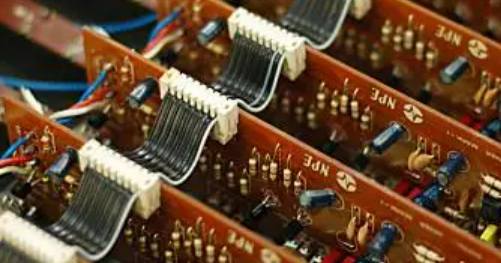
The main factors considered in the design of laminated structure are the heat resistance, voltage resistance, filling amount and dielectric layer thickness of the material, which should follow the following main principles.
(1) Semi-cured sheet and core plate manufacturers must be consistent. In order to ensure PCB reliability, 1080 or 106 semi-cured sheets shall be avoided for all layers (except for special requirements of the customer). If the customer has no requirement of medium thickness, the thickness of medium between each layer shall be guaranteed to be ≥0.09mm according to IPC-A-600G.
(2) When the customer requires high TG plate, the core plate and semi-cured plate shall use the corresponding high TG material.
(3) Inner substrate 3OZ or above, select high resin content semi-cured tablets, such as 1080R/C65%, 1080HR/C 68%, 106R/C 73%, 106HR/C76%; However, the structural design of 106 high-adhesive semi-cured sheets should be avoided as far as possible, so as to prevent multiple pieces of 106 semi-cured sheets from overlapping. Because the glass fiber yarn is too thin, the glass fiber yarn will collapse in the large substrate area, which will affect the dimensional stability and burst plate stratification.
(4) If the customer does not have special requirements, the dielectric layer thickness tolerance between layers is generally controlled by +/-10%. For impedance plates, the dielectric thickness tolerance is controlled by IPC-4101 C/M class tolerance. If the impedance influence factor is related to the substrate thickness, the plate tolerance must also be controlled by IPC-4101 C/M class tolerance.
2.3 Interlayer alignment control
The precision of inner core board size compensation and the control of production size requires accurate compensation of each layer graphic size of high-rise board through the data and historical data experience collected during production for a certain period of time, so as to ensure the consistency of each layer core board growth and shrinkage. Select high precision, high reliability before pressing interlayer positioning methods, such as four slot positioning (Pin LAM), hot melt and rivet bonding. The key to ensure the pressing quality is to set up the appropriate pressing process and daily maintenance of the press, control the merging glue and cooling effect, and reduce the dislocation between layers. The control of interlayer alignment degree should be considered from the compensation value of inner layer, the pressing positioning mode, the pressing process parameters, the material characteristics and other factors.
2.4 Inner circuit process
Since the resolution capacity of the traditional exposure machine is about 50μm, the laser direct imaging machine (LDI) can be introduced for the production of high-rise plate to improve the graphic resolution capacity to about 20μm. The alignment accuracy of conventional exposure machine is ±25μm, and the alignment accuracy between layers is greater than 50μm. Using high precision alignment exposure machine, graphic alignment accuracy can be improved to about 15μm, interlayer alignment accuracy control within 30μm, reduce the alignment deviation of traditional equipment, improve the interlayer alignment accuracy of high layer board.
In order to improve the etching ability of the line, the need in the engineering design of the width of the line and the welding plate (or ring) to give appropriate compensation, but also need to special graphics, such as back circuit, independent line compensation amount to do more detailed design considerations. Confirm whether the design compensation for inner line width, line distance, isolation ring size, independent line, hole to line distance is reasonable, otherwise modify the engineering design. Impedance, inductive design requirements pay attention to independent line, impedance line design compensation is enough, etch control parameters, the first confirmed qualified before mass production. In order to reduce etching side erosion, it is necessary to control the composition of each group of etching solution within the best range. The traditional etching line equipment has insufficient etching ability, so it can be reformed or imported with high precision etching line equipment to improve the etching uniformity and reduce the problems of etching rough edge and unclean etching.
2.5 Pressing process
At present, interlayer positioning methods before pressing mainly include: four-slot positioning (Pin LAM), hot melt, rivet, hot melt and rivet combination. Different product structures adopt different positioning methods. For the high level plate using four slot positioning mode (Pin LAM), or using fusion + riveting production, OPE punching machine out of the positioning hole, punching accuracy control in ±25μm. In the fusion adjustment mechanism, X-RAY should be used to check layer skewness for the first plate, and the layer skewness can be qualified before batch production. During batch production, it is necessary to check whether each plate is fused into the unit to prevent subsequent stratification. The pressing equipment uses a high-performance supporting press to meet the inter-layer alignment accuracy and reliability of high-rise plates.
According to the laminated structure of the high-rise board and the materials used, study the appropriate pressing procedure, set the best temperature rise rate and curve, in the conventional multi-layer circuit board pressing procedure, properly reduce the pressing rate of the pressing board, prolong the high temperature curing time, so that the resin fully flow and cure, while avoiding the problems of sliding plate and dislocation between layers in the pressing process. Material TG value is not the same as the plate, can not be with the grate plate; The plate with ordinary parameters can not be mixed with the plate with special parameters; The performance of different sheets and semi-cured sheets is different. The corresponding sheet semi-cured sheet parameters should be used for pressing. The special materials that have never been used need to verify the process parameters.