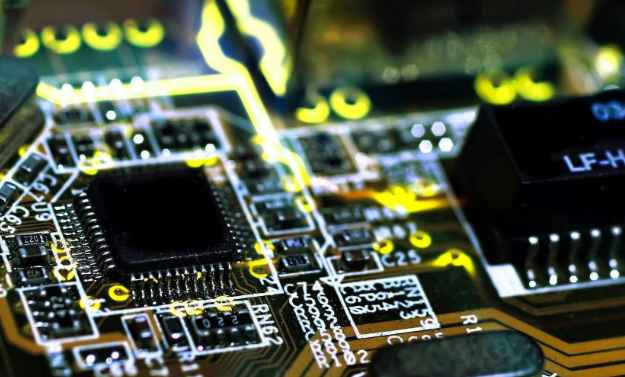
1. Dipping silver (sinking silver)
The silver leaching process is between organic coating and electroless nickel plating/gold leaching, which is simple and fast. It's not as complicated as electroless nickel/gold plating, nor is it a thick coat of armor for the PCB, but it still provides good electrical performance. Silver is the younger brother of gold, able to maintain good solderability even when exposed to heat, humidity and pollution, but tarnish. Silver immersion does not have the good physical strength of electroless nickel/gold plating because there is no nickel underneath the silver layer. Silver immersion is a displacement reaction, it is almost submicron grade sterling silver coating. Sometimes the process of silver leaching also contains some organic matter, mainly to prevent silver corrosion and eliminate silver migration problems; This thin layer of organic matter is generally difficult to measure, and analysis suggests that the organism is less than 1% by weight.
2. Dipping tin (sinking tin)
Since all solder is currently based on tin, the tin layer can be matched to any type of solder. From this point of view, leaching tin process has a very promising development. However, tin whiskers appeared in the previous PCB after leaching process. Tin whiskers and tin migration in the welding process will bring reliability problems, so the use of tin leaching process is limited. Later, organic additives were added to the leaching solution to make the tin layer structure granular structure, overcome the previous problems, but also has good thermal stability and weldability. Tin dipping process can form flat copper-tin intermetallic compounds, which makes tin dipping have the same good solderability as hot air leveling without the headache flat problem of hot air leveling. Tin immersion also does not have the diffusion problem of electroless nickel/gold plating - the copper-tin intermetallic compounds are able to bond firmly together. The tin dipping plate cannot be stored for too long, and must be assembled according to the order of dipping.
3. Other surface treatment processes
The application of other surface treatment processes is less, the following is the application of relatively more nickel gold plating and chemical palladium plating process. Nickel-gold plating is the ancestor of the PCB surface treatment process. It has been around since the appearance of PCBS and has slowly evolved into other methods. It is the PCB surface conductor is first coated with a layer of nickel and then coated with a layer of gold, nickel plating is mainly to prevent the diffusion between gold and copper. There are two types of electroplated nickel gold: soft gold plating (pure gold, the surface of gold does not look bright) and hard gold plating (smooth and hard surface, wear-resistant, containing cobalt and other elements, the surface of gold looks brighter). Soft gold is mainly used in chip packaging gold wire; Hard gold is mainly used for electrical interconnection in non-welded places.
Because of the cost, the industry often uses image transfer for selective plating to reduce the use of gold. Selective electroplating continues to increase in the industry due to the difficulty in controlling the electroless nickel plating/gold leaching process. Under normal circumstances, welding will cause electroplating to become brittle, which will shorten the service life, so avoid welding on electroplating; However, electroless nickel plating/gold leaching rarely occurs because gold is very thin and uniform.
The process of electroless palladium is similar to that of electroless nickel plating. The main process is to reduce palladium ions to palladium on the catalyzed surface by a reducing agent (such as sodium dihydrogen subphosphate). The newly formed palladium can be used as a catalyst to promote the reaction, and thus palladium coatings of any thickness can be obtained. The advantages of electroless palladium plating are good welding reliability, thermal stability and surface flatness.
The choice of surface treatment process mainly depends on the type of final assembly components; Surface treatment process will affect the production, assembly and final use of PCB. The following will specifically introduce the use of five common surface treatment processes.
1. Hot air leveling (spray tin)
Hot air leveling used to be the dominant technology in PCB surface treatment. In the 1980s, more than three-quarters of PCBS used hot-air smoothing, but the industry has been reducing its use over the past decade and estimates that 25% to 40% of PCBS now use hot-air smoothing. Hot air leveling is dirty, smelly, and dangerous, so it has never been a favorite process, but hot air leveling is an excellent process for larger components and more widely spaced wires. In PCBS with high density, the flatness of hot air smoothing will affect subsequent assembly; Therefore, HDI board generally does not use hot air leveling process. With the development of technology, the industry has now appeared the hot-air leveling process suitable for assembling QFPS and BGA with smaller spacing, but the practical application is less.
At present, some factories use organic coating and electroless nickel plating/gold dipping process instead of hot air leveling process; Technological developments have also led to the adoption of tin and silver leaching processes in some factories. Coupled with the trend of lead-free in recent years, the use of hot air leveling is further restricted. Although so-called lead-free hot air smoothing is available, it may involve equipment compatibility issues.