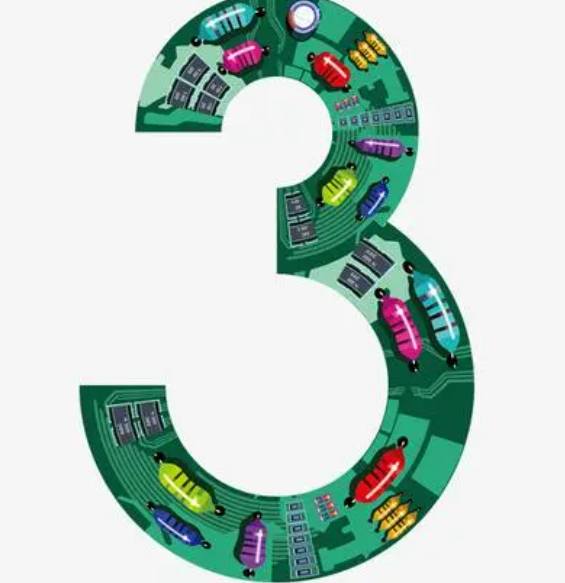
Simple characteristic impedance model: Z=V/I, where Z represents the impedance at each step of the signal transmission process, V represents the voltage at which the signal enters the transmission line, and I represents the current. I=±Q/±t, where Q is the charge and t is the time of each step.
Power (from the battery) : ±Q=±C×V, C represents capacitance, V represents voltage. Capacitance can be derived from the capacity per unit length of the transmission line (CL) and signal transmission speed (v). The length value of the unit pin is taken as the speed, and then multiplied by the required time t of each step, the formula can be obtained: ±C=CL×v×(±)t. Comprehensive above, we may safely draw the characteristic impedance, Z = V/I = V/(+ Q / + t) = V/(x + C V / + t) = V/(CL * V/V * (+) t + t) = 1 / (CL (V)
It can be seen that the characteristic impedance is related to the capacity per unit length of the transmission line and the speed of signal transmission. In order to distinguish the characteristic impedance from the actual impedance Z, we add 0 after Z. The characteristic impedance of the transmission line is: Z0=1/(CL×v)
If the capacity per unit length of the transmission line and the signal transmission speed remain constant, then the characteristic impedance of the transmission line also remains constant. This simple statement connects the common sense of capacitance with the newly discovered theory of characteristic impedance. If the unit length capacity of the transmission line is increased, such as the thickened transmission line, the characteristic impedance of the transmission line can be reduced.
Measurement of characteristic impedance
When the battery is connected to the transmission line (assuming the impedance is 50 ohms at the time), attach an ohm meter to the 3-foot RG58 cable. How do you measure the infinite impedance? The impedance of any transmission line is time dependent. If you measure the impedance of the cable in a shorter time than it reflects, you measure the "surge" impedance, or characteristic impedance. But if you wait long enough until the energy is reflected back and received, the impedance can be measured to change. In general, impedance values bounce up and down to a stable limit.
For a 3-foot cable, impedance measurements must be completed within 3 nanoseconds. TDR(Time domain reflectometer) can do this by measuring the dynamic impedance of a transmission line. If you measure the impedance of a three-foot cable in one second, the signal will bounce back and forth millions of times, giving you a different "surge" impedance.
Details of the three factors that cause circuit board welding defects
The welding defects of circuit boards are caused by the following three factors:
1. The weldability of circuit board holes affects the welding quality
Poor weldability of circuit board holes will produce virtual welding defects, affect the parameters of components in the circuit, lead to the instability of multilayer components and inner wire conduction, and cause the functional failure of the entire circuit. The so-called welderability is the property of the metal surface being wetted by molten solder, that is, the metal surface where the solder forms a layer of relatively uniform continuous smooth adhesion film.
The main factors affecting the weldability of printed circuit board are:
(1) the composition of the solder and the nature of the solder. Solder is an important part of the chemical process of welding. It is composed of chemical materials containing flux. The common low melting point eutectic metal is Sn-Pb or Sn-Pb-Ag. The content of impurities should be controlled by a certain proportion to prevent the oxides produced by impurities from being dissolved by flux. The function of flux is to help solder wet the circuit surface of the plate by transferring heat and removing rust. White rosin and isopropyl alcohol solvents are commonly used.
(2) Welding temperature and metal surface cleanliness will also affect the weldability. The temperature is too high, the solder diffusion speed is accelerated, at this time has a high activity, will make the circuit board and solder melt surface rapid oxidation, welding defects, circuit board surface pollution will also affect the weldability resulting in defects, these defects include tin bead, tin ball, open circuit, glossiness is bad.
2. Welding defects caused by warping
Circuit boards and components in the process of welding produce warping, due to stress deformation and produce defects such as welding, short circuit. Warping is often caused by an imbalance in temperature between the upper and lower parts of the board. For large PCB, due to the weight of the board falling will also produce warping. A common PBGA device is about 0.5mm away from the PCB. If the device on the PCB is large, the solder joint will remain under stress for a long time as the PCB is cooled and returns to its normal shape. If the device is raised 0.1mm, it will be enough to cause a virtual weld to open.
3. The design of circuit board affects the welding quality
In the layout, the size of the circuit board is too large, although welding is easier to control, but the printing line is long, the impedance increases, the anti-noise ability decreases, the cost increases; After hours, the heat dissipation decreases, welding is not easy to control, easy to appear adjacent lines interference with each other, such as the electromagnetic interference of the circuit board. Therefore, PCB board design must be optimized:
(1) Shorten the connection between high-frequency components and reduce EMI interference.
(2) Large weight (such as more than 20g) components, should be fixed with a support, and then welded.
(3) Heat dissipation of the heating element should be considered to prevent defects and rework caused by large ΔT on the surface of the element. The thermal sensitive element should be far away from the heating source.
(4) the arrangement of components as parallel as possible, so not only beautiful and easy to weld, suitable for mass production. Circuit board design is the best 4∶3 rectangle. Do not mutate the wire width to avoid discontinuity in the wiring. When the circuit board is heated for a long time, copper foil is easy to expand and fall off. Therefore, large area copper foil should be avoided.