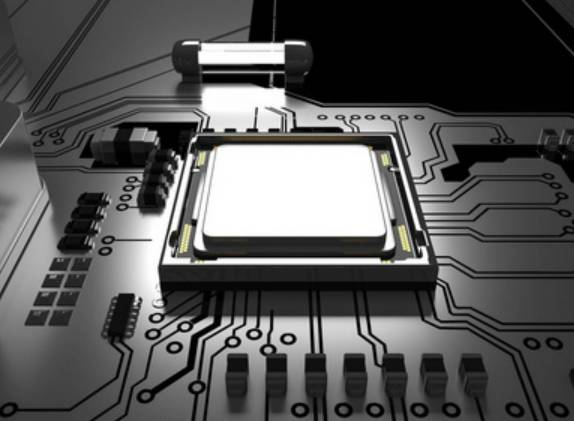
1. Common impedance coupling: It is a common coupling channel, that is, the interference source and the interfered device often share some conductors (such as loop power supply, bus, common ground, etc.).
2. The field common-mode coupling will cause the radiation source to cause common-mode voltage in the loop formed by the interfered circuit and on the common reference surface. If the magnetic field plays a dominant role, the value of the common-mode voltage generated in the series ground loop is Vcm=-(△B/△t)* area (△B = change in magnetic induction intensity in the formula). If it is electromagnetic field, the induced voltage when its electric field value is known: Vcm=(L*h*F*E)/48, the formula is applicable to L(m)=150MHz, beyond this limit, the calculation of the maximum induced voltage can be simplified as: Vcm=2*h*E.
3. Differential mode field coupling: refers to the direct radiation induced by the wire pair or the lead on the circuit board and its loop. If I get as close to the two wires as possible. This coupling is greatly reduced, so the two wires can be twisted together to reduce interference.
4, line coupling (crosstalk) can make any line equal to the parallel circuit between the occurrence of unwanted coupling, serious will greatly damage the performance of the system. It can be divided into capacitive and inductive crosstalk. The former is because the parasitic capacitance between the lines makes the noise on the noise source coupled to the noise receiving line through the current injection. The latter can be thought of as the coupling of signals between the primary stages of an unwanted parasitic transformer. The size of inductive crosstalk depends on the proximity of two loops, the size of the loop area, and the impedance of the load affected.
5. Power cable coupling: It refers to the transmission of electromagnetic interference to other devices by AC or DC power cables.
There are several ways to eliminate crosstalk in PCB design:
1. The size of both types of crosstalk increases with the increase of load impedance, so signal lines sensitive to interference caused by crosstalk should be properly terminated.
2, as far as possible to increase the distance between signal lines, can effectively reduce capacitive crosstalk. Grounding management, spacing between wiring (e.g. isolating the active signal line from the ground, especially between the signal line and ground where the state has changed) and reducing lead inductance.
3. Capacitive crosstalk can also be effectively reduced by inserting a ground wire between adjacent signal lines, which needs to be connected to the formation every quarter wavelength.
4. For perceptual crosstalk, the loop area should be reduced as far as possible, and if allowed, the loop should be eliminated.
5, avoid signal sharing loop.
6, pay attention to signal integrity: the designer should realize the end in the welding process to solve the signal integrity. Designers using this approach can focus on masking the microstrip length of copper foil for good performance of signal integrity. For systems with dense connectors in the communication structure, the designer may use a PCB as the terminator.
Four, electromagnetic interference
As the speed increases, EMI becomes more and more serious and is manifested in many aspects (such as electromagnetic interference at interconnections). High speed devices are particularly sensitive to this, and will thus receive high speed false signals, while low speed devices will ignore such false signals.
The methods of eliminating electromagnetic interference in PCB design are as follows:
1. Reduce loops: Each loop is equivalent to an antenna, so we need to minimize the number of loops, the area of loops and the antenna effect of loops. Ensure that the signal has only one loop path at any two points, avoid artificial loops, and try to use the power layer.
2, filtering: on the power line and in the signal line can take filtering to reduce EMI, there are three methods: decoupling capacitor, EMI filter, magnetic element.
3. Shield. Due to the problem of space and the discussion of the shield of many articles, will not be detailed.
4, try to reduce the speed of high-frequency devices.
5. Increase the dielectric constant of PCB board, which can prevent the high frequency parts such as the transmission line near the board from radiating outward; Increasing the thickness of PCB board and minimizing the thickness of microstrip line can prevent electromagnetic line spillover and also prevent radiation.
In this discussion, we can summarize the following principles that should be followed in the design of high-frequency PCB:
1, power and ground unity, stability.
2. Carefully considered wiring and proper terminating can eliminate reflections.
3. Careful wiring and proper terminating can reduce both capacitive and inductive crosstalk.
4. Noise suppression is needed to meet EMC requirements.