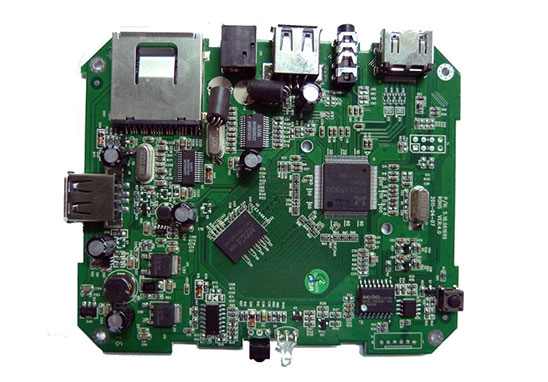
Shenzhen kingford is a PCBA processing manufacturer with its own PCB board factory and SMT patch processing plant. It can undertake the manufacturing and materials contract of Guangzhou PCBA, and provide PCB design, PCB board making, component purchasing, SMT patch, DIP plug-in, PCBA testing, finished product assembly and other one-stop PCBA processing services.
What is PCBA contract labor and materials?
PCBA contract means that customers provide a full set of materials, and PCBA manufacturers provide one-stop services such as electronic component procurement, PCB procurement, SMT patch processing, DIP plug-in processing and PCBA testing. Customers only need to provide complete information (such as PCB file, BOM form, coordinate file, mounting file, etc.), then they can wait for the goods. This is a popular electronic processing mode nowadays, which is favored by more and more customers. The processing mode of PCBA can save the tedious work of parts procurement, plate making and other links.
PCBA labor and material contracting matters needing attention
1. Circuit design
For a PCBA, good circuit design is the foundation of success, and it is the most basic to carry out circuit design according to the actual needs of the product. However, some engineers forget to consider the actual processing difficulty in the process of circuit design. The same function of the board due to different processing difficulties need to pay the processing costs must be different, and is not conducive to electronic processing circuit boards in the process of processing will encounter some obstacles to processing efficiency and actual performance problems.
2. Selection of materials
For PCBA contract materials materials is one of the key factors to ensure quality, circuit board materials, the selection of electronic components and so on. If you want to produce a high-quality board in the selection of materials is very important, the process and materials of the board can be directly requested, the procurement of components can be given the standard and price range, important components can also be directly designated supplier brand. In the quotation of contracted labor and materials, it is often the case that the quotation is higher than the psychological price of the commissioned processing party, which actually requires targeted communication between the research and development enterprises and the PCBA processing plant. The quality of high-quality components is difficult to buy with the price of inferior products. The need to control the cost also needs to communicate with the purchasing staff of the processing plant, in order to ensure the quality of the product plan, how to reduce the cost is also a technical work.
3. Selection of PCBA factory
In the final analysis, the choice of PCBA factory is the most important thing. A reliable processing plant may not be able to offer attractive prices, but can provide reassuring services. Rich processing experience and responsible service attitude, timely response in emergencies and provide practical solutions, these are an important sign of whether a PCBA processing plant is reliable
PCBA contract process
1. Customers place orders
Customers place orders according to their actual needs of PCBA processing plants, and put forward specific requirements. The processing plant will evaluate its capacity to see if it can fulfill the order. If the manufacturer is sure that they can complete the order within the expected time, then the two parties will negotiate to determine the production details.
2. Production materials provided by customers
After the customer decides to place an order, he shall provide a series of documents and lists to the PCBA processing plant, such as PCB electronic files, coordinate files, BOM list and so on, which must be provided.
3. Purchase raw materials
PCBA processing plant purchases relevant raw materials from designated suppliers according to the documents provided by customers.
4. Incoming material inspection
Before PCBA processing, strict quality inspection is carried out for all raw materials to be used to ensure that they are qualified before being put into production.
5. PCBA production
In the process of PCBA processing, in order to ensure the quality of production, whether it is patch or welding production, the manufacturer needs to strictly control the furnace temperature.
6. PCBA test
The PCBA processing plant conducts rigorous product testing, and the PCB board that passes the test is delivered to the customer.
7. Packaging after sale
After the PCBA processing is completed, the products are packaged and then handed over to the customer to complete the whole PCBA processing.
2. PCB copy board company detailed the method of disassembling integrated circuit
kingford is a circuit board copying team with more than 10 years of actual experience in circuit board copying. Kingford can provide circuit board copying solutions, such as circuit board modification, schematic copy, chip model identification, chip decryption, circuit board copying proofing, PCBA OEM and materials.
In the process of PCB board copying, it is also an important subject to remove the integrated circuit on the PCB board correctly because the circuit board needs to be split, the integrated circuit and other components need to be removed to make BOM list, and the bare PCB board from which the split is to be scanned and copied.
Not only in the PCB board copy process, is in the circuit maintenance, often need to remove the integrated circuit from the printed circuit board, and because the IC pins are more and more dense, it is difficult to disassemble, sometimes will damage the integrated circuit and circuit board. Here, we provide several accurate disassembly integrated circuit effective methods, hope to help you.
Circuit board copying method for disassembling integrated circuits
1. Tin absorber tin suction disassembly method
Use a tin absorber to disassemble the integrated block, which is a common professional method. The tool used is an ordinary suction and welding dual-purpose electric iron, with a power of more than 35W. When removing the integrated block, just place the heated dual-purpose electric soldering iron head on the pin of the integrated block to be removed. After the solder joint is melted and sucked into the fine tin, the integrated block can be removed after the solder of all the pins are sucked.
2. Medical hollow needle disassembly method
Take a couple of medical 8 to 12 hollow needles. When used, it is appropriate that the inner meridian of the needle just covers the pin of the integrated block. When disassembling, melt the pin solder with the soldering iron, cover the pin with the needle in time, then remove the soldering iron and rotate the needle, and pull out the needle after the solder solidifies. So the pin is completely separate from the board. Once all the pins have been done this way, the block can be easily removed.
3. Electric soldering iron brush with disassembly method
This method is simple and easy to do, as long as you have an electric iron and a small brush. When disassembling the integrated block, the electric iron is heated first. When the soldering tin on the pin is melted at the temperature of dissolving tin, the dissolved solder is swept away with the brush. This allows the pin of the integrated block to be separated from the circuit board. The method can be carried out separately or separately. Finally, pry off the block with pointed tweezers or a small "one" flathead screwdriver.
4. Add solder melting disassembly method
This method is a convenient method. As long as some solder is added to the pins of the integrated block to be dismantled, the solder joints of each column of pins are connected, so as to facilitate heat transfer and facilitate disassembly. When disassembling, each row of pins heated by electric iron should be pry with pointed tweezers or small "one" flat-head screwdriver. The two rows of pins should be heated alternately until removed. In general, each column of pins can be removed by heating twice.
5. Multi-strand copper wire tin absorption disassembly method
Is the use of multiple strands of copper core plastic wire, remove the plastic skin, the use of multiple strands of copper core wire (short wire can be used). Before use, put the rosin alcohol solution on the multiple strands of copper core wire. After the electric soldering iron is heated, put the multiple strands of copper core wire on the integrated block pin for heating, so that the tin welding on the pin will be absorbed by the copper wire, and the part that absorbs the solder can be cut off. Repeat several times and all the solder on the pin can be sucked away. Braided wire in shielded wire can also be used if possible. As long as the solder is sucked up, gently pry with tweezers or a small "one" screwdriver, the integrated block can be removed.
Why ford?
1. Strength guarantee
▪SMT workshop: We have imported SMT machines and several sets of optical inspection equipment, with a daily output of 4 million. Each process is equipped with QC personnel, who can keep an eye on product quality.
▪DIP production line: We have two wave-soldering machines, among which there are more than 10 old employees who have worked for more than three years. The skilled workers can weld all kinds of plug-in materials.
2. Quality assurance, cost-effective
▪ High-end equipment can stick precision shaped parts, BGA, QFN, 0201 materials. Can also template patch, loose material hand.
▪ Sample and size batch can be produced, proofing from 800 yuan, batch 0.008 yuan/point, no start-up fee.
3. Rich experience in SMT and welding of electronic products, stable delivery
▪ Accumulated SMT SMT processing services for thousands of electronic enterprises, involving many kinds of automotive equipment and industrial control motherboard. The products are often exported to Europe and the United States, and the quality can be affirmed by new and old customers.
▪ On time delivery, normal 3-5 days after complete materials, small batch can also be expedited on the same day shipment.
4. Strong maintenance ability and perfect after-sales service
▪ Experienced maintenance engineers can repair all kinds of patch welding caused by bad products, to ensure the connection rate of each piece of circuit board.
▪ 24-hour customer service staff at any time response, the fastest speed to solve your order problems.