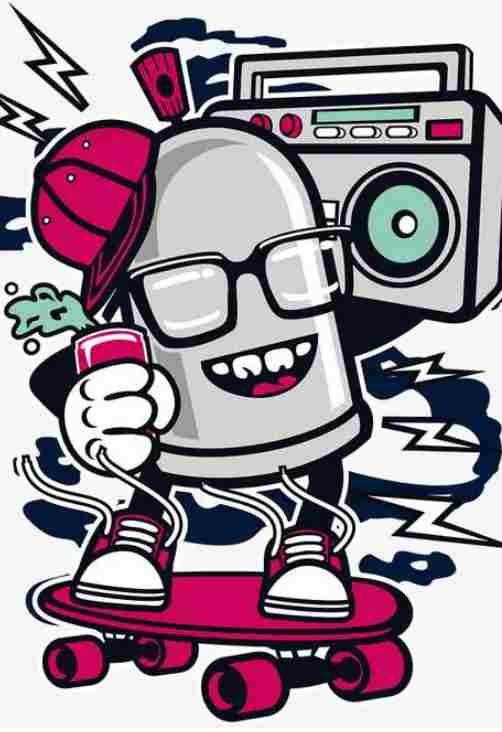
Automatic wiring is a highly configurable tool. To get the most out of them, the wiring parameters have to be set carefully and thoughtfully for each task, even for individual modules in a single pcb design, and there is no basic universal default that is suitable for every occasion.
When you ask an experienced designer "What's the best auto-wiring device?" their usual answer is "the thing between your ears." It's not a joke, they mean it. Wiring, as a process, is as artistic as the algorithm; The wiring itself is heuristic and therefore very similar to traditional backtracking algorithms. For constrained path selection applications (such as mazes and puzzles), backtracking algorithms are good for finding answers, but in open, unconstrained situations, such as printed PCBS with pre-laid components, backtracking algorithms are not good at finding optimal solutions. Unless the constraints of the auto-routing algorithm have been highly fine-tuned by the designer, the auto-routing results still need to be manually checked for weaknesses in the backtracking algorithm results.
Wire size is another difficulty. An automatic wiring device cannot reliably determine how much current will flow through a wire, so it cannot help you determine how wide a wire to use. As a result, most of the automatic wiring out of the wire width does not meet the requirements. Many automatic cablers allow you to specify reference wire constraints. In a forum post on a website, the author wrote, "Every board I've ever made has used an automatic wiring device (excuse me, a very high-end wiring device...). . If your constraints look something like this: only at this level, these two signals form differential pairs, and these networks must match lengths, then you have to tell the autoradier those conditions." When you want to use an autorouter, ask yourself, "How much manual wiring will be done in the time I have to set the autorouter constraints for the pcb, and maybe even set the constraints for each wire in the schematic?"
Experienced designers put a lot of effort into the initial component layout, spending almost half of their design time optimizing the component layout:
Wiring simplification - minimize the crossing of fly lines and so on;
Device proximity - Shorter routes mean better wiring;
Signal timing considerations.
On a user forum, one post reads, "Pay more attention to component layout. Components are laid out in a way that is easier to route. Component layout accounts for 70% of the total effort. Put all the components in place before you start laying the first wire... Use fly lines (which indicate connections that have not yet been wired) as a rough guide to the complexity of wiring."
Old-timers often used a hybrid approach to wiring -- hand-laying a few key lines and locking them when they were done. Automatic wiring is then used to deal with non-critical wires and to help manage the "escape state" in the wiring algorithm. This approach is sometimes a good compromise between controlled manual wiring and fast automatic wiring.
Tip 4
Most people involved in electronics design know that, like a river along its course, electronics can hit choke points and bottlenecks. This point has been directly applied in the design of automobile fuse. By controlling the thickness and shape of the wire (U-bend, V-bend, S-shape, etc.), the fuse that is calibrated under overload will fuse at the throat point. The problem is that pcb designers accidentally produce similar electrical choke points in their pcb designs. For example: use a 90 degree Angle where you can use two quick 45s to form an Angle; The bending degree is greater than 90 degrees, forming the word shape. At best, these wires slow the signal down; In the worst cases, they are like car fuses, which can blow at resistance points.
Tip 5
Oh, the pieces!
Fragmentation is a manufacturing problem that can be best managed with proper pcb design (Figure 1). To understand the fragmentation problem, it is first necessary to review the chemical etching process. The purpose of chemical etching is to dissolve the unwanted copper. But if there are particularly long, thin, strip-like pieces that need to be corroded, these pieces sometimes come apart in one piece before they dissolve completely. The strip then floats in a chemical solution, potentially landing on another pcb at random.
An equally risky situation is when debris remains on the pcb. If the splinter is narrow enough, the acid pool can eat away enough of the copper beneath it to partially peel it off. Now debris is floating around, attached to the pcb like a flag. Eventually it will land on your pcb and cause a short circuit in the other wires.
So where do you look for potential debris and how to avoid it? When designing pcb layout, it is best to avoid leaving a very narrow area of copper sheet (Figure 2). This area is usually created when copper is applied at the junction of the wire and pad clearance (Figure 3). Set the minimum width of the copper sheet to exceed the minimum allowed by the manufacturer, and your design should be free of this problem. The standard minimum width for etching is 0.006 inches.