cost-effective
- High-end equipment can stick precision shaped parts, BGA, QFN, 0201 materials. Can also template patch, loose material hand.
- Sample and size batch can be produced, proofing starting from 800 yuan, batch 0.008 yuan/point, no start-up fee.
3. Rich experience in SMT and welding of electronic products, stable delivery
- Accumulated services for thousands of electronic enterprises, involving SMT processing services for various types of automotive equipment and industrial control motherboard, products are often exported to Europe and America, quality can be affirmed by new and old customers.
- Delivery on time, normal 3-5 days after complete materials, small batch can also be expedited day shipment.
4. Strong maintenance ability and perfect after-sales service
- Experienced maintenance engineer, can repair all kinds of patch welding caused by defective products, can ensure the connection rate of each circuit board.
- 24 hours customer service staff response at any time, the fastest speed to solve your order problems.