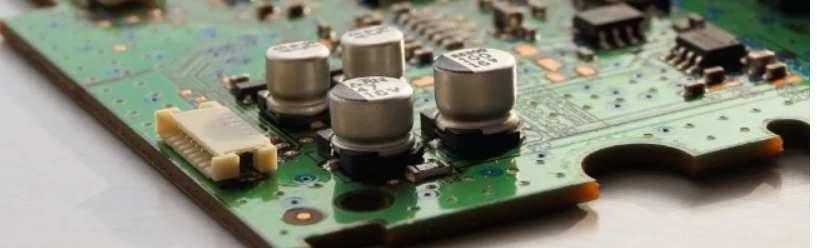
Shenzhen kingford is a professional PCB design company with an average PCB design team of more than 10 years of experience, which can provide multi-layer, high density, high speed PCB routing design and PCB design proofing services. Next, introduce the basic requirements of BGA pad design.
Basic requirements of BGA pad design
1. The center of the pad of each welding ball on PCB is consistent with the center of the corresponding welding ball at the bottom of BGA.
2, PCB pad graphics is solid circle, the through hole can not be processed on the pad.
3, the through hole in the hole after electroplating, must use dielectric material or conductive glue to plug, the height shall not exceed the height of the pad.
4. Usually, the diameter of the pad is less than 20% ~ 25% of the diameter of the ball. The larger the pad is, the smaller the wiring space between the two pads is.
5. The number of wiring between two pads is calculated as p-d ≥(2N+I). In the Xr formula, P is the spacing of the welding ball; D is the diameter of the pad; N is the number of wiring; X is the line width.
6. General rule: The diameter of the pad of PBGA is the same as that of the pad on the device substrate.
7. The wire width connected with the pad should be the same, generally 0.15 ~ 02mm.
8, resistance welding size is greater than bonding pad feet す 0.1 ~ 0.15 mm.
9. The welding pad design of CBGA shall ensure that the opening of the template makes the printing amount of the welding paste greater than or equal to 0.08mm2(this is the minimum requirement) in order to ensure the reliability of the solder joints after PCBA processing products. Therefore, the pad of CBGA is larger than that of PBGA.
10. Set the positioning line of the outer frame.
Setting up the external positioning line is important for post-SMT inspection. The size of the positioning frame is the same as that of the chip shape. The line width is 0.2-0.25mm. The 45° chamfer indicates the chip direction. The positioning line of the outer frame has two kinds of silk screen and copper. The former generates errors. The latter is more accurate. In addition, 2 Mark points should be set outside the positioning frame.
2.PCBA manufacturer detailed the advantages of SMT patch processing technology
Shenzhen kingford is a professional PCBA manufacturer with its own PCB board factory and SMT patch processing factory. We can provide PCB design, PCB board making, component purchasing, SMT patch, DIP plug-in, PCBA testing, finished product assembly and other one-stop PCBA processing services. Next, we will introduce the advantages of SMT patch processing technology.
Advantages of SMT patch processing technology
First, high reliability, strong anti-vibration ability
SMT patch processing adopts flake components, with high reliability, small and light components, so strong vibration resistance, automatic production, high mounting reliability, generally bad solder joint rate is less than 10 parts per million, one order of magnitude lower than through hole insertion components wave welding technology, can ensure that electronic products or components solder joint defect rate is low, SMT is now used in almost 90% of electronic products.
Two, electronic products small size, high assembly density
SMT patch components volume is only about 1/10 of the traditional plug-in components, and the weight is only 10% of the traditional plug-in components, usually using SMT technology can reduce the size of electronic products by 40%~60%, 60%~80% quality reduction, the area and weight are greatly reduced. The SMT patch processing and assembly component grid has been developed from 1.27MM to 0.63MM grid at present, and the individual is up to 0.5MM grid. The through hole installation technology is used to install components, which can make the assembly density higher.
Three, high frequency characteristics, reliable performance
Because the chip components are firmly mounted, the devices are usually leadless or short leads, which reduces the influence of parasitic inductance and parasitic capacitance, improves the high frequency characteristics of the circuit, and reduces electromagnetic and radio frequency interference. The maximum frequency of the SMC and SMD circuits is 3GHz, while the chip components are only 500MHz, which can shorten the transmission delay time. It can be used for the circuit with the clock frequency of more than 16MHz. If MCM technology is used, the high-end clock frequency of computer workstations can reach 100MHz, and the additional power consumption caused by parasitic reactance can be reduced by 2-3 times.
Fourth, improve productivity and realize automated production
At present, the perforated installation circuit board to achieve full automation, but also need to expand 40% of the original circuit board area, so as to enable the automatic plug-in cartridge head to insert components, otherwise there is not enough space clearance, will damage the parts. Automatic SMT machine (SM421/SM411) adopts vacuum nozzle suction and discharge element, the vacuum nozzle is smaller than the element shape, but improve the installation density. In fact, small components and fine - spaced QFP devices are produced by automatic placement machines, in order to achieve full - line automatic production.
Five, reduce costs, reduce expenses
(1) The use of the circuit board area is reduced, the area is 1/12 of the through hole technology, if the use of CSP installation, its area will be significantly reduced;
(2) The number of holes on the circuit board is reduced, saving the cost of repair;
(3) The cost of circuit debugging is reduced due to the improvement of frequency characteristics;
(4) Due to the small size and light weight of chip components, packaging, transportation and storage costs are reduced;
SMT processing technology can save materials, energy, equipment, manpower, time, etc., can reduce the cost up to 30%~50%.
Shenzhen kingford PCB design capability
Maximum signal design rate: 10Gbps CML differential signal;
Maximum number of PCB design layers: 40;
Minimum line width: 2.4mil;
Minimum line spacing: 2.4mil;
Minimum BGA PIN spacing: 0.4mm;
Minimum mechanical hole diameter: 6mil;
Minimum laser drilling diameter: 4mil;
Maximum number of pins:; 63000 +
Maximum number of components: 3600;
Maximum number of BGA: 48+.
PCB designservice process
1. Schematic diagram provided by the customer to consult circuit board design;
2. Evaluate quotation according to schematic diagram and customer design requirements;
3. The customer confirms the quotation, signs the contract and pays the project deposit;
4. Received advance payment and arranged engineer design;
5. After the design is completed, provide the screenshot of the document to the customer for confirmation;
6. The customer confirmed OK, settled the balance, and provided circuit board design data.