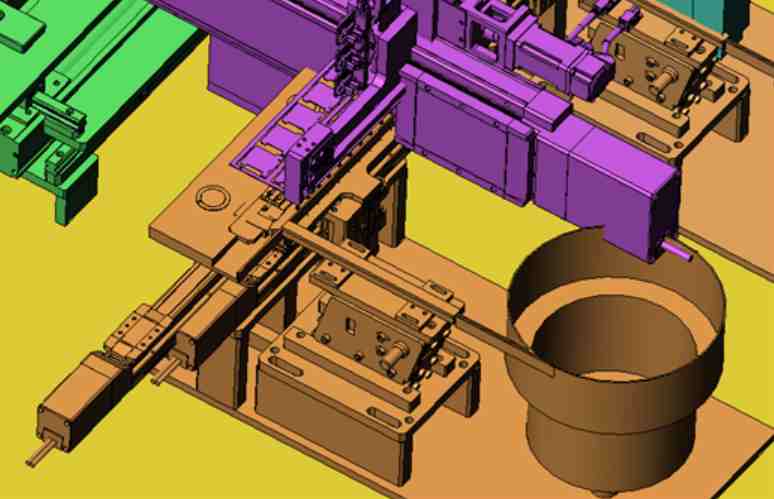
Design rule checks (DRC) are commonly used to input the manufacturer's design constraints, although setting up an automatic routing device is usually done specifically for a specific design function. While this setup is tedious, it's not as bad as an auto-wiring device. Most design teams eventually establish a set of design rules that aim to: standardize bare board construction costs to maximize yield; Assemble, inspect, and test as consistently as possible. In addition to the design benefits, these design rules -- keeping the design within predefined manufacturing limits -- also help establish better consistency in the purchasing department. If the price of pcb manufacturing is consistent, purchasing often reduces the number of specialized pcb manufacturing agreements that need to be maintained.
To help solve all of these problems, many pcb design tools have DRC checkers built in (some tools call them "constraint managers") that interactively flag design rule violations as you edit. Once you have your DRC rules in place for your chosen manufacturer, take errors seriously. DRC tools are generally conservative. They intentionally report possible errors and let you make the decision. It's tedious to sift through hundreds of "possible" problems, but do it anyway. Deep in this list of problems may lie the reasons why the first production is doomed. In addition, if your design generates a large number of possible errors, you should be aware that your wiring may need to be improved.
The designer suggested this. "Take the time to understand and properly set up the constraint system provided by the layout tool. Take the time to review all levels of constraints. Restraint tools can be powerful and flexible, but they can also be confusing and dangerous. Wrong constraints can easily lead to defective or unmanufacturable PCBS. An error in the constraint setting could easily limit the DRC check or make it unusable. It is possible that every time the DRC is passed, the pcb still cannot be manufactured or does not work properly. I've seen this happen before. The design team was happy because the pcb had passed the DRC, but the first product was smoking on the test stand. Tracking this failure takes the team back to the CAD tool's constraint manager. The constraint manager has no design awareness; It will make you do anything, no matter how bad it is."
Almost every day we receive quotation requests for pcb designs that are easy to manufacture, but there are also times when the design tolerances and clearances in critical areas are too small. This situation has forced pcb foundries (such as Sunstone) to deliver the bad news: either we can't make PCBS at all because the tolerance is beyond our capabilities, or we can make PCBS at a higher price and possibly lower yield. If only these customers had designed with the capabilities of the specific manufacturer in mind.
"If your mapping software allows you to suspend DRC violations, be careful when using this feature," he adds. It is easy to forget DRC because of the temptation to leave it for later. Remember to check for all DRC bugs before sending your design out for manufacture."
"Resist the temptation to completely shelve the DRC mistake and follow the rules that were set in the beginning," says the seasoned pcb designer.
Tip 7
Know the foundry you are using
After discussing DRC setup, this tip is almost -- but not entirely -- redundant. In addition to helping you establish the DRC rules correctly, knowing which OEM your pcb will be shipped to can also provide some additional pre-manufacturing assistance. A good foundry will offer helpful help and advice before you place your order, including how to improve your design to reduce design iteration, reduce final debugging problems on the test bench, and improve pcb yield.
Hugo, a doctoral student at Carnegie Mellon University, blogs about what he knows about manufacturers:
"Each manufacturer has its own specifications, such as minimum wire width, spacing, number of layers, etc. Before you start designing, you should consider your own requirements and find a manufacturer that will meet your requirements. Your requirements also include pcb material grade. pcb material grades range from FR-1 (paper-phenolic resin mixture) all the way up to FR-5 (fiberglass and epoxy). Most pcb prototype manufacturers use the FR-4, but the FR-2 is also often used in high-volume consumer applications. The type of material affects the pcb's strength, durability, moisture absorption and flame retardant (FR)."
Understanding the manufacturing process of printed PCBS and knowing which processes and methods your manufacturer will use can help you make better design decisions. Visit the supplier of your choice and see for yourself the manufacturing process. Take advantage of DFM (Design for Manufacturability) tools before submitting your design to manufacturing.
Summary of this article
If you're thinking about these basic tips and techniques, you're already well on your way to fast, reliable, professional-quality PCBS. Understand the manufacturing process; Using DRC and DFM helps you catch inadvertentive design features that can increase foundry costs and/or decrease yield. Then carefully plan the layout of the components, eliminating expensive design features. Use all the design tools provided by CAD tools wisely, including automatic layout and automatic wiring, but be patient and thorough in setting up the automatic wiring, so as to achieve good automatic wiring results.
Don't rely on the auto cabler for anything other than wiring; Adjust wire size manually as needed to ensure the correct current is carried in the design. Trust the fly wire anyway, your pcb design is not complete until 100% of the fly wire is gone.