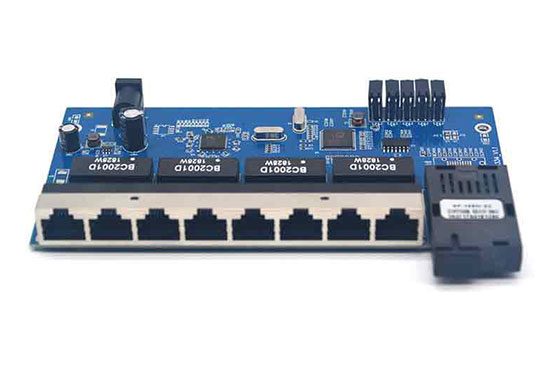
Viscosity and surface tension are important properties of PCBA solder, good PCBA solder melting should have low viscosity and surface tension. Whether reflow soldering, wave soldering or hand welding, surface tension is a disadvantage to forming a good solder joint. Next, Shenzhen PCBA manufacturer kingford introduces how to reduce the surface tension and viscosity in PCBA welding processing.
First, change the surface tension and viscosity measures
Viscosity and surface tension are important properties of PCBA solder. Good PCBA solder should have low viscosity and surface tension when melting. Surface tension is the nature of matter, can not be eliminated, but can be changed.
The main measures to reduce surface tension and viscosity in PCBA welding processing are as follows:
① Raise the temperature. Increasing the temperature can increase the molecular distance in the molten PCBA solder and reduce the gravitational attraction of the molecules in the liquid PCBA solder to the surface molecules. So heating can reduce viscosity and surface tension.
② Adjust the proportion of metal alloys. The surface tension of Sn is very high, and the addition of Pb can reduce the surface tension. As can be seen from the figure, when the content of lead in Sn-PbPCBA solder is increased, the surface tension decreases obviously when the content of Pb reaches 37%.
When the content of Pb in Sn-PbPCBA solder is increased, the surface tension decreases obviously when the content of Pb reaches 37%
③ Add active agent. This can effectively reduce the surface tension of PCBA solder, but also can remove the surface oxidation layer of PCBA solder.
(4) Improve the PCBA welding processing environment. Nitrogen protected PCBA welding process or vacuum PCBA welding process can reduce high temperature oxidation and improve wettability.
2. The role of surface tension in PCBA welding processing
Surface tension is in the opposite direction of wetting force, so surface tension is one of the factors unfavorable to wetting.
Whether reflow soldering, wave soldering or hand welding, surface tension is a disadvantage to forming a good solder joint. But the surface tension can be used in SMT reflow welding.
When the solder paste reaches the melting temperature, Self Alignment effect occurs under the action of balanced surface tension. In other words, when the component placement position deviates slightly, the component can be automatically pulled back to the approximate target position under the action of surface tension.
Therefore, the surface tension makes the reflow process more relaxed in the requirements of mounting accuracy, and it is easier to achieve high automation and high speed.
Meanwhile, due to the characteristics of "re-flow" and "self-positioning effect", SMT reflow welding process has stricter requirements for pad design, component standardization and other aspects.
If the surface tension is not balanced, even if the mounting position is very accurate, PCBA welding processing defects such as component position deviation, monument, bridge will appear after PCBA welding.
During wave soldering, due to the size and height of the SMC/SMD component itself, or because the high component blocks the high component and blocks the oncoming tin wave flow, and is affected by the surface tension of the tin wave flow caused by shadow effect, the formation of liquid PCBA solder on the back of the component body can not be infiltrated into the flow block area, resulting in leakage welding.
SMT patch processing capability
1. Maximum board card: 310mm*410mm(SMT);
2. Maximum plate thickness: 3mm;
3. Minimum plate thickness: 0.5mm;
4. Minimum Chip parts: 0201 package or parts above 0.6mm*0.3mm;
5. Maximum weight of mounted parts: 150g;
6. Maximum parts height: 25mm;
7. Maximum parts size: 150mm*150mm;
8. Minimum spacing of pin parts: 0.3mm;
9. Minimum ball parts (BGA) spacing: 0.3mm;
10. Minimum ball parts (BGA) ball diameter: 0.3mm;
11. Maximum parts mounting accuracy (100QFP) : 25um@IPC;
12. Patch capacity: 3-4 million points/day.
Why choose Shenzhen kingford?
1. Strength guarantee
▪SMT workshop: We have imported SMT machines and several sets of optical inspection equipment, with a daily output of 4 million. Each process is equipped with QC personnel, who can keep an eye on product quality.
▪DIP production line: We have two wave-soldering machines, among which there are more than 10 old employees who have worked for more than three years. The skilled workers can weld all kinds of plug-in materials.
2. Quality assurance, cost-effective
▪ High-end equipment can stick precision shaped parts, BGA, QFN, 0201 materials. Can also template patch, loose material hand.
▪ Sample and size batch can be produced, proofing from 800 yuan, batch 0.008 yuan/point, no start-up fee.
3. Rich experience in SMT and welding of electronic products, stable delivery
▪ Accumulated SMT SMT processing services for thousands of electronic enterprises, involving many kinds of automotive equipment and industrial control motherboard. The products are often exported to Europe and the United States, and the quality can be affirmed by new and old customers.
▪ On time delivery, normal 3-5 days after complete materials, small batch can also be expedited on the same day shipment.
4. Strong maintenance ability and perfect after-sales service
▪ Experienced maintenance engineers can repair all kinds of patch welding caused by bad products, to ensure the connection rate of each piece of circuit board.
▪ 24-hour customer service staff at any time response, the fastest speed to solve your order problems.