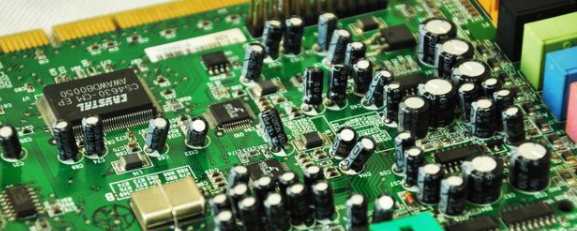
The circuit board of our common electronic products, that is, we often say PCBA, is manufactured by SMT patch processing and DIP plug-in processing. Due to the fine and integrated components of the patch in PCBA processing, especially for SMT patch processing technology is relatively technical content. In order to ensure the patch processing quality intact, we must master the corresponding technical points. Next, Shenzhen patch processing manufacturer -kingford- share SMT patch processing technology points with you, I hope to bring you some help!
I. Main points of solder paste printing technology
1, the Angle of the printing press scraper and steel mesh: the smaller the Angle of the scraper and steel mesh, the greater the pressure of the scraper, easy to squeeze the solder paste to the bottom of the steel mesh, causing tin short circuit. Steel mesh scraper Angle is generally 45~60°
2. Scraper pressure: Scraper pressure refers to the depth of the scraper falling to the steel mesh surface, which is also an important factor affecting the printing quality. When the pressure is too small, the scraper is not close to the steel mesh surface, so it is equivalent to increasing the thickness of solder paste printing. Moreover, a layer of solder paste remains on the surface of the steel mesh, which is easy to cause the pointed defect of the printed solder paste when demoulding.
3, scraper speed: scraper running speed and solder paste viscosity is inversely proportional. When PCBA has a narrow spacing pad, the printing speed should be slow, the speed is too fast, the shorter the time that the scraper passes through the steel mesh opening, the solder paste can not fully penetrate into the steel mesh. Easy to cause solder paste printing is not full or leakage defects.
4. Printing gap: printing gap is the fit degree between steel mesh and PCB, which is related to the storage of printing solder paste on PCBA pad. The fit between the two is too tight, easy to cause deformation of steel mesh. On the contrary, it is easy to cause the printing solder paste to be too thick, and it is easy to form short circuit.
5. Demoulding speed: The instant speed of steel mesh leaving PCBA after solder paste printing is completed is the demoulding speed, which is an important parameter related to the printing quality. Demoulding speed is too fast, the adhesive force of solder paste will be reduced, easy to cause the phenomenon of solder paste wire drawing or point pulling.
Two, SMT SMT machine technical points
SMT machine is one of the key equipment in SMT processing. Because of the high speed, high efficiency, stable performance, to our PCBA processing has brought a huge advantage. SMT machine technology points can be summarized in three words: accurate patch, patch good, patch fast.
(1) Correct installation of components: The type, size, resistance value and polarity of components on each side of the PCBA surface shall meet the requirements of the assembly drawing and BOM list, and shall not be pasted incorrectly. ② Accurate component mounting: Component mounting should be aligned and centered with PCBA screen printing as far as possible. For more precise devices, the actual printed solder paste graphic alignment shall prevail.
2. Good patch: ① do not damage components: the patch machine may damage components when picking up and mounting because of the error of the feeder, components and printed board, leading to the failure of the patch. (2) Suitable patch pressure: the patch pressure should be suitable, the patch pressure is too small, the welding end or pin of the components float on the surface of the solder paste, the solder paste does not stick to the components, and the azimuth movement is easy to occur when transferring and reflow welding; Too much pressure on the patch, too much extrusion of solder paste, simple adhesion of solder paste, easy short circuit during reflow welding, too much pressure will even damage components. ③ Guarantee the mounting rate: because the parameter adjustment of the mounting machine is unreasonable or the reason of the feeder, the components fall in the mounting process, this phenomenon is called "throwing". In practice, it is measured by the mount rate. When the mount rate is below the booking level, the reason must be found.
3. Fast SMT: Usually, there are hundreds to thousands of electronic components on a PCBA board, which are pasted to the PCBA board one by one through the SMT machine. The mounting speed is the basic requirement of SMT patch production capacity. The mounting speed mainly depends on the speed of the mounting machine, but also closely related to the optimization of the mounting process and the use of equipment.
3, reflow technical points
1. Reasonable reflow welding temperature curve should be set and real-time test of temperature curve should be done regularly. 2, according to the design of PCBA welding direction transmission welding. 3. Prevent the vibration of the conveyor belt during reflow welding. 4. The welding effect of the first printed board must be tested for the mechanical strength of the solder joint. 5. Check whether the welding is sufficient, whether the surface of the solder joint is smooth, whether the shape of the solder joint is in half moon shape, the condition of the tin ball and residue, and the condition of continuous welding and virtual welding.
The above three points are the SMT patch processing technical points shared by kingford
2. Explain the core technology of SMT placing machine
SMT machine is the most important equipment in SMT factory. The principle is to vacuum absorb components through the mounting head, and then mirror the movement of the center point of the identification component coincides with the PCBA coordinates, and finally release the mounting. This process includes the main technology of the whole SMT machine, such as automatic control technology, mechanical motion technology, visual detection and sensing technology, industrial computer and information processing technology, etc. We may rarely really understand the main technology of the SMT SMT machine in the ordinary working process, but whether the SMT SMT machine is advanced or not directly affects the production efficiency and quality of the whole SMT SMT factory, so the efficiency and quality of the production line depends on the speed and quality of the SMT machine. Next, Shenzhen patch processing plant -kingford- to share with you, I hope to bring you some help!
1. Industrial computer and information processing technology
Because the servo control is strict to the real-time requirements of the industrial computer system, at the same time, the chip machine equipment needs to have the ability of multi-task synchronous processing, such as online programming, multi-task interface and real-time work. Therefore, it is necessary to establish a real-time multitasking control model for SMT mounters, which runs on the real-time multitasking operating system and serves as the realization platform for SMT control. Information processing includes information access, exchange, operation, judgment and decision, etc. Computer is the main tool to realize information processing. Information processing technology and computer application are the most active factors to promote the development of SMT machine and electromechanical integration technology. SMT SMT machine control is completed by computer, generally adopt secondary computer control: each machine has its own set of control software, to achieve the control of mechanical structure movement; The master computer uses software to realize programming and man-machine interface. With the vigorous development of computer technology, windows operating system has completely replaced DOS, OS2 and other platforms, which makes the operation of the patch machine more visual and intelligent, the intelligent level of the patch machine has been greatly improved.
2. Mechanical motion technology of the SMT machine
In the SMT process, due to the high-speed operation of the SMT machine, combined with the precision of the mounting components, it is required to implement the high-speed and miniaturization of the parts. The requirements of the mechanical motion part of the SMT machine are as follows: 1. Design, manufacture and assembly technology of micro, precision and high precision mechanical parts; 2, sports machinery express response, low loss, high efficiency, precision positioning mechanism in line with transmission technology; 3, high precision, intelligent, high speed patch technology; The mounting head is an important operating structure of the mounting machine. In order to make the mounting machine run stably and meet the accuracy requirements, the mounting machine is usually driven by ball screw. At present, the guide rail of the SMT machine is generally integral or movable guide rail. The new SMT machine is developing from the traditional single way conveying to the multi-way conveying structure, and the mounting head is also developing to the single head multi-suction nozzle to the multi-suction nozzle.
3. Automatic control technology of SMT machine
The combination of automation control technology and computer control technology has become the most important technology in electromechanical integration equipment. Automatic control technology is the core of the whole SMT placing machine. As the installation efficiency of components is affected by the size of PCBA, the electronic components used and the type of feeder, etc., various factors should be taken into consideration when selecting the type of placing machine. In addition, program optimization should ensure the movement sequence and path of the mounting head in the actual production process. The total travel time of the entire circuit board is the shortest, so as to achieve the most efficient mounting efficiency. Due to the strict requirements on efficiency and precision of SMT mounters, PCBA components shall be mounted and positioned at high speed, and the positioning accuracy shall be maintained within 0.05mm. At the same time, the mounting strength of components also needs to be strictly controlled, so it should meet the requirements of speed, acceleration, vibration, impact and mounting strength. SMT mounters need to establish motion control models and intelligent control strategies to achieve high precision, high efficiency and high speed.
4. Visual detection technology of the patch machine
The research direction of vision detection and sensor technology of SMT machine is sensor and its signal detection device. It is of great significance to develop the research of vision detection and sensor technology for the development of electromechanical integration technology. Because machine vision is advanced in enhancing detectability and improving detection accuracy, so with the improvement of mechanical and electrical automation technology level, machine vision has been widely used in SMT components, SMT product quality detection and other fields. Today, almost all high precision SMT systems include a visual subsystem for positioning. These subsystems are used to detect and process the original position information of the target, obtain the feedback information needed by the computer, and provide accurate data for the precise component mounting. Visual inspection technology can grasp components for accurate positioning and calibration. Because electronic components now have higher and higher requirements for mounting accuracy, the new full-vision technology for surface mounting technology used in high-precision microelectronics equipment adopts high-precision and high-speed image processing and feature extraction methods. In addition, the visual technology can also recognize the image of the mounted IC, which can be used for component classification, waste disposal, etc., to improve the quality and efficiency of the mounted IC. Machine vision detection technology includes: 1. High speed image processing technology for patch; 2. 2. Machine vision high-speed recognition technology; 3, lighting technology, etc. The machine vision of some advanced SMT machines uses flight detection technology to realize positioning correction and defect detection of electronic components. The technology has the ability of real-time detection and positioning in the process of component picking, positioning and mounting, so that the SMT machine can achieve the purpose of improving the mounting efficiency under the condition of ensuring accuracy.
5. Sensor technology of the patch machine
Mounting equipment needs high reliable and high precision electromechanical detection and positioning technology. In order to make the mounting head of the SMT machine work together, the mounting head is installed with a variety of sensors, which are like the eyes of the SMT machine, monitoring the running state of the machine from time to time, and can effectively adjust the working state of the SMT machine. The more sensors are used, the higher the intelligent level of the SMT machine is predicted. The main types of sensors used in the SMT machine are position sensor, negative pressure sensor and pressure sensor. The position sensor is to monitor the limit position of various motion positions; The negative pressure sensor monitors the change of negative pressure. When the nozzle is not sucked or sucked, the negative pressure data is abnormal. The sensor feeds back the abnormal information to the computer, and the system can alarm in time. The pressure sensor is to allow the mounting head to adjust the mounting force when mounting components on the circuit board, so as to avoid excessive damage to PCB or too small mounting force.
The above five points are the core technology of SMT SMT machine shared by kingford. For more knowledge about SMT SMT processing, please visit kingford Shenzhen Co., LTD. One is a professional SMT plant integrating PCB design and manufacture, component collection, SMT patch processing, special process processing and failure analysis, which can meet the needs of various customers. Is your reliable SMT patch processing factory